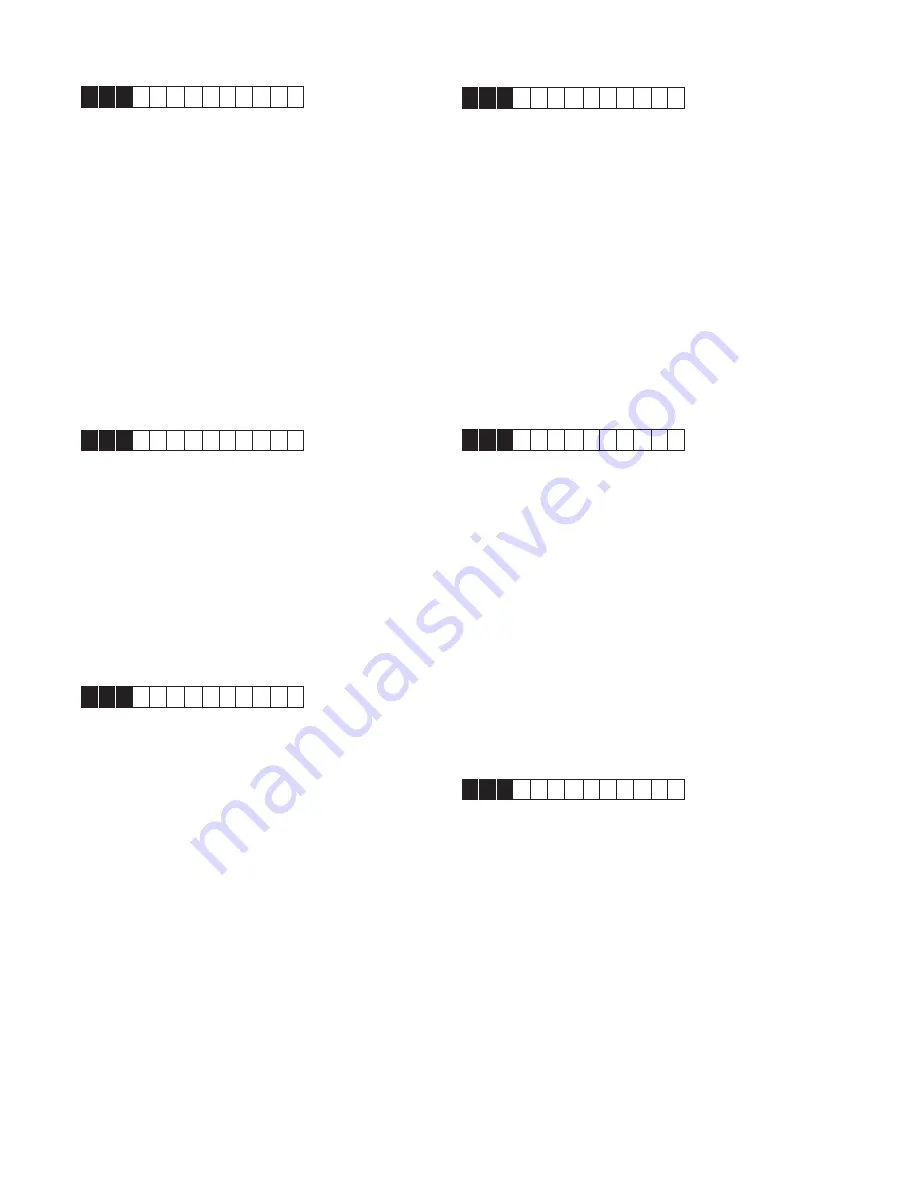
5-36
H13 Auto-restart (Restart time)
H 1 3
R E S T A R T
T
Setting range: 0.1 to 10.0 seconds
Instantaneous switching to another power line (when the
power of an operating motor is cut off or power failure
occurs) creates a large phase difference between the line
voltage and the voltage remaining in the motor, which may
cause electrical or mechanical failure. To rapidly switch
power lines, store the remaining voltage attenuation time
to wait for the voltage remaining in the motor to attenuate.
This function operates at restart after a momentary power
failure.
If the momentary power failure time is shorter than the
wait time value, a restart occurs following the wait time. If
the power failure time is longer than the wait time value, a
restart occurs when the drive is ready to operate (after
about 0.2 to 0.5 seconds).
H14 Auto-restart (freq. fall rate)
H 1 4
F A L L
R A T E
Setting range: 0.00, 0.01 to 100.00 Hz/s
If H14 = 0.00, the frequency is reduced according to the
set deceleration time.
This function determines the reduction rate of the output
frequency for synchronizing the drive output frequency
with the motor speed. This function is also used to
reduce the frequency and thereby prevent stalling under a
heavy load during normal operation.
Note:
A frequency reduction rate that is set too large may
temporarily increase the regeneration energy from the load
and invoke the overvoltage protective function. Con-
versely, a rate that is too small extends the operation time
of the current limiting function and may invoke the drive
overload protective function.
H15 Auto-restart (holding DC voltage)
H 1 5
H O L D
V
Setting range
230V series: 200 to 300V
460 V series: 400 to 600V
This function is used when
F14 Restart after momentary
power failure (operation selection)
is set to 2 (decelera-
tion-to-stop at power failure) or 3 (operation continuation).
Either function starts a control operation if the main circuit
DC voltage drops below the set operation continuation
level.
If power supply voltage to the drive is high, control can be
stabilized even under an excessive load by raising the
operation continuation level. However, if the level is too
high, this function activates during normal operation and
causes unexpected motion. Please contact GE Fuji
before changing the factory default value.
H10 Energy-saving operation
H 1 0
E N E R G Y
S A V
Setting range: 0: Inactive 1: Active
With constant-speed operation at light loads (fixed output
frequency), this function automatically reduces the output
voltage while minimizing the product of voltage and
current (power).
[Exception: If F09 Torque boost 1 = 0.0]
Notes:
Use this function for variable torque loads (e.g., fans,
pumps). If used for a constant torque load or rapidly
changing load, this function causes a delay in control
response.
The energy-saving operation automatically stops during
acceleration and deceleration or when the torque limiting
function is activated.
H11 DEC mode
H 1 1
D E C
M O D E
Setting range:
0: Deceleration-to-stop based on data
set with H07 Non-linear acceleration
and deceleration
1: Coasting-to-stop
This function determines the drive stopping method when
a STOP command is entered.
Note:
This function is effective only when a STOP command is
entered and, therefore, is ineffective if the motor is
stopped by lowering the set frequency.
H12 Instantaneous overcurrent limiting
H 1 2
I N S T
C L
Setting range: 0: Inactive 1: Active
An overcurrent trip generally occurs when current flows
above the drive protective level, following a rapid change
in motor load. The instantaneous overcurrent limiting
function controls drive output and prohibits the flow of a
current exceeding the protective level, even if the load
changes.
Since the operation level of the instantaneous overcurrent
limiting function cannot be adjusted, the torque limiting
function must be used.
Motor generation torque may be reduced when instanta-
neous overcurrent limiting is applied. Set this function to
be inactive for equipment such as elevators, which are
adversely affected by reduced motor generation torque, in
which case an overcurrent trip occurs when the current
flow exceeds the drive protective level. A mechanical
brake should be used to ensure safety.
Summary of Contents for AF-300 P11
Page 1: ...GE Consumer Industrial AF 300 P11 User s Guide ...
Page 35: ...2 18 Data subject to change without notice 7 07 2007 GE Drives Notes ...
Page 37: ...3 2 Data subject to change without notice 7 07 2007 GE Drives Notes ...
Page 53: ...4 16 Data subject to change without notice 7 07 2007 GE Drives Notes ...
Page 62: ...5 9 Frequency Setting Block Diagram ...
Page 66: ...5 13 ...
Page 84: ...5 31 Notes ...
Page 99: ...5 46 Notes ...
Page 109: ...7 8 Data subject to change without notice 7 07 2007 GE Drives Notes ...
Page 115: ...8 6 Data subject to change without notice 7 07 2007 GE Drives Notes ...
Page 123: ...10 6 Data subject to change without notice 7 07 2007 GE Drives Notes ...