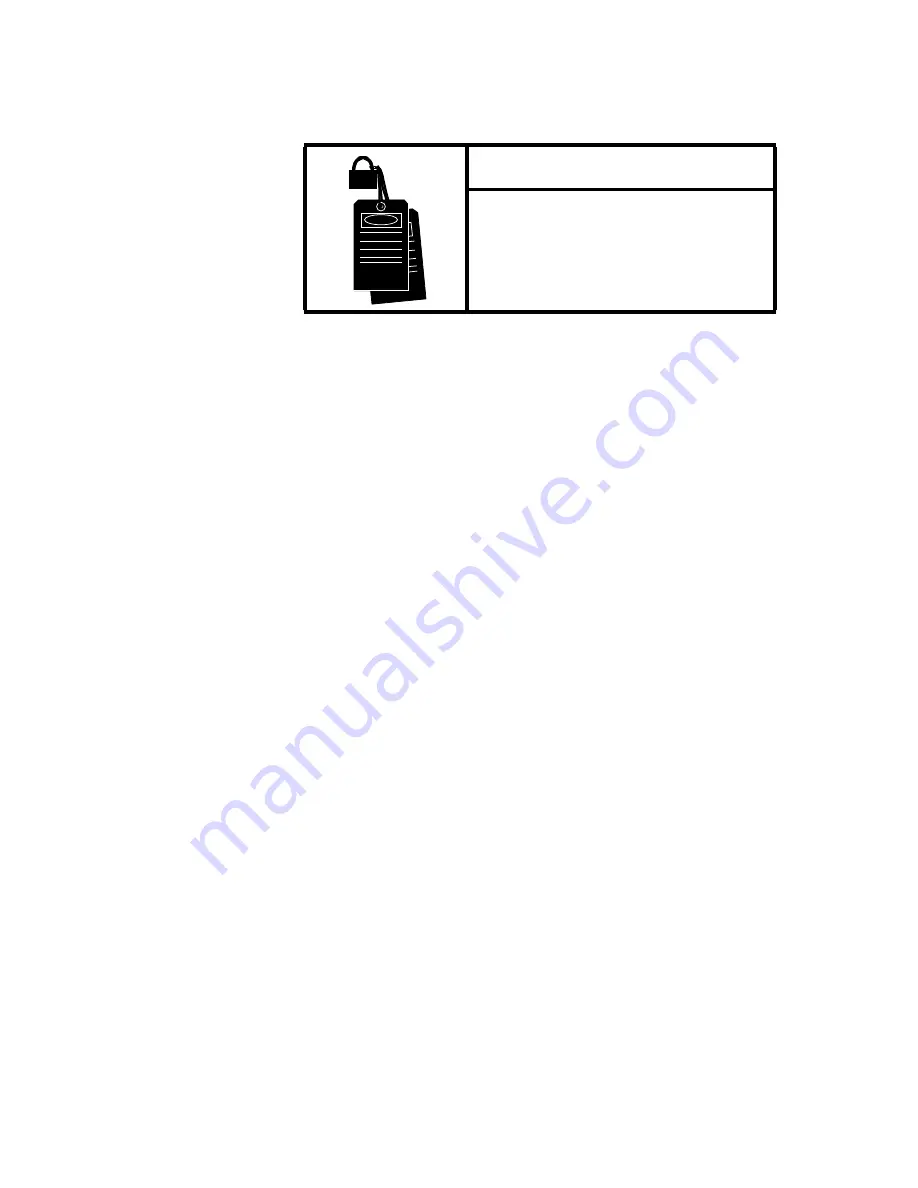
FRP 10: Logic Cable Replacement
AC Repair and Adjustment Procedures
66
Cray Research/Silicon Graphics Proprietary
HMM-168-A
You may also open, lock, and tag the customer’s wall breaker(s).
3.
Open the rear cabinet door.
4.
Loosen the eight 1/4-turn captive screws that secure the module panel,
then pull the module panel out of the cabinet at an angle.
To access a cable in the Z-side (top) wiremat, skip
and
and
. To access a cable in the Y-side (bottom) wiremat, complete
and
.
5.
To access a cable in the Y-side (bottom) wiremat: Remove the I/O panel.
Eight 1/4-turn captive screws secure the I/O panel to the cabinet.
6.
To access a cable in the Y-side (bottom) wiremat: Remove the lower
plenum panel
.
Twelve #1 Phillips screws hold the lower plenum in place;
four of the screws pass through the top of the I/O bulkhead.
7.
To access a cable in the Z-side (top) wiremat: Use a small flatblade
screwdriver to disconnect the clock cable from the clock switch board.
8.
To access a cable in the Z-side (top) wiremat: Use a #2 Phillips
screwdriver to remove the blower exhaust shield.
NOTE:
If the torus interconnections (of the cable that you are removing) are
in a different cabinet than the rail connection, you must access the
wiremats in both cabinets. In addition, you must open the
intercabinet cable ducts as described in the following step.
9.
If the cable that you are removing passes from one cabinet to another,
open the cable ducts where the cable passes between cabinets:
a. Use a #1 Phillips screwdriver to loosen the five Phillips screws that
secure each air seal assembly on the cable ducts.
WARNING
Ensure that the electrical plug for the
equipment that you service is
unplugged, locked, and tagged. Failure
to do so could result in severe shock
and burns.