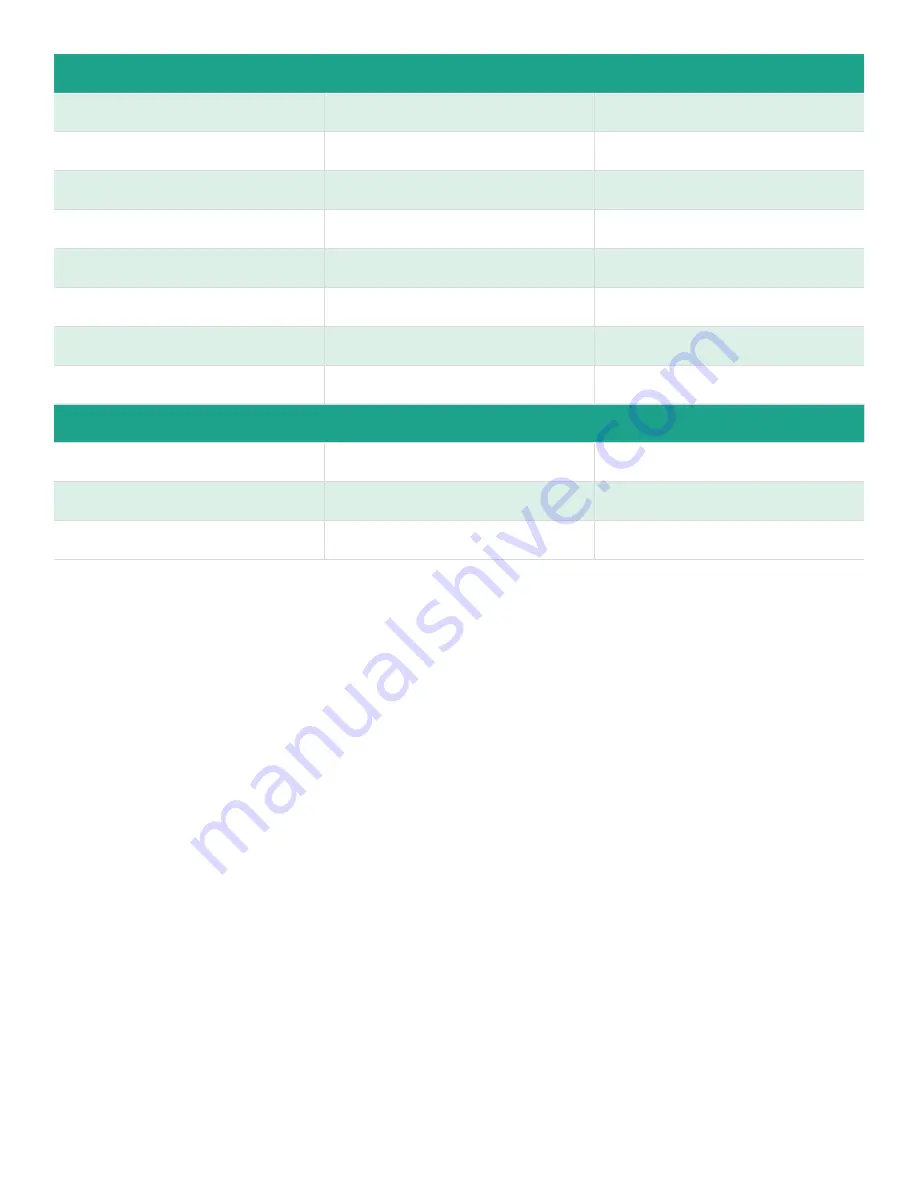
Table 34: Measurements available over HART
Ch 1 Gain Up
Ch 2 ActiveTw SNR Up
Ch 3 ActiveTw Gain Down
Ch 1 Gain Down
Ch 2 ActiveTw SNR Down
Ch 3 Error Status
Ch 1 SNR Up
Ch 2 ActiveTw Amplitude Up
Ch 3 Reported Error
Ch 1 SNR Down
Ch 2 ActiveTw Amplitude Down
Ch 3 Peak Index Up
Ch 1 ActiveTw Up
Ch 2 ActiveTw Gain Up
Ch 3 Peak Index Down
Ch 1 ActiveTw SNR Up
Ch 2 ActiveTw Gain Down
Ch 3 Peak % Up
Ch 1 ActiveTw SNR Down
Ch 2 Error Status
Ch 3 Peak % Down
Ch 1 ActiveTw Amplitude Up
Ch 2 Reported Error
Ch 3 No. Of Errors
Meter Information
Flow board Serial number
Sensor 1 Dn Serial number
Sensor 3 Up Serial number
Flow board hardware revision
Sensor 2 Up Serial number
Sensor 3 Dn Serial number
Sensor 1 Up Serial number
Sensor 2 Dn Serial number
99
Summary of Contents for Panametrics PanaFlow LC
Page 1: ...PanaFlow LC User s manual 910 327 Rev A...
Page 2: ...ii...
Page 3: ...PanaFlow LC Panametrics liquid ultrasonic flowmeter User s manual 910 327 Rev A Sep 2019 iii...
Page 4: ...no content intended for this page iv...
Page 12: ...no content intended for this page xii...
Page 44: ...Figure 58 Setting up pulse output 32...
Page 49: ...Figure 60 Setting up alarm output 37...
Page 80: ...no content intended for this page 68...
Page 82: ...no content intended for this page 70...
Page 86: ...no content intended for this page 74...
Page 98: ...Table 30 Service Record Date Description of Service Performed By 86...
Page 104: ...no content intended for this page 92...
Page 106: ...no content intended for this page 94...
Page 114: ...no content intended for this page 102...
Page 138: ...no content intended for this page 126...
Page 140: ...no content intended for this page 128...