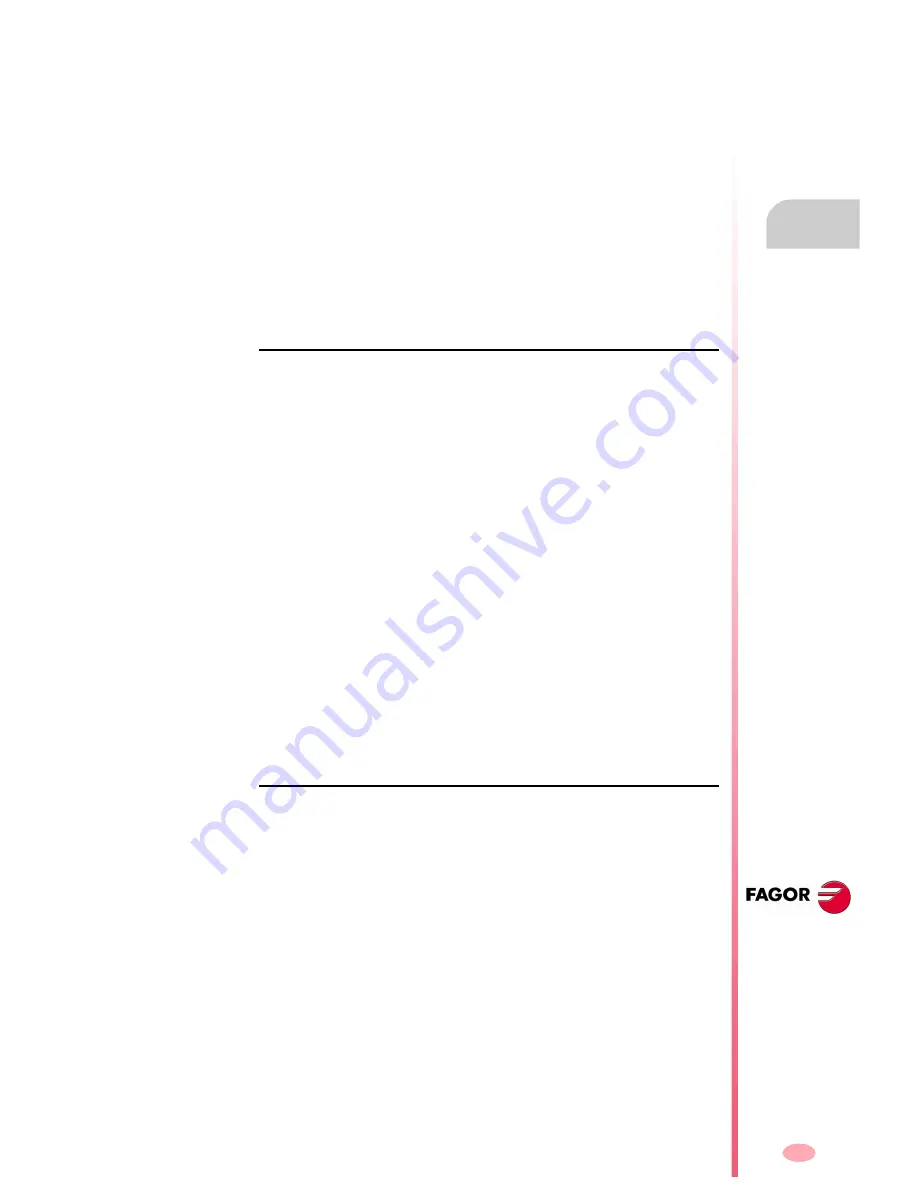
Operating manual
CNC 8070
SETUP ASSI
STANCE
The
ci
rc
ul
ar
it
y (
roundne
ss)
t
e
st
13.
(S
OFT
V03.0
X
)
289
13.3.2 Configuring and executing the circularity (roundness) test
The process consists in executing a circle with the axes of the machine and verifying
it on its graphic representation. The graphic shows the difference between the actual
(real) coordinate obtained from the feedback device and the theoretical coordinate
calculated in that point. This difference is shown projected radially.
The interpolation of the machine axes and the point capture for the graphics are
initiated separately. The data capture is handled from the softkey menu whereas the
movement of the axes is controlled from the operator panel.
The adjustment process is repeated until obtaining the best adjustment of the axes.
The circularity (roundness) test diagram is an assistance tool that only shows the
response of the system to the various settings (adjustments); it is up to the technician
to choose the best adjustment.
How to execute the circularity (roundness) test
Basically it is done as follows. Each of these points is described in more detail in the
indicated chapter.
The configuration used may be saved in a file for later.
1.
Before initiating the process, certain aspects must be configured as well as the
graphic environment, the circular interpolation, the values of the parameters
involved, etc. See
"13.1.4 Machine parameter editing"
on page 277.
A previously saved configuration may be used.
2.
Execute a circular interpolation of the machine axes. The axes must be moving
before the data capture starts. See
"13.3.4 Define and execute the movement
subroutine"
on page 291.
3.
Initiate the data capture and the graphic simulation. Once the axes are moving,
the data capture for the graphics may begin. While capturing data, the position
error at each point is drawn on the graphics. See
"13.3.5 Data capture for the
graphic"
on page 292.
4.
Optimize the adjustment by changing some machine parameters of the CNC or
of the drive. This makes it possible to evaluate the system response to these
changes and optimize the adjustment. See
"13.3.6 Adjustment of the machine
parameters involved"
on page 293.
5.
Save the modified values and the configuration used. See
"13.3.7 Validate the
changes and save the configuration used"
on page 295.
Move through the data
To enter or modify a data, it must be selected; i.e. it must have the editing focus on
it. To select a data, use the [
§
][
¨
][
©
][
ª
] keys.
The data are accepted with the [ENTER] key. Before accepting a data, it is checked
out and if the data is not correct, it is not accepted.
Summary of Contents for CNC 8070
Page 1: ...CNC 8070 REF 0509 SOFT V03 0X OPERATING MANUAL Soft V03 0x Ref 0509...
Page 2: ......
Page 4: ......
Page 6: ......
Page 12: ......
Page 14: ......
Page 16: ......
Page 22: ......
Page 26: ......
Page 28: ......
Page 30: ......
Page 32: ......
Page 34: ......
Page 66: ...Operating manual CNC 8070 2 HOW TO OPERATE THE CNC Keyboard shortcuts SOFT V03 0X 32...
Page 96: ...Operating manual CNC 8070 3 AUTOMATIC MODE Program selection and execution SOFT V03 0X 62...
Page 194: ...Operating manual CNC 8070 7 MDI MODE Full MDI screen SOFT V03 0X 160...
Page 250: ...Operating manual CNC 8070 10 UTILITIES MODE Utilities Softkeys SOFT V03 0X 216...
Page 288: ...Operation manual 8070 CNC 11 PLC Messages service SOFT V03 0X 254...
Page 300: ...Operating manual CNC 8070 12 MACHINE PARAMETERS Operations with tables SOFT V03 0X 266...
Page 346: ...Operating manual CNC 8070 14 DDSSETUP Command generator SOFT V03 0X 312...