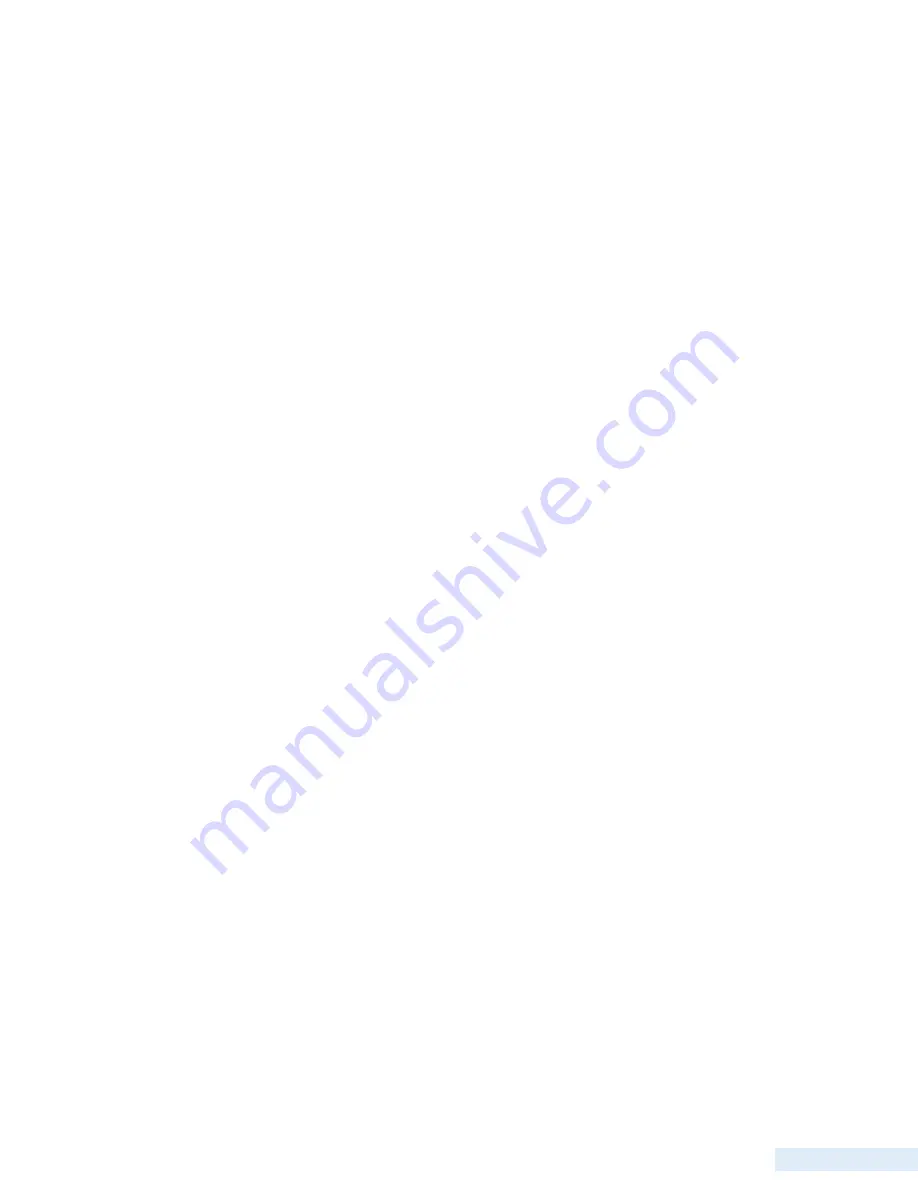
25
U n i t O v e r v i e w
3. Tries the next pump
The preferred method for monitoring motor run is to use phase A at the load side of the motor breaker as motor run bias,
and feed the bias through the starter auxiliary contacts to the TCU’s motor run input terminal with a proper bias resistor
in the circuit. Monitoring the starter auxiliary contacts by using Phase A as bias can provide fault detection of the TCU’s
starter relays, the motor-starter coils, and heater overloads, as well as an open breaker.
Solid State Motor Starter Control Relays
The TCU features three solid-state relays, capable of controlling up to three motor starters. STR_PWR (starter power),
terminal P1-24, will be switched to the starter coils when the TCU’s starter relays are energized, or when the H-O-A
switches are placed in the “Hand” position. The TCU controls 120-240 VAC starter coils, with each output supporting a
maximum of one amp. A one-amp slow-blow fuse is required to protect the TCU’s relays from short-circuited motor-starter
coils. Size 3 or larger starters should be isolated with a relay. If starters are not maintained over time, they can draw over
one ampere.
Auxiliary Input and Output
The TCU’s auxiliary digital input (AUX_IN; P2-12) and output (AUX_OUT; P1-19) can function together as a
programmable time delay relay or work independently as general monitor and control points for telemetry. Additionally,
the auxiliary input can operate as a pulse counter and be used with pulse-type flow meters and rain gauges.
To use AUX_IN and AUX_OUT as general monitor and control points, or to use AUX_IN as a pulse input, the time delay
relay function must be disabled. This is done by setting the function’s delay time to 0 (zero).
Time Delay Relay
An example of an auxiliary relay application is switching on a backup compressor for a bubbler system. The backup
compressor is connected to the AUX_OUT terminal, and an airflow switch for the primary compressor is connected to the
AUX_IN terminal. The Time Delay Relay function can then be configured to turn on the AUX_OUT when the flow switch
detects no airflow. The Time Delay Relay can also be configured to start the backup compressor only when the flow stops
for longer than a set time. This is accomplished by configuring the Time Delay Relay with the ON delay mode and setting
the desired delay time.
Pulse Counting
For the auxiliary input to be used as a pulse input, its corresponding HT3 point (point 12 of Module A, a DMM002) must
be configured as a digital pulse point (select DP for the Point Type). Additionally, the time delay relay function must be
disabled in the TCU.
The specifications for the pulse input are as follows:
• Supply voltage: 8 to 14 VDC
• Minimum pulse width: 25 ms
Alarm Light & Horn/Bell Outputs
The TCU contains two mechanical relays for controlling an alarm light and horn. Alarm devices can be AC or DC powered
for operation during power outages. If the TCU is connected to telemetry, these devices are not necessary and may be
Summary of Contents for TCU800
Page 1: ...Installation and Operation Manual T C U 8 0 0 Data Flow Systems Inc P r e l i m i n a r y ...
Page 2: ...Intentionally left blank ...
Page 4: ...D a t a F l o w S y s t e m s I n c Intentionally left blank ...
Page 8: ...ii Intentionally left blank ...
Page 10: ...ii Intentionally left blank ...
Page 56: ...46 C h a p t e r 5 Quick View Analog View Pump Statistics ...
Page 57: ...47 U s e r I n t e r f a c e Alarms Settings Screen 1 Settings Screen 2 ...
Page 58: ...48 C h a p t e r 5 Advanced Settings About ...
Page 77: ...67 O p e r a t i n g P r o c e d u r e s TCU Installed in Existing Control Panel ...
Page 87: ...77 M o d b u s S u p p o r t Figure 1 Figure 2 Figure 3 ...
Page 92: ...82 D a t a F l o w S y s t e m s I n c Appendix ...
Page 157: ...147 D a t a F l o w S y s t e m s I n c ...
Page 158: ...148 D a t a F l o w S y s t e m s I n c ...
Page 159: ...149 D a t a F l o w S y s t e m s I n c ...
Page 160: ......