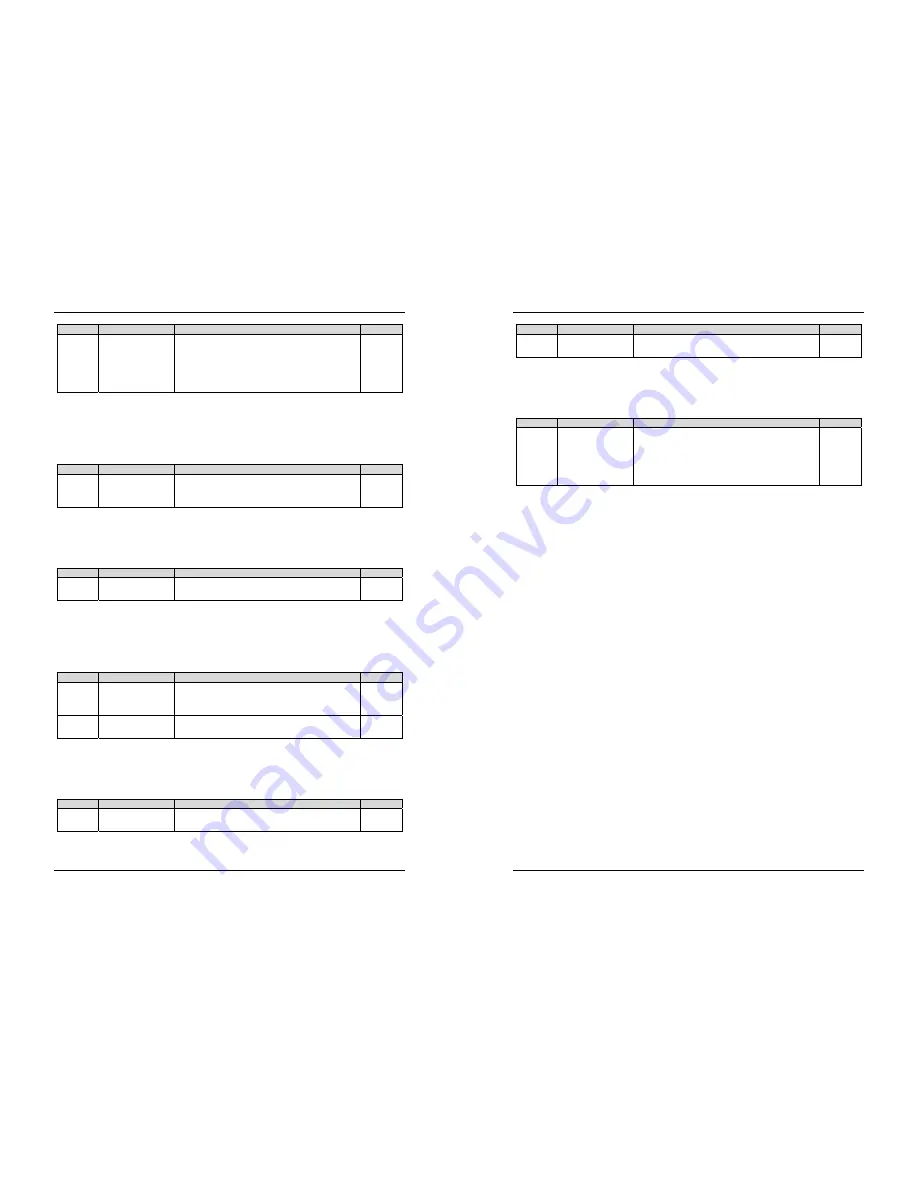
EM11 User’s Manual
5. Description of Function Codes
103
Code
Parameter Name
Setting Range
Default
d0-20
Encoder type
0: ABZ incremental encoder
1: Resolver
2: UVW incremental encoder
3: Reserved
4: Wire-saving UVW encoder
0
The EM11 supports multiple types of encoder. Different PG cards are required for different types of
encoder. Select the appropriate PG card for the encoder used. Any of the five encoder types is applicable to
synchronous motor. Only ABZ incremental encoder and resolver are applicable to asynchronous motor.
After installation of the PG card is complete, set this parameter properly based on the actual condition.
Otherwise, the frequency inverter cannot run properly.
Code
Parameter Name
Setting Range
Default
d0-21
A/B phase sequence
of ABZ incremental
encoder
0: Forward
1: Reserve
0
This parameter is valid only for ABZ incremental encoder (d0-20 = 0) and is used to set the A/B phase
sequence of the ABZ incremental encoder.
It is valid for both asynchronous motor and synchronous motor. The A/B phase sequence can be obtained
through "Asynchronous motor complete auto-tuning" or "Synchronous motor no-load auto-tuning".
Code
Parameter Name
Setting Range
Default
d0-22
Encoder installation
angle
0.0°~359.9° 0.0°
This parameter is applicable only to synchronous motor. It is valid for ABZ incremental encoder, UVW
incremental encoder, resolver and wire-saving UVW encoder, but invalid for SIN/COS encoder.
It can be obtained through synchronous motor no-load auto-turning or with-load auto-tuning. After
installation of the synchronous motor is complete, the value of this parameter must be obtained by motor
auto-tuning. Otherwise, the motor cannot run properly.
Code
Parameter Name
Setting Range
Default
d0-23
U, V, W phase
sequence of UVW
encoder
0: Forward
1: Reverse
0
d0-24
UVW encoder angle
offset
0.0°~359.9° 0.0°
These two parameters are valid only when the UVW encoder is applied to a synchronous motor. They can
be obtained by synchronous motor no-load auto-tuning or with-load auto-tuning. After installation of the
synchronous motor is complete, the values of these two parameters must be obtained by motor auto-tuning.
Otherwise, the motor cannot run properly.
Code
Parameter Name
Setting Range
Default
d0-28
Number of pole pairs
of resolver
1~99 1
If a resolver is applied, set the number of pole pairs properly.
5. Description of Function Codes
EM11 User’s Manual
104
Code
Parameter Name
Setting Range
Default
d0-29
Encoder wire-break
fault detection time
0.0s: No action
0.1s~10.0s
0.0s
This parameter is used to set the detecting time that a wire-break faults. If it is set to 0.0s, the frequency
inverter does not detect the encoder wire-break fault. If the duration time of the encoder wire-break fault
detected by the frequency inverter exceeds the time set in this parameter, the frequency inverter reports
Err20.
Code
Parameter Name
Setting Range
Default
d0-30
Motor 1 auto-tuning
selection
0: No auto-tuning
1: Asynchronous motor static auto-tuning
2: Asynchronous motor complete auto-tuning
11: Synchronous motor with-load auto-tuning
12: Synchronous motor no-load auto-tuning
0
0: No auto-tuning
Auto-tuning is prohibited.
1: Asynchronous motor static auto-tuning
It is applicable to scenarios where complete auto-tuning cannot be performed because the asynchronous
motor cannot be disconnected from the load.
Before performing static auto-tuning, properly set the motor type and motor nameplate parameters of d0-00
~ d0-04 firstly. The frequency inverter will obtain parameters of d0-05 ~ d0-07 by static auto-tuning.
Action guide: Set this parameter to 1, and press
RUN
key. Then, the frequency inverter starts static
auto-tuning.
2: Asynchronous motor complete auto-tuning
To perform this type of auto-tuning, ensure that the motor is disconnected from the load. During the process
of complete auto-tuning, the frequency inverter performs static auto-tuning first and then accelerates to 80%
of the rated motor frequency within the acceleration time set in b0-21. The frequency inverter keeps
running for a certain period and then decelerates to stop with deceleration time set in b0-22.
Before performing complete auto-tuning, properly set the motor type, motor nameplate parameters of b0-00
and d0-00~ d0-04, "Encoder type" (d0-20) and "Encoder pulses per revolution" (d0-19) first.
The frequency inverter will obtain motor parameters of d0-05 ~ d0-09, "A/B phase sequence of ABZ
incremental encoder" (d0-21) and vector control current loop PI parameters of d1-10 ~ d1-13 by complete
auto-tuning.
Action guide: Set this parameter to 2, and press
RUN
key. Then, the frequency inverter starts complete
auto- tuning.
11: Synchronous motor with-load auto-tuning
It is applicable to site where the synchronous motor cannot be disconnected from the load. During
with-load auto-tuning, the motor rotates at the speed of 10 RPM.
Before performing with-load auto-tuning, properly set the motor type and motor nameplate parameters of
b0-00 and d0-00 ~ d0-04 first.
By with-load auto-tuning, the frequency inverter obtains the initial position angle of the synchronous motor,
which is a necessary prerequisite of the motor's normal running. Before the first use of the synchronous
motor after installation, motor auto-tuning must be performed.
Action guide: Set this parameter to 11, and press
RUN
key. Then, the frequency inverter starts with-load
auto-tuning.