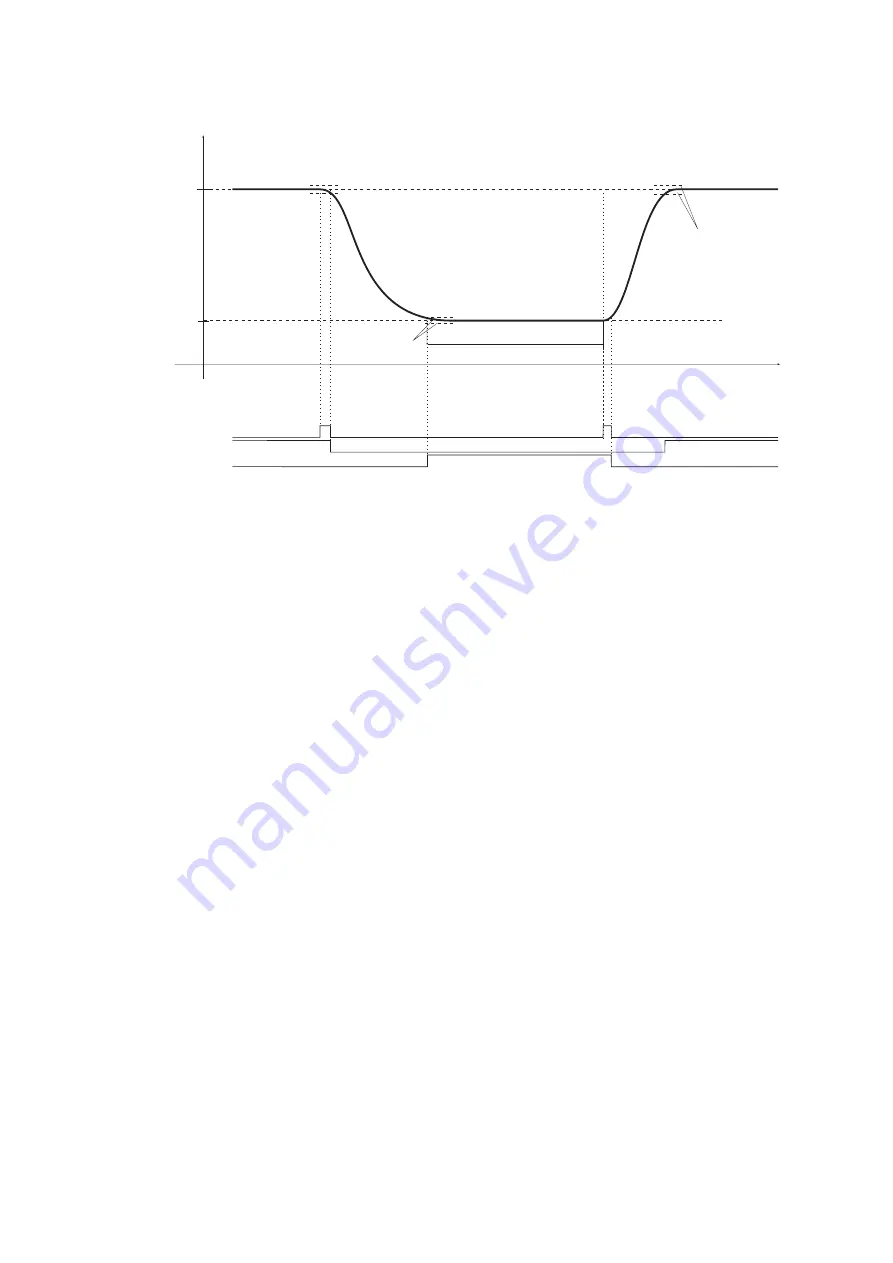
92/132 Operation
Bosch Rexroth AG
, SYEPS series 1X, RE 30201-B/07.2014
X
t
POP
PUP
OUT 2
OUT 3
IN 2
Start stroke
Position POP reached
Position PUP reached
Positioning window PUP
Forming time
Positioning window
POP
Start stroke
Forming time
R421
NRG
R423
R425
Fig. 67: Mode 44 – forming with stop in PUP using 2 start signals and associated I/O signals
9.2.9 Failsafe operation
Failsafe operation serves to move the axis in closed-loop control and at constant
velocity to the failsafe position when the machine is switched off or in the event of a
fault. In most of the cases, the failsafe position corresponds to the upper positive
stop of the cylinder.
Failsafe operation is activated by withdrawing the enable input IN1 of the HNC100.
The axis moves to the failsafe position set in R parameter 443. The velocity at which
the axis moves to the failsafe position is set in R parameter 442 “failsafe ramp“.
With somewhat greater effort, this operating mode can also be used in the event
of a voltage failure in order to move the axis smoothly to the upper positive
stop. To maintain the closed-loop-controlled movement of the axis, the voltage
supply of both, the high-response valve and the HNC100, must be buffered with a
(rechargeable) battery or capacitor so that the axis can move to its failsafe position.
The buffer capacity of the voltage buffer depends on the time that the axis takes at
maximum to reach its failsafe position. This time can only be determined by trial and
testing during initial commissioning of the machine. Failsafe operation is started
automatically in the event of a voltage failure, when all of the PLC outputs dropped
out and the IN1 on the HNC100 is consequently at Low level.
The axis moves at the preset velocity of 300 mm/s to the upper mechanical stop.
Advanced/High
Standard