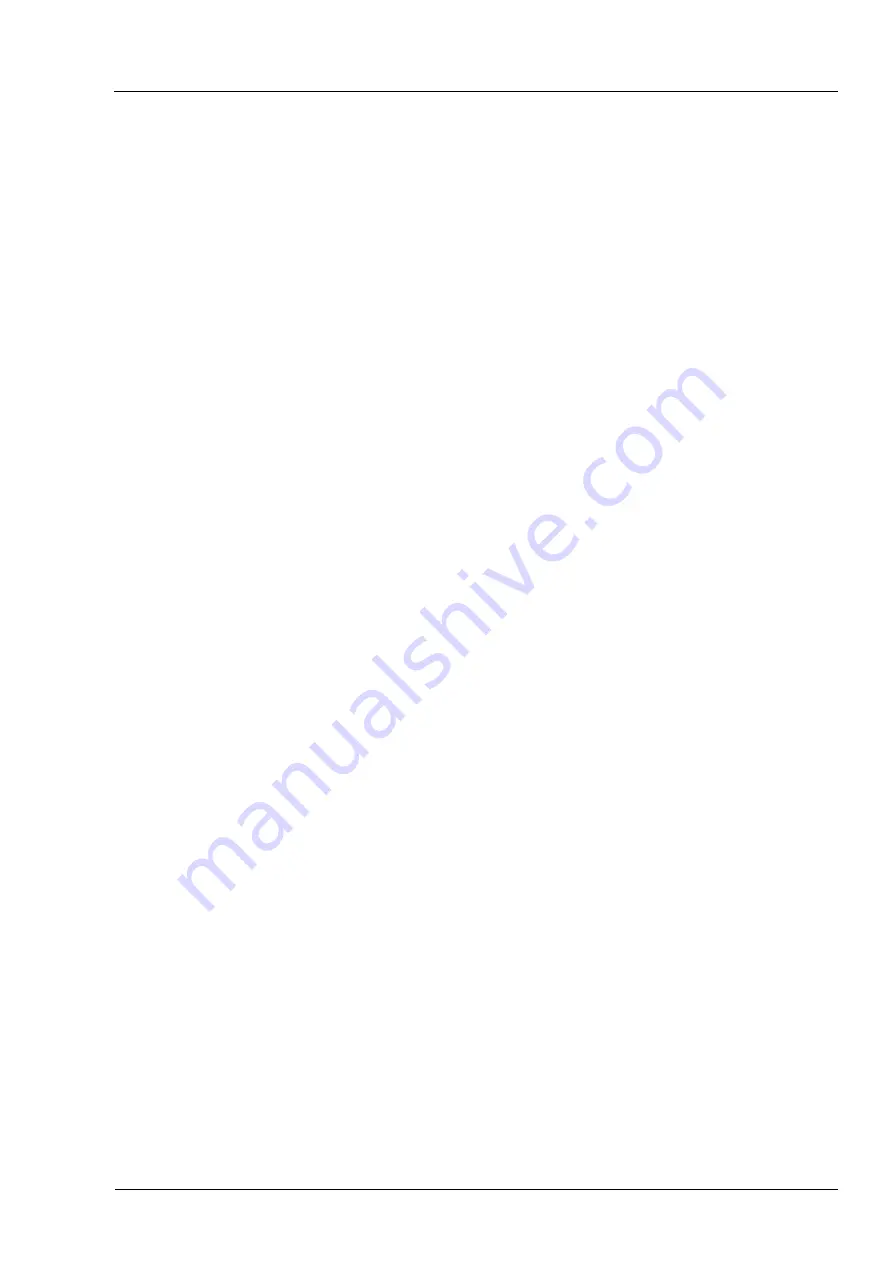
AUSTROMAT
®
624 / 644
7. Maintenance and Service
Operating Instructions (Version 01/2012)
133
7.4. Change
the
heating element
NOTE:
Before each maintenance and service task: Read section 2, Safety. In particular, be aware
of the hazards listed in section 2.4.
NOTE:
If technical servicing or repairs are necessary, they should only be performed by
authorized professionals (see section 7.7).
Over time, the heating element wears out from use. This can have a negative influence on your
firing results. For this reason, change the heating element at the proper time. If the self-check
program is run regularly (see section 7.3), a recommendation will be displayed when the
heating element wear exceeds the permissible limit. Follow the accompanying installation and
safety instructions in section 2 to install the replacement heating element. Heating elements
should only be replaced by trained professionals.
Summary of Contents for AUSTROMAT 624
Page 1: ...Operating Instructions AUSTROMAT 624 644 Version 01 2012 ...
Page 8: ...Table Of Contents AUSTROMAT 624 644 8 Operating Instructions Version 01 2012 ...
Page 146: ...9 Appendix AUSTROMAT 624 644 146 Operating Instructions Version 01 2012 ...
Page 147: ...AUSTROMAT 624 644 9 Appendix Operating Instructions Version 01 2012 147 ...
Page 148: ...9 Appendix AUSTROMAT 624 644 148 Operating Instructions Version 01 2012 ...
Page 149: ...AUSTROMAT 624 644 9 Appendix Operating Instructions Version 01 2012 149 ...
Page 150: ...9 Appendix AUSTROMAT 624 644 150 Operating Instructions Version 01 2012 ...
Page 151: ...AUSTROMAT 624 644 9 Appendix Operating Instructions Version 01 2012 151 ...
Page 152: ...9 Appendix AUSTROMAT 624 644 152 Operating Instructions Version 01 2012 ...
Page 155: ...AUSTROMAT 624 644 10 Index Operating Instructions Version 01 2012 155 ...