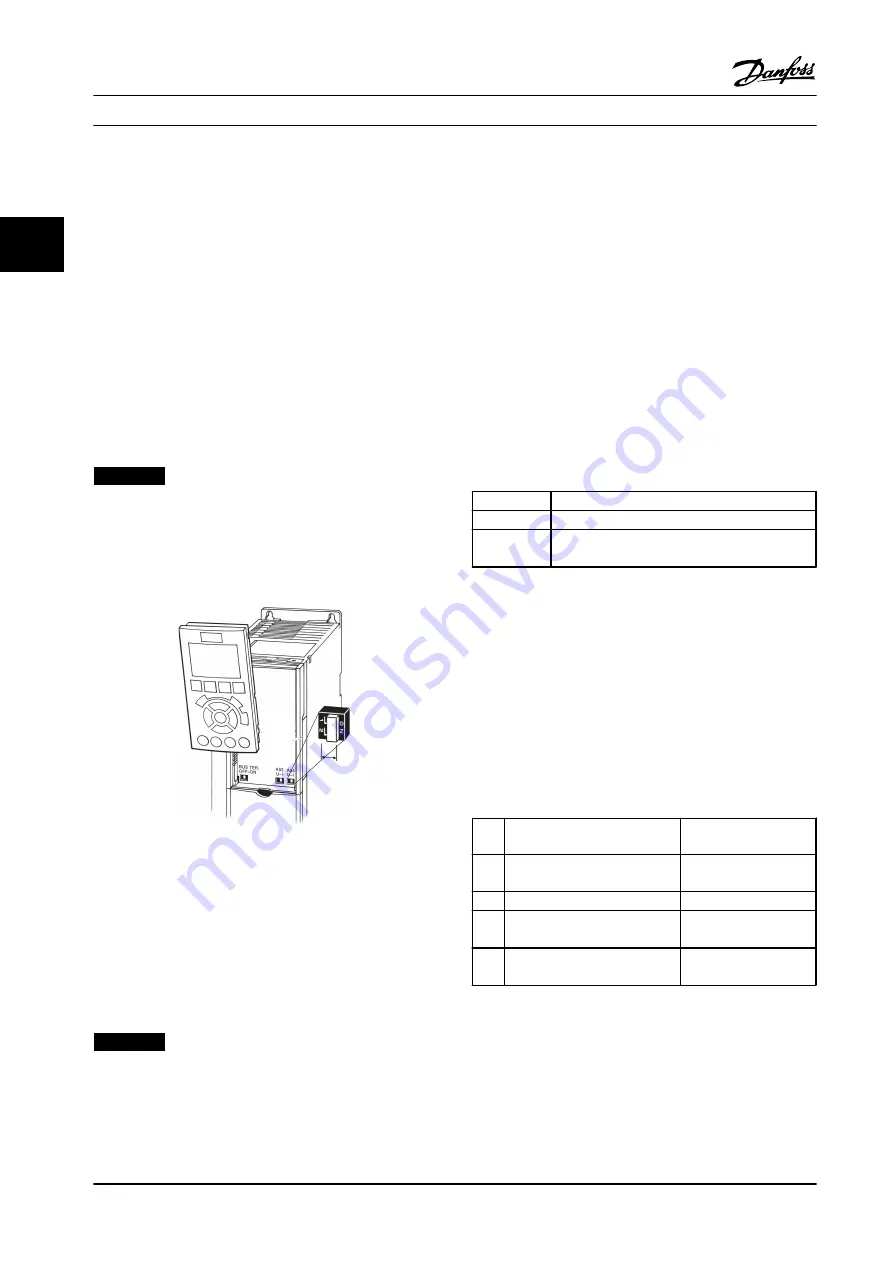
3.4.22 Switches S201, S202, and S801
Use switches S201 (A53) and S202 (A54) to select a current
(0–20 mA) or a voltage (-10 V to 10 V) configuration of the
analog input terminals 53 and 54 respectively.
Switch S801 (BUS TER.) can be used to enable termination
on the RS-485 port (terminals 68 and 69).
See
Default setting:
S201 (A53) = OFF (voltage input)
S202 (A54) = OFF (voltage input)
S801 (Bus termination) = OFF
NOTICE!
When changing the function of S201, S202 or S801 do
not use force for the switch over. Remove the LCP cradle
when operating the switches. The switches must not be
operated while the adjustable frequency drive is
powered.
130B
T310.11
Figure 3.30 Remove the LCP Cradle to Access Switches
3.4.23 Serial Communication
RS-485 is a 2-wire bus interface compatible with multi-drop
network topology, i.e., nodes can be connected as a bus,
or via drop cables from a common trunk line. A total of 32
nodes can be connected to one network segment.
Repeaters divide network
NOTICE!
Each repeater functions as a node within the segment in
which it is installed. Each node connected within a given
network must have a unique node address across all
segments.
Terminate each segment at both ends using either the
termination switch (S801) of the adjustable frequency
drives or a biased termination resistor network. Always use
shielded twisted pair (STP) cable for bus cabling, and
always follow good common installation practice.
Low-impedance ground connection of the shield at every
node is important, including at high frequencies. Thus,
connect a large surface of the shield to ground, for
example, with a cable clamp or a conductive cable
connector. It may be necessary to apply potential-
equalizing cables to maintain the same ground potential
throughout the network - particularly in installations with
long cables.
To prevent impedance mismatch, always use the same
type of cable throughout the entire network. When
connecting a motor to the adjustable frequency drives,
always use shielded motor cable.
Cable
Shielded twisted pair (STP)
Impedance
120
Ω
Cable length
Max. 4000 ft [1200 m] (including drop lines)
Max. 1,650 ft [500 m] station-to-station
Table 3.13 Cable Recommendations
3.5 Final Set-up and Test
Before operating the adjustable frequency drive, perform a
final test of the installation:
1.
Locate the motor nameplate to find out whether
the motor is star (Y) or delta connected (
Δ)
.
2.
Enter the motor nameplate data in the parameter
list. Access the list by pressing the [Quick Menu]
key and selecting Q2 Quick Set-up. See
.
1.
Motor Power [kW]
or Motor Power [HP]
1-20 Motor Power [kW]
1-21 Motor Power [HP]
2.
Motor Voltage
3.
Motor Frequency
1-23 Motor Frequency
4.
Motor Current
5.
Motor Nominal Speed
parameter 1-25 Motor
Nominal Speed
Table 3.14 Quick Set-up Parameters
Installation
Instruction Manual
36
Danfoss A/S © Rev. 2014-02-07 All rights reserved.
MG37A222
3
3
Summary of Contents for VLT AutomationDrive FC 302
Page 2: ......