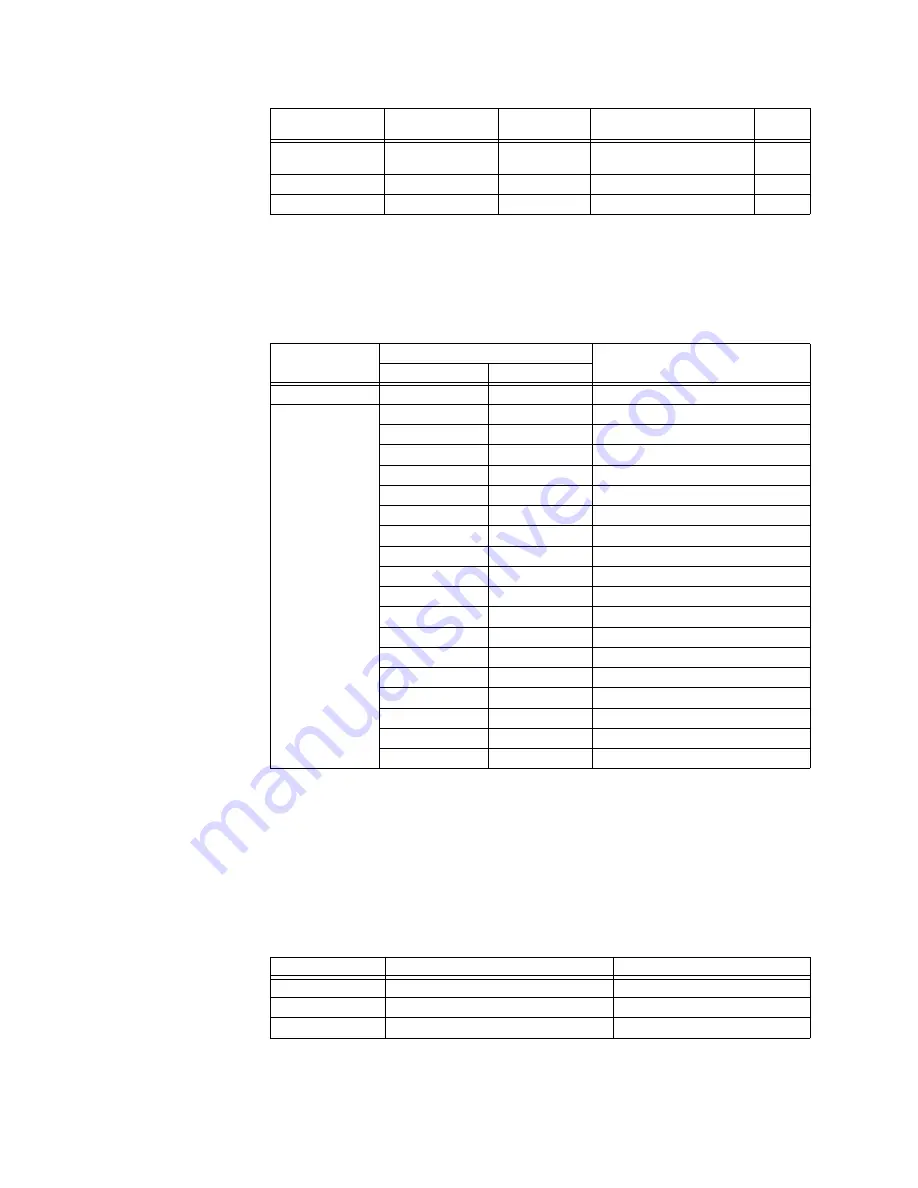
4–10
MM300 MOTOR MANAGEMENT SYSTEM – COMMUNICATIONS GUIDE
PROFIBUS DP
CHAPTER 4: FIELDBUS INTERFACE
Profibus Output Data
The capability to reset, stop, and start the motor has been made available via the Profibus
Output data. Because polled output data is continuously written to the slave device, the
MM300 looks for a change in the value to execute any command.
Profibus DPV0-Diagnostics
The MM300 supports both slave mandatory (6 bytes system-wide standardized) and slave
specific extended diagnostic data. If the diagnostics are considered high priority, the PLC/
host program will be informed of the fault (alarm, trip, command, or message) and can call
a special error routine. When no extended diagnostic information is available and the
master initiates a diagnostics read, only the six standard slave mandatory bytes are read,
formatted as follows:
Table 4-4: System Standard Diagnostics Bytes 1 through 6
Contact Outputs
178
4
Contact Output 32-1 (Bit
Field)
FC167
Virtual Inputs
182
4
Virtual Input 32-1 (Bit Field)
FC167
Virtual Outputs
186
4
Virtual Output 32-1 (Bit Field) FC167
Category
Address (By Bytes) Length in
Bytes
Description
Format
Byte
Value
Description
Dec
Hex
0
0
0x00
Reserved Byte
1
1
0x01
Reset
2
0x02
Lockout Reset
4
0x04
Stop
8
0x08
Start A
16
0x10
Start B
66
0x42
Clear Last Trip Data Prompt
67
0x43
Reset MWh and Mvarh Meters
68
0x44
Clear Counters
69
0x45
Clear Event Records
70
0x46
Clear Waveform Data
71
0x47
Clear Maintenance Timer
72
0x48
Clear RTD Maximums
73
0x49
Reset Motor Information
74
0x4A
Auto Mode
75
0x4B
Manual Mode
80
0x50
Trigger Waveform Capture
81
0x51
Start Datalog
82
0x52
Stop Datalog
Byte
Description
Measured Value
1
Station Status 1
0x08
2
Station Status 2
0x0C
3
Station Status 3
0x00