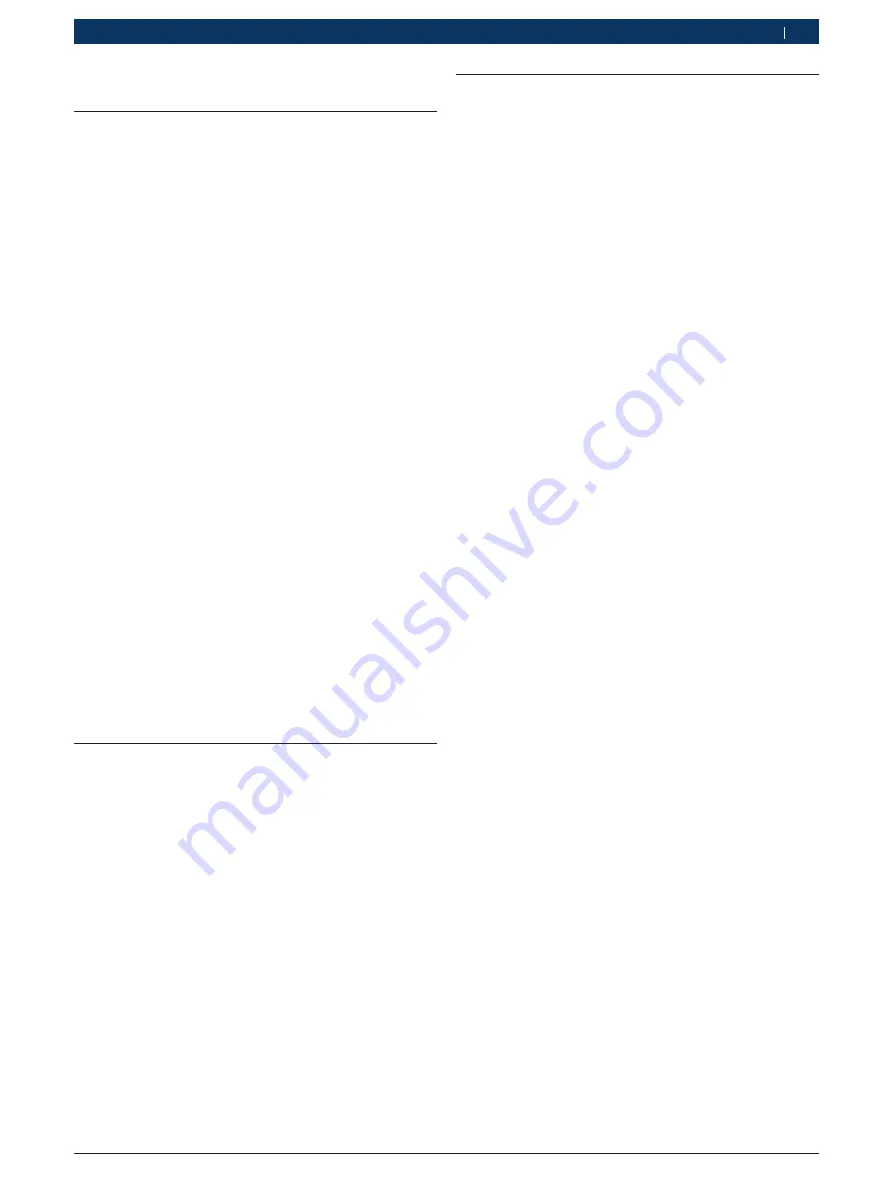
1 689 989 000
2013-05-02
|
Robert Bosch GmbH
Operation | EPS 200 | 39
en
5. Operation
5.1
Turning on/off
¶
Switch on EPS 200 using the master switch on the
front of the unit (see Fig. 1, Pos. 7).
After switching on, the Windows operating system
starts first, followed by the EPS 200 system soft-
ware.
¶
Before switching off
using the master switch, first
close the EPS 200 system software and then shut
down the Windows operating system.
i
Prior to renewed switch-on, the PC must have been
switched off for at least 60 seconds.
i
Always switch off the EPS 200 by way of the central
master switch on the front of the unit before
unplugging the three-phase AC connector from the
three-phase AC system.
i
When operating the EPS 200, errors can occur
if peripheral devices (e.g. printer, DVD drive,
connecting leads) are used that have
not
been
supplied by Bosch.
5.1.1
Touchscreen with stylus
The touchscreen on the EPS 200 is operated using the
stylus. The stylus essentially has the same functions as
a mouse (see Online Help).
5.1.2
On-screen keyboard
The EPS 200 system software provides an on-screen
keyboard that is operated using the stylus (see Online
Help). Pressing <
F2
> displays the on-screen keyboard in
the current window.
5.2
Preparations for testing
R
Before every CRI/CRIN and DHK/UI test sequence,
use the oil level display (Fig 1, 9) that there is
sufficient test oil in the tank.
!
The test oil level must always be on or just below the
upper inspection port mark.
R
We recommend performing a daily leak test (sealing
plug with connection adapter, see section 3.5.13).
The leak test is called up under “
Service >> Unit
diagnosis
”.
R
To prevent contamination of the test oil, every
CRI/CRIN and DHK/UI component must be cleaned
before the test. Never fit damaged, contaminated
and/or severely corroded CRI/CRIN and DHK/UI for
testing.
5.3
Cleaning instructions for CRI/CRIN
and DHK/UI
!
Do
not
clean the nozzle cone with a brass brush,
steel brush or the like as this would damage the
injection orifices. Do
not
clean injection orifices with
the nozzle cleaning tool 0 986 611 140. Do
not
clean
the electrical connection of the injector with cold
cleaning agent.
1.
Seal the inlet connection, return connection and
nozzle cone of the injector/nozzle holder with pro-
tective caps or cover over.
2.
Use a plastic brush to remove any coarse dirt on the
injector/nozzle holder.
3.
Pre-clean the injector/nozzle holder with cold clean-
ing agent.
!
Use the cleaning agent Tickopur TR 13 or a compa-
rable corrosion and coke-dissolving cleaning agent
for ultrasonic cleaning.
4.
Remove the protective cap from the nozzle cone.
5.
Attach the injector/nozzle holder to a suitable holder
and immerse it in the ultrasonic bath until the nozzle
retaining nut is completely covered by the cleaning
agent.
6.
Set a cleaning temperature of 140 °F to 158 °F (60 °C
to 70 °C).
7.
After approx. 15 minutes, take the injector/nozzle
holder out of the ultrasonic bath and blow dry with
compressed air.
i
After cleaning, always store injectors/nozzle holders
in a clean, closed container to prevent the injectors/
nozzle holders coming into contact with dirt par-
ticles (e. g. fluff, swarf).
i
Also heed the additional cleaning information in the
ESI[tronic] component repair instructions.