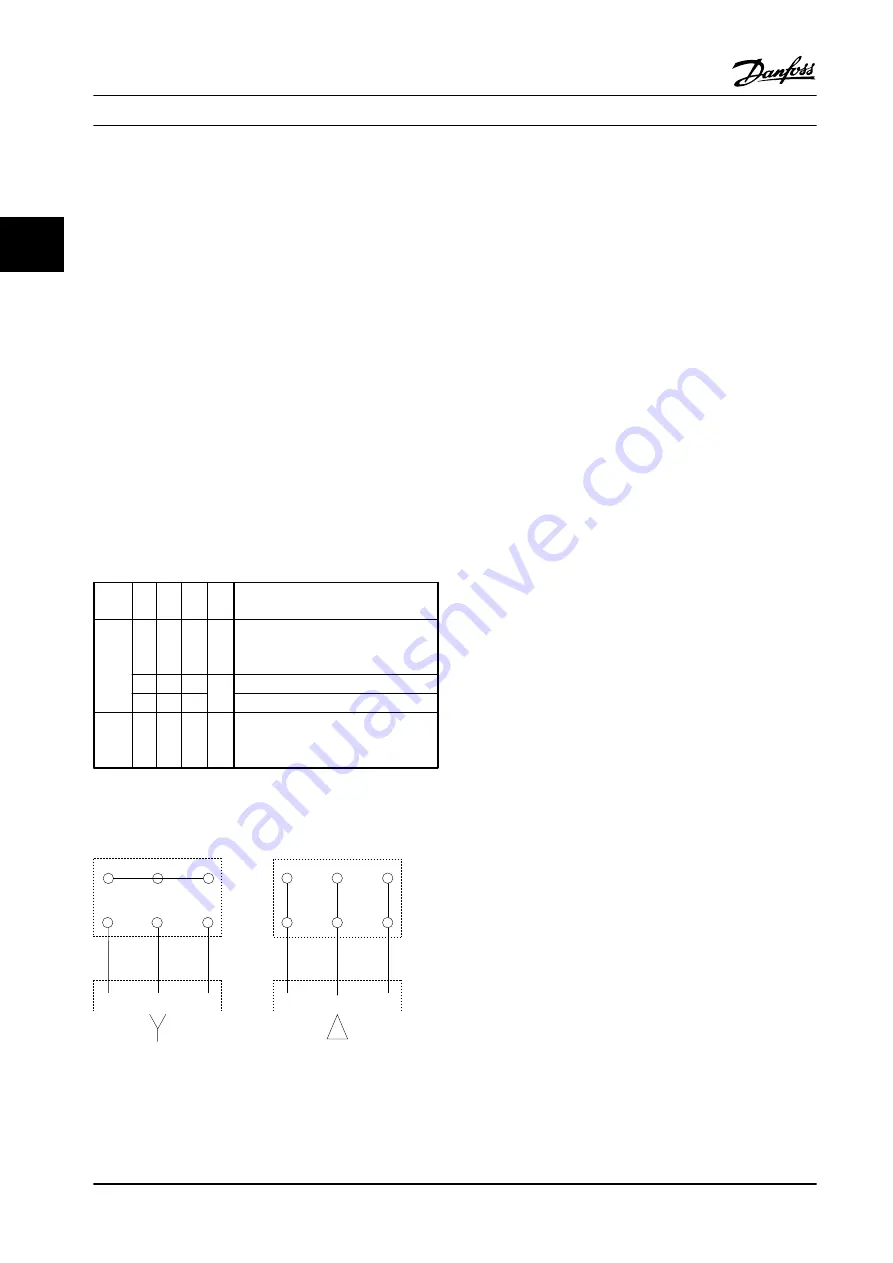
Shielding of cables
Avoid installation with twisted shield ends (pigtails). They
spoil the shielding effect at higher frequencies. If breaking
the shield is necessary to install a motor isolator or
contactor, continue the shield at the lowest possible HF
impedance.
Connect the motor cable shield to both the decoupling
plate of the adjustable frequency drive and to the metal
housing of the motor.
Make the shield connections with the largest possible
surface area (cable clamp). Use the installation devices
within the adjustable frequency drive.
Cable length and cross-section
The adjustable frequency drive has been EMC tested with
a given length of cable. Keep the motor cable as short as
possible to reduce the noise level and leakage currents.
Switching frequency
When adjustable frequency drives are used together with
sine-wave filters to reduce the acoustic noise from a
motor, the switching frequency must be set according to
14-01 Switching Frequency
.
Term.
no.
96 97 98 99
U
V
W PE
1)
Motor voltage 0–100% of AC line
voltage.
3 wires out of motor
U1 V1 W1
PE
1)
Delta-connected
W2 U2 V2
6 wires out of motor
U1 V1 W1 PE
1)
Star-connected U2, V2, W2
U2, V2, and W2 to be interconnected
separately.
Table 3.3 Terminal Connections
1)
Protected Ground Connection
U
1
V
1
W
1
175ZA114.11
96
97
98
96
97
98
FC
FC
Motor
Motor
U
2
V
2
W
2
U
1
V
1
W
1
U
2
V
2
W
2
Figure 3.15 Y and Delta Terminal Configurations
3.4.2 Grounding
Note the following basic issues for electromagnetic
compatibility (EMC) during installation:
•
Safety grounding: The adjustable frequency drive
has a high leakage current and must be
grounded appropriately for safety reasons. Always
follow local safety regulations.
•
High-frequency grounding: Keep the ground wire
connections as short as possible.
Connect the different ground systems at the lowest
possible conductor impedance. Keep the conductor as
short as possible and use the greatest possible surface area
for the lowest possible conductor impedance.
The metal cabinets of the different devices are mounted
on the cabinet rear plate using the lowest possible HF
impedance. Doing so avoids different HF voltages for
individual devices and the risk of radio interference
currents running in connection cables between the
devices. The radio interference is reduced.
To obtain a low HF impedance, use the fastening bolts of
the devices as HF connection to the rear plate. Remove
insulating paint or similar from the fastening points.
3.4.3 Extra Protection (RCD)
ELCB relays, multiple protective grounding, or standard
grounding provide extra protection, if local safety
regulations are followed.
In the case of a ground fault, a DC component develops in
the fault current.
If using ELCB relays, observe local regulations. Relays must
be suitable for protection of 3-phase equipment with a
bridge rectifier and for a brief discharge on power-up.
Installation
Instruction Manual
26
Danfoss A/S © Rev. 2014-02-07 All rights reserved.
MG37A222
3
3
Summary of Contents for VLT AutomationDrive FC 302
Page 2: ......