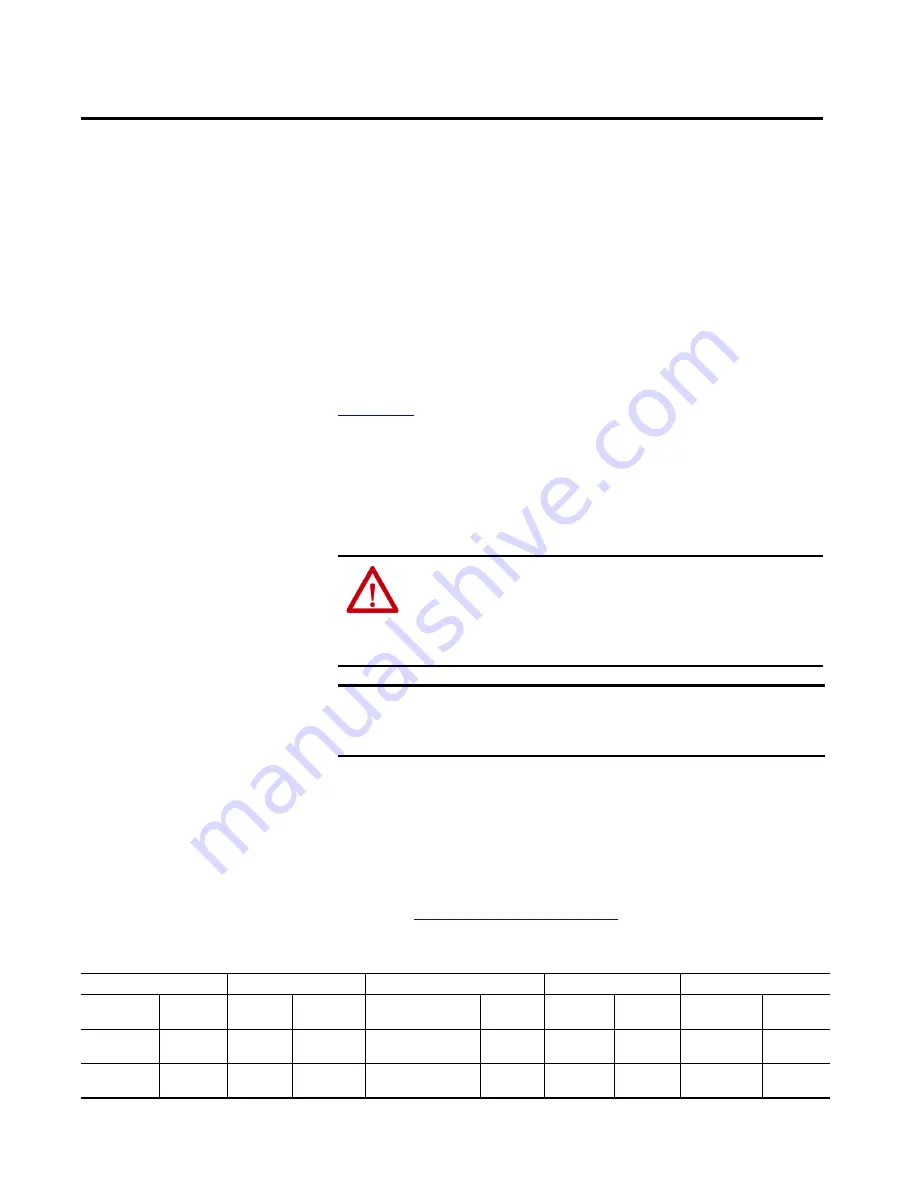
Rockwell Automation Publication 750-UM006C-EN-P - March 2022
49
Chapter
4
Configure and Start Up the Drive
This chapter includes information to establish communication with the drive
via the embedded EtherNet/IP adapter, view adapter status via parameters,
configure the basic startup parameters, and how to set or clear a fault action via
drive parameters. For detailed information on programming, additional
startup information, and troubleshooting of the PowerFlex 755® drive, see the
PowerFlex 750-Series AC Drives Programming Manual, publication
Startup is performed by using the cover-mounted HIM, Connected
Components Workbench™ software, Drive Executive™ software, or the Logix
Designer application. Startup can also be performed by downloading a locally
stored customer template drive file that has the I/O to control the motor brake
configured.
For questions regarding this requirement contact Rockwell Automation Drives
technical support for assistance.
Prepare for Initial Drive
Startup
Gather the following information before proceeding to startup. We
recommend that you print this page and keep it available during the startup
process. See
Startup Information on page 207
in Appendix B of this document
for a printable version of this table. This information is used throughout
startup and while in the startup dialog boxes.
ATTENTION:
Allen Bradley® servo motors must be uncoupled from the load
and have a rotate autotune preformed at startup to identify the
commutation offset required to produce torque properly. This test cannot be
performed with the motor coupled to the load. Failure to comply will result
in equipment damage or failure.
IMPORTANT
For induction motors that can't be easily uncoupled, an alternative static
tune procedure can be used in the autotune portion of startup. However, an
uncoupled rotate tune is the recommended method for commissioning.
Motor Data
(1)
(2)
Dynamic Brake Data
Option Module: Safety
Stop Mode
Application Specifics
Hp/kW
Ohms
(A) S3 Safe Torque Off –
Hardwired
Coast
Accel Rate
Hertz
Watts
(A) S3 Safe Torque Off –
Integrated Safety
Ramp Stop
Decel Rate
RPM
Watts/sec
(joules)
(B) S4 Integrated Safe
Speed Monitoring
Current Limit
S Curve