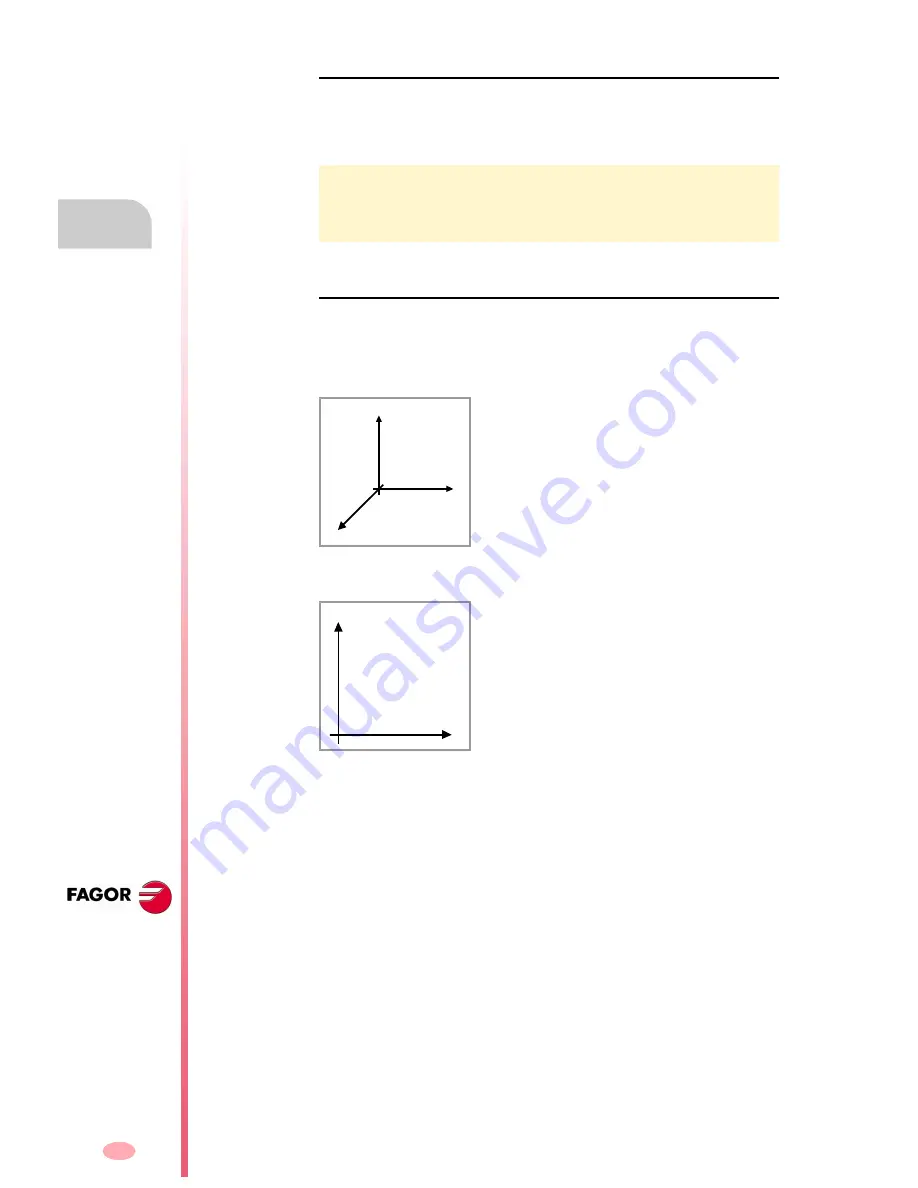
Operating manual
CNC 8070
5.
M
ANUAL
(J
OG
) MODE.
TOOL
CALI
B
RAT
IO
N
(S
OFT
V03.0
X
)
80
Probe selection
Two probes may be configured at the CNC. The probe active at the time is used for
calibration. The active probe may be changed via part-program or MDI using the
instruction
#SELECT PROBE
.
Geometrical configuration of the axes: "plane" or "trihedron".
At the lathe model, the geometrical configuration of the axes may be either of the
"plane" or "trihedron" type depending on the availability of a third main axis, usually
the ·Y· axis. The different calibration modes adapt to the current configuration
showing the necessary data for each one of them.
Configuration of "plane" type axes. The longitudinal axis.
In this configuration, the second axis of the channel is considered as longitudinal axis.
If the X (first) and Z (second) axes have been defined, the work plane will be the ZX
and Z will be the longitudinal axis. Tool length compensation is applied on this
longitudinal axis when using milling tools. With lathe tools, tool length compensation
is applied on all the axes where a tool offset has been defined.
When using milling tools on a lathe, the longitudinal compensation axis may be
changed by means of the #TOOL AX instruction or the G20 function.
#SELECT PROBE [1]
Selects the first probe.
#SELECT PROBE [2]
Selects the second probe.
Geometrical configuration of "trihedron" type
axes.
It is the typical configuration of a milling machine or of
a lathe that has a third main axis (·Y· axis).
There are three axes forming a Cartesian XYZ type
trihedron like on a milling machine. There may be more
axes besides those forming the trihedron.
With this configuration, the planes behave in the same
way as on a milling machine except that the usual work
plane will be G18 (if it has been configured like that).
Geometrical configuration of "plane" type axes.
It is the typical configuration of a lathe.
There are two axes forming the usual work plane. There
may be more axes, but they cannot be part of the
trihedron; there must be auxiliary, rotary, etc.
With this configuration, the active plane will be formed
by the first two axes defined in the channel. If the X (first)
and Z (second) axes have been defined, the work plane
will be the ZX (Z as abscissa and X as ordinate).
The work plane is always G18; the plane cannot be
changed via part-program.
Z
X
Y
Z
X
Summary of Contents for CNC 8070
Page 1: ...CNC 8070 REF 0509 SOFT V03 0X OPERATING MANUAL Soft V03 0x Ref 0509...
Page 2: ......
Page 4: ......
Page 6: ......
Page 12: ......
Page 14: ......
Page 16: ......
Page 22: ......
Page 26: ......
Page 28: ......
Page 30: ......
Page 32: ......
Page 34: ......
Page 66: ...Operating manual CNC 8070 2 HOW TO OPERATE THE CNC Keyboard shortcuts SOFT V03 0X 32...
Page 96: ...Operating manual CNC 8070 3 AUTOMATIC MODE Program selection and execution SOFT V03 0X 62...
Page 194: ...Operating manual CNC 8070 7 MDI MODE Full MDI screen SOFT V03 0X 160...
Page 250: ...Operating manual CNC 8070 10 UTILITIES MODE Utilities Softkeys SOFT V03 0X 216...
Page 288: ...Operation manual 8070 CNC 11 PLC Messages service SOFT V03 0X 254...
Page 300: ...Operating manual CNC 8070 12 MACHINE PARAMETERS Operations with tables SOFT V03 0X 266...
Page 346: ...Operating manual CNC 8070 14 DDSSETUP Command generator SOFT V03 0X 312...