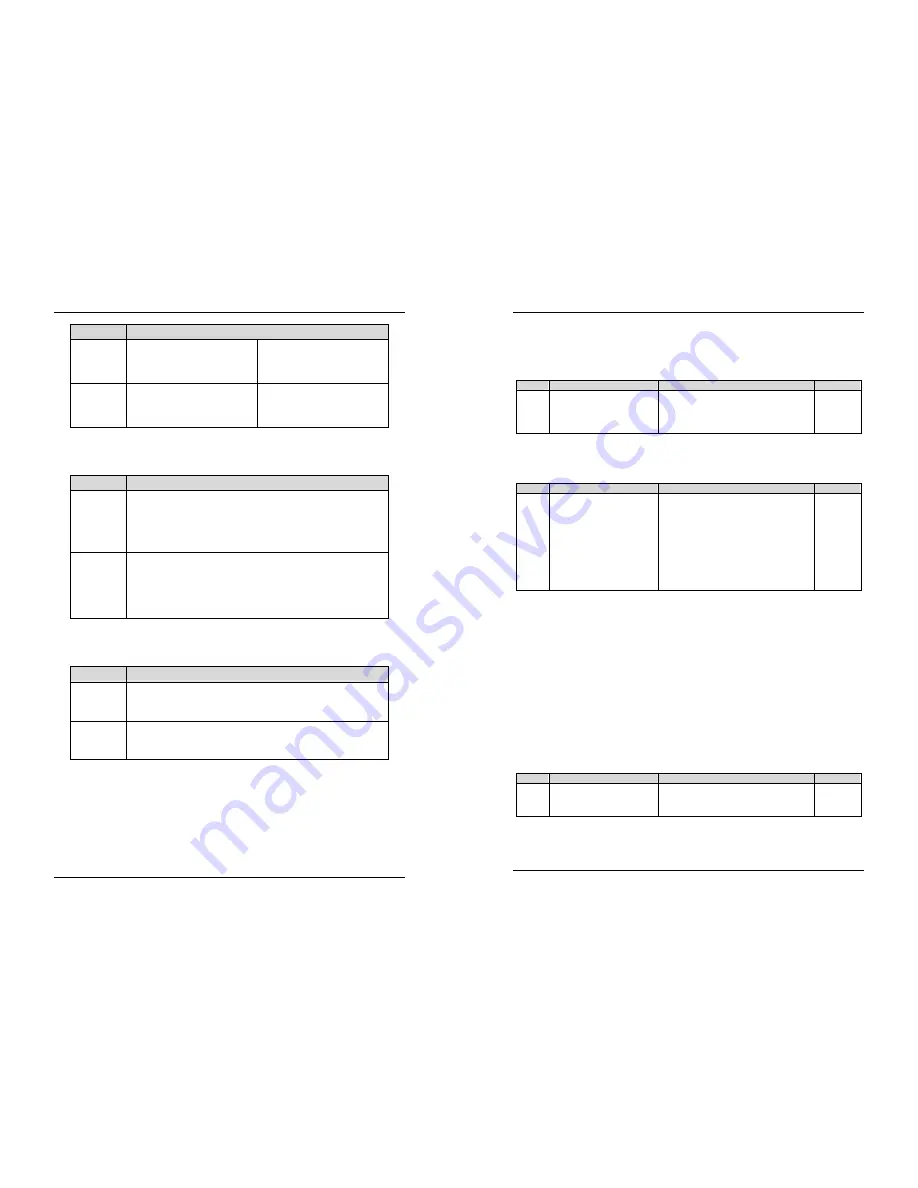
EM11 User’s Manual
4. Operation and display
37
Motor
Parameter
Motor 1
b0-00
:
Motor Type Selection
d0-01
:
Motor Rated Voltage
d0-03
:
Motor Rated Frequency
d0-00
:
Motor Rated Power
d0-02
:
Motor Rated Current
d0-04
:
Motor Rated Speed
Motor 2
b0-00
:
Motor Type Selection
d2-01
:
Motor Rated Voltage
d2-03
:
Motor Rated Frequency
d2-00
:
Motor Rated Power
d2-02
:
Motor Rated Current
d2-04
:
Motor Rated Speed
AC asynchronous motor tuning
If the motor can be disconnected from the load, then please set d0-30/d2-30 to 2(asynchronous motor
complete auto-tuning), then press the RUN key on the keypad. The frequency inverter will automatically
calculate the following parameters of motor:
Motor
Parameter
Motor 1
d0-05
:
Stator resistance (asynchronous motor)
d0-06
:
Rotor resistance (asynchronous motor)
d0-07
:
Leakage inductive reactance(asynchronous motor)
d0-08
:
Mutual inductive reactance(asynchronous motor)
d0-09
:
No-load current(asynchronous motor)
Motor 2
d2-05
:
Stator resistance (asynchronous motor)
d2-06
:
Rotor resistance (asynchronous motor)
d2-07
:
Leakage inductive reactance(asynchronous motor)
d2-08
:
Mutual inductive reactance(asynchronous motor)
d2-09
:
No-load current(asynchronous motor)
Finish motor parameter auto-tuning.
If the motor cannot be fully disconnected with the load, then please select d0-30/d2-30 as 1 (asynchronous
static auto-tuning), and press the RUN key in the keypad panel.
And the frequency inverter will automatically calculate the following parameters of motor:
Motor
Parameter
Motor 1
d0-05
:
Stator resistance (asynchronous motor)
d0-06
:
Rotor resistance (asynchronous motor)
d0-07
:
Leakage inductive reactance(asynchronous motor)
Motor 2
d2-05
:
Stator resistance (asynchronous motor)
d2-06
:
Rotor resistance (asynchronous motor)
d2-07
:
Leakage inductive reactance(asynchronous motor)
Description of synchronous motor identification:
As the EM11 driven synchronous machine system needs the feedback signal from encoder, so uses need to
correctly set the parameter of encoder before identification.
During the identification process of synchronous system, rotation movement is needed. The best
identification method is no-load dynamic running identification, if the condition is not allowed; with-load
dynamic identification is workable.
5. Description of Function Codes
EM11 User’s Manual
38
5. Description of Function Codes
5.1 Group b0: Basic Function Parameters
Code
Parameter Name
Setting Range
Default
b0-00
Motor type selection
Unit’s digit: Motor 1 selection
Ten’s digit: Motor 2 selection
0: AC asynchronous motor
1: Permanent magnetic synchronous motor
0
Unit’s digit: 0- select Motor 1 as AC asynchronous motor;
1-select Motor 1 as Permanent magnetic synchronous motor
Ten’s digit: 0-select Motor 2 as AC asynchronous motor;
1-select Motor 2 as Permanent magnetic synchronous motor
Code
Parameter Name
Setting Range
Default
b0-01
Motor control mode
Unit's digit: Motor 1 control mode selection.
Ten's digit: Motor 2 control mode selection.
0: Sensor-less vector control (SVC)
1: Closed-loop vector control (VC)
2:V/F control
Hundred’s digit/Thousand’s digit: reserved
Ten thousand’s digit: Motor selection
0: Motor 1
1: Motor 2
0
Unit’s digit and Ten’s digit is to select motor 1 and motor 2 control mode.
0: Sensor less vector control (SVC)
It indicates open-loop vector control, and is applicable to high-performance control applications such as
machine tool, centrifuge, wire drawing machine and injection molding machine. One frequency inverter can
operate only one motor.
1: Closed-loop vector control (VC)
It is applicable to high-accuracy speed control or torque control applications such as high-speed paper
making machine, crane and elevator. One Frequency inverter can operate only one motor. An encoder must
be installed at the motor side, and a PG card matching the encoder must be installed at the frequency
inverter side.
2: Voltage/Frequency (V/F) control
It is applicable to applications with low requirements or applications where one frequency inverter operates
multiple motors, such as fan and pump.
Note:
If vector control is used, motor auto-tuning must be performed because the advantages of vector
control can only be utilized after correct motor parameters are obtained. Better performance can be achieved
by adjusting speed regulator parameters in group “d”.
For the permanent magnetic synchronous motor (PMSM), the EM11 does not support SVC. VC is used
generally. In some low requirements applications, you can also use V/F.
Code
Parameter Name
Setting Range
Default
b0-02 Command
source
selection
0: Keypad control (LED off)
1: Terminal control (LED on)
2: Communication control (LED blinking)
0
It is used to determine the input channel of the frequency inverter control commands, such as run, stop,
forward rotation, reverse rotation and jog operation. You can input the commands in the following three
channels:
0: Keypad control
("LOCAL/REMOT" indicator off)