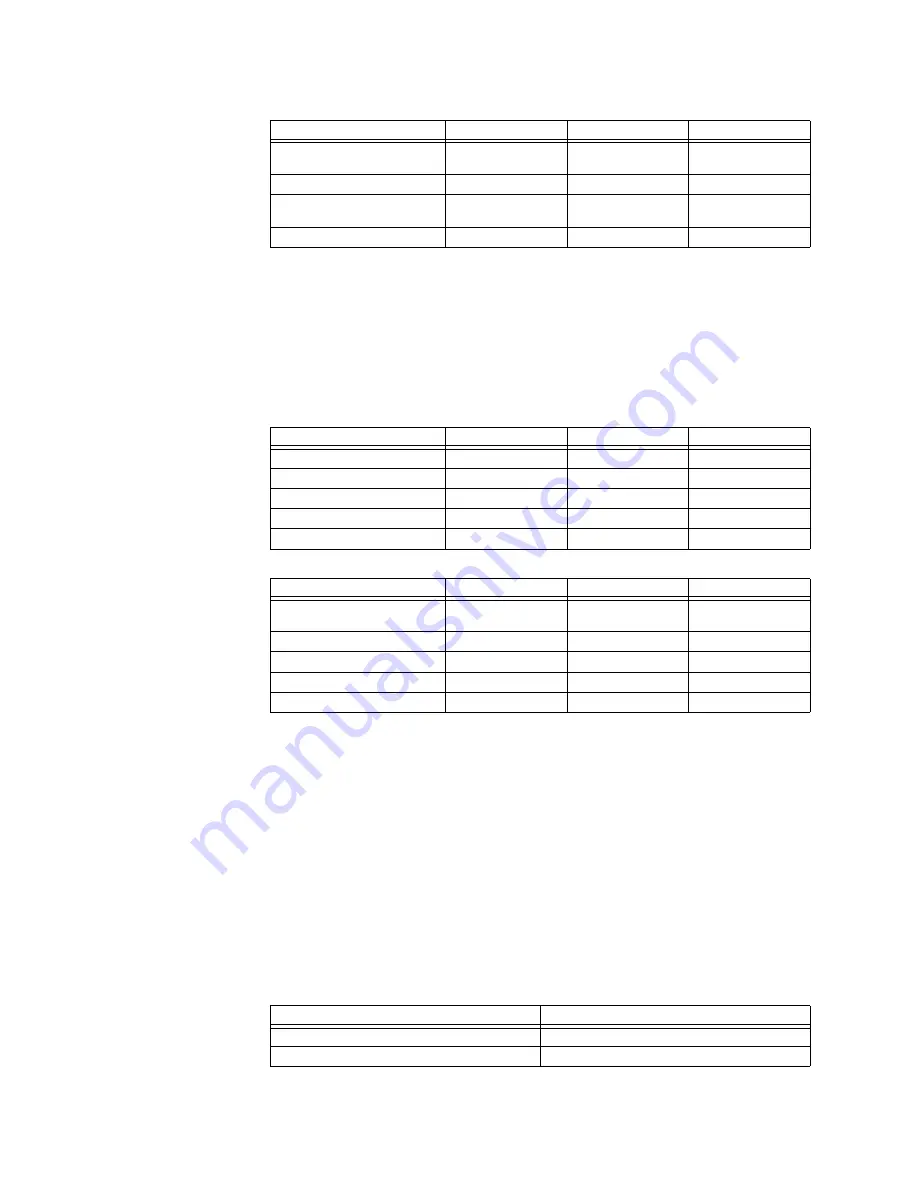
2–8
MM300 MOTOR MANAGEMENT SYSTEM – COMMUNICATIONS GUIDE
MODBUS FUNCTIONS
CHAPTER 2: RS485 INTERFACE (MODBUS RTU)
Function Code 08H
Modbus Implementation: Loopback
Test MM300 Implementation: Loopback Test
This function is used to test the integrity of the communication link. The MM300 will echo
the request.
For example, consider a loopback test from slave 17:
Table 2-7: Master/slave packet format for Function Code 08H
Function Code 10H
Modbus Implementation: Preset Multiple Registers
MM300 Implementation: Store Multiple Setpoints
This function code allows multiple Setpoints to be stored into the MM300 memory. Modbus
“registers” are 16-bit (two byte) values transmitted high order byte first. Thus all MM300
setpoints are sent as two bytes. The maximum number of Setpoints that can be stored in
one transmission is dependent on the slave device. Modbus allows up to a maximum of 60
holding registers to be stored. The MM300 response to this function code is to echo the
slave address, function code, starting address, the number of Setpoints stored, and the
CRC.
For example, consider a request for slave 17 to store the value 00 02 to setpoint address 04
5C and the value 01 F4 to setpoint address 04 5D. After the transmission in this example is
complete, MM300 slave 17 will have the following setpoints information stored:
SLAVE RESPONSE
BYTES
EXAMPLE
DESCRIPTION
SLAVE ADDRESS
1
11
message from slave
17
FUNCTION CODE
1
07
read device status
DEVICE STATUS (see definition
above)
1
2C
status = 00101100 (in
binary)
CRC
2
22 28
CRC error code
MASTER TRANSMISSION
BYTES
EXAMPLE
DESCRIPTION
SLAVE ADDRESS
1
11
message for slave 17
FUNCTION CODE
1
08
loopback test
DIAG CODE
2
00 00
must be 00 00
DATA
2
00 00
must be 00 00
CRC
2
E0 0B
CRC error code
SLAVE RESPONSE
BYTES
EXAMPLE
DESCRIPTION
SLAVE ADDRESS
1
11
message from slave
17
FUNCTION CODE
1
08
loopback test
DIAG CODE
2
00 00
must be 00 00
DATA
2
00 00
must be 00 00
CRC
2
E0 0B
CRC error code
Address
Data
04 5C
00 02
04 5D
01 F4