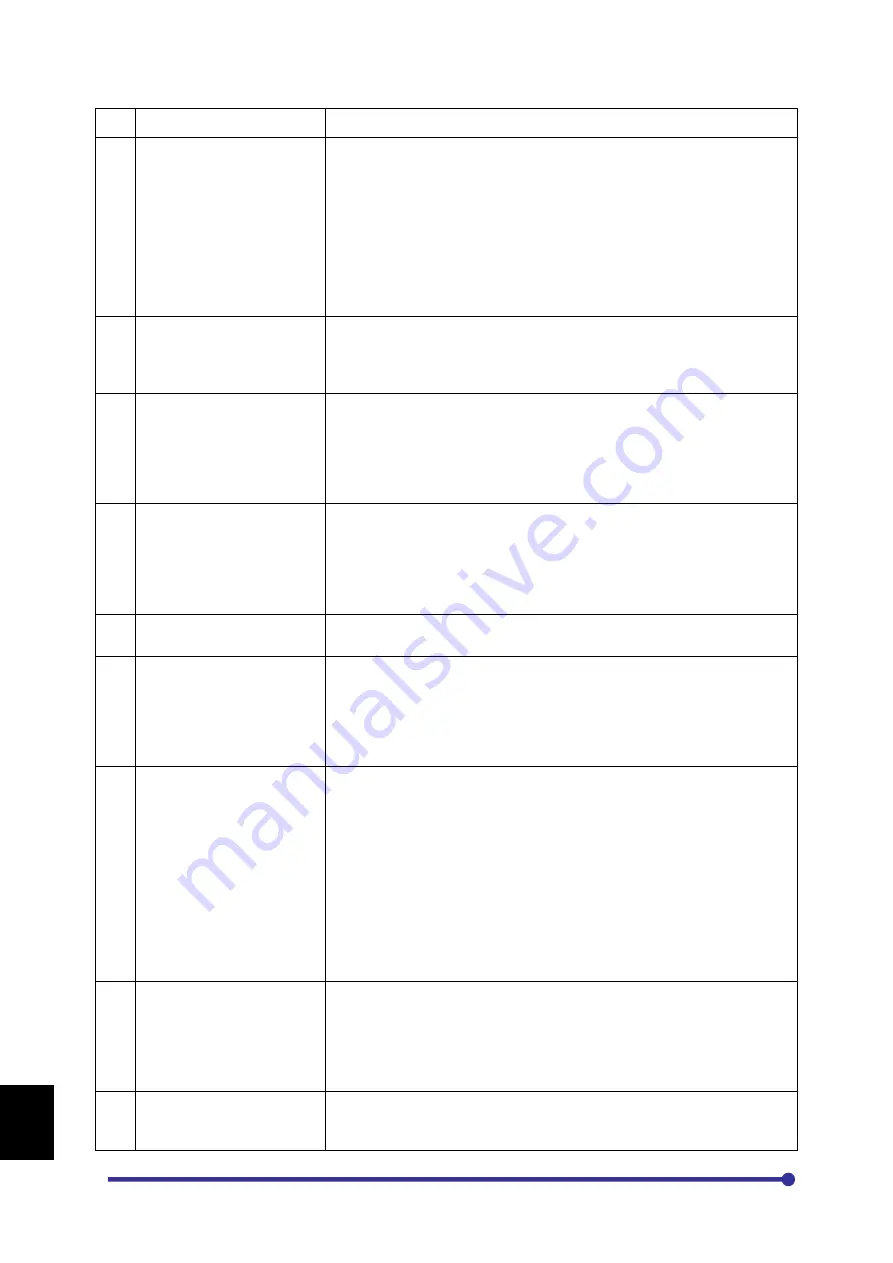
Amtech
A.14
13
A
No.
Fault Name
Causes & Countermeasures
Adjust B111 to prevent the hunting of motor.
3. If the fault is coming during deceleration, the load GD
2
may be too
large. Set the ramp down time according to the load GD
2
.
4. Loose connection of dc bus voltage feedback at J9 of PCA-2014A.
Ensure proper connections.
5. Check the value of snubber capacitors mounted on the IGBT and
replace if found abnormal.
6. Check the output line or motor. Check that any output is not
shorted with the ground. Partially damaged output cables can also
lead to this condition.
7
Under Voltage Fault
1. DC Bus voltage may have fallen below the under voltage level. A
drop in voltage, phase dropout or power supply failure may have
occurred. Check the input power supply and correct it if necessary.
2. Check soft charge contactor or connection.
8
Charging Fault
1. The dc bus voltage didn’t reach to predefined voltage level within 5
seconds after power up.
Soft charge resistor may be open.
One or more phases may have failed.
Dc bus voltage feedback may be missing. Ensure proper
connection of dc bus voltage feedback at J9.
9
Output Phase Loss
1. There may be a single phasing of the motor.
Disconnect and check the motor.
2. One or more output cables are open or loose connected.
Check the output connections and correct it.
3. There may be problem in current sensors.
4. Disable the feature using
C307.
10
Reference Missing
1. Analog current input reference (4-20 mA) to the unit is below 3 mA.
Check the voltage level at FSI terminal of PCA-2014A.
11
External Fault
1. The signal for the external fault is present at the PSI.
Check and correct it.
2. If the signal is not present, remove the selection of the external
fault with the help of Mode-C parameters.
3. There may be a problem in PCA-2014A.
Remove the control board PCA-2014A.
12
Thermistor Over
Temperature Fault
1. A trouble may have occurred in the cooling blower.
Replace it if necessary.
2. The ambient temperature may have risen.
Lower the ambient temperature (less than 50 °C for 400 V series or
less than 40 °C for 500 V / 600 V series).
3. The carrier frequency may be set too high.
4. The temperature switch (thermostat) or thermistor is not connected
or loosely connected at J16 and J13 respectively. Disconnect
thermostat switch connection at J16 and ensure that the thermostat
shows short circuit. Disconnect the thermistor and ensure that the
thermistor shows resistance greater than 2.2 k
Ω
but less than 60
k
Ω
. Reconnect thermostat and thermistor properly.
13
Auto Tuning Fault
1. The auto tuning process has failed. The motor parameter setting
value may be incorrect.
Set correct motor parameter.
Ensure that motor is directly connected to the inverter (remove any
additional components if any like output choke etc. when
performing auto tuning).
14
Emergency Stop
1. The signal for the emergency stop input is present at the PSI.
Check and correct it.
2. If the signal is not present, remove the selection for emergency
Summary of Contents for Axpert-Eazy AMT-011-4
Page 2: ...Amtech ii...
Page 19: ...Axpert Eazy AC Variable Frequency Drive 2 11 2 400V Series AMT 200 4 AMT 250 4...
Page 22: ...Amtech 2 14 2 This Page is intentionally left blank...
Page 37: ...Axpert Eazy AC Variable Frequency Drive 4 9 4...
Page 38: ...Amtech 4 10 4 This page is intentionally left blank...
Page 46: ...Amtech 5 8 5 This page is intentionally left blank...
Page 216: ...Amtech 13 6 13 This page is intentionally left blank...
Page 221: ...Axpert Eazy AC Variable Frequency Drive A 5 13 A Outline Dimensions...
Page 239: ...Notes...
Page 240: ...Notes...
Page 241: ......
Page 242: ...AMTECH...