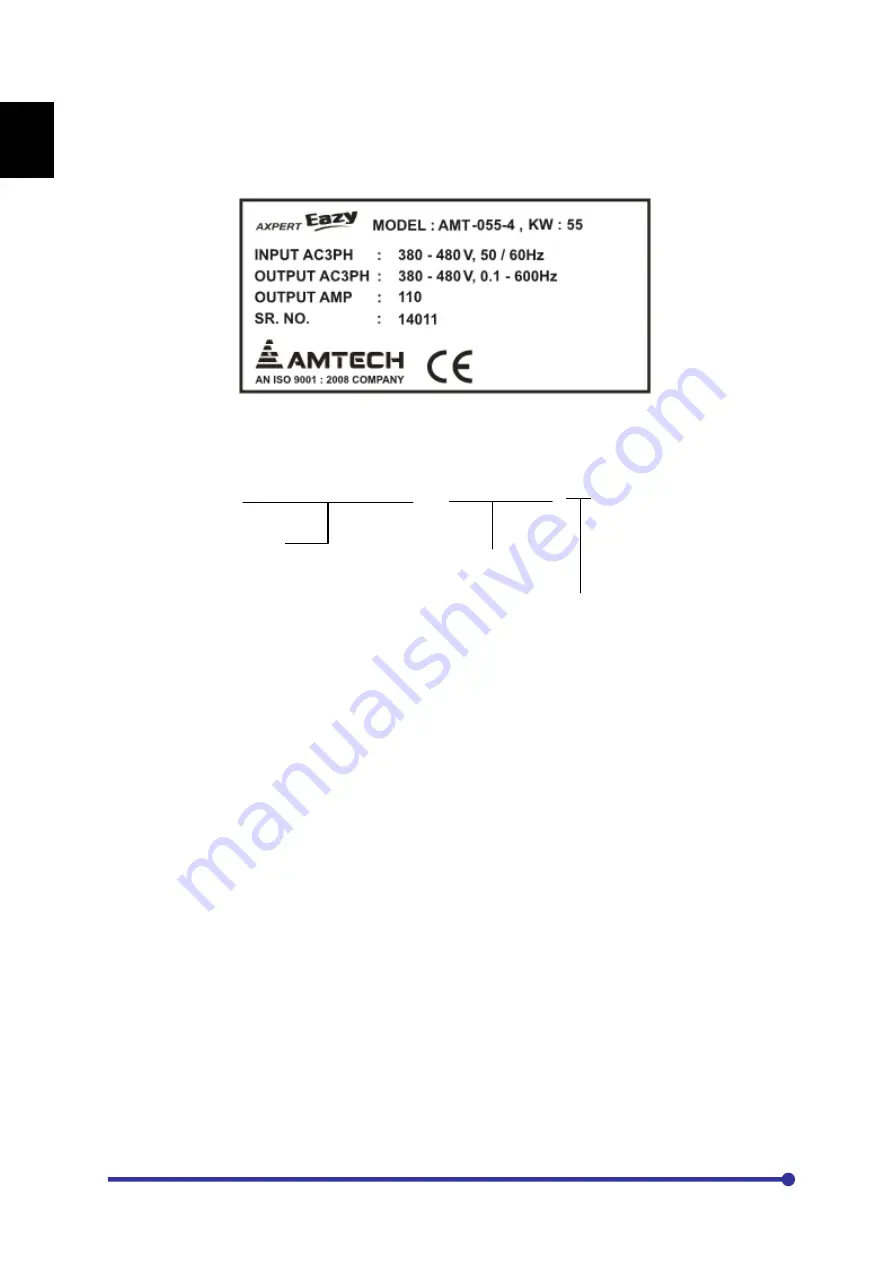
Amtech
1.2
1
1-2 Details of rating nameplate and type display method
The following details are listed on the rating nameplate.
Using the above type as an example, the type is displayed as follows:
AXPERT- EAZY
AMT - 055 - 4
Series name
Capacity 55kW
4: 380 ~ 480VAC, 3-phase, 50/60Hz
5: 500 ~ 575VAC, 3-phase, 50/60Hz
6: 600 ~ 690VAC, 3-phase, 50/60Hz
2: 200 ~ 240VAC, 3-phase, 50/60Hz
Summary of Contents for Axpert-Eazy AMT-011-4
Page 2: ...Amtech ii...
Page 19: ...Axpert Eazy AC Variable Frequency Drive 2 11 2 400V Series AMT 200 4 AMT 250 4...
Page 22: ...Amtech 2 14 2 This Page is intentionally left blank...
Page 37: ...Axpert Eazy AC Variable Frequency Drive 4 9 4...
Page 38: ...Amtech 4 10 4 This page is intentionally left blank...
Page 46: ...Amtech 5 8 5 This page is intentionally left blank...
Page 216: ...Amtech 13 6 13 This page is intentionally left blank...
Page 221: ...Axpert Eazy AC Variable Frequency Drive A 5 13 A Outline Dimensions...
Page 239: ...Notes...
Page 240: ...Notes...
Page 241: ......
Page 242: ...AMTECH...