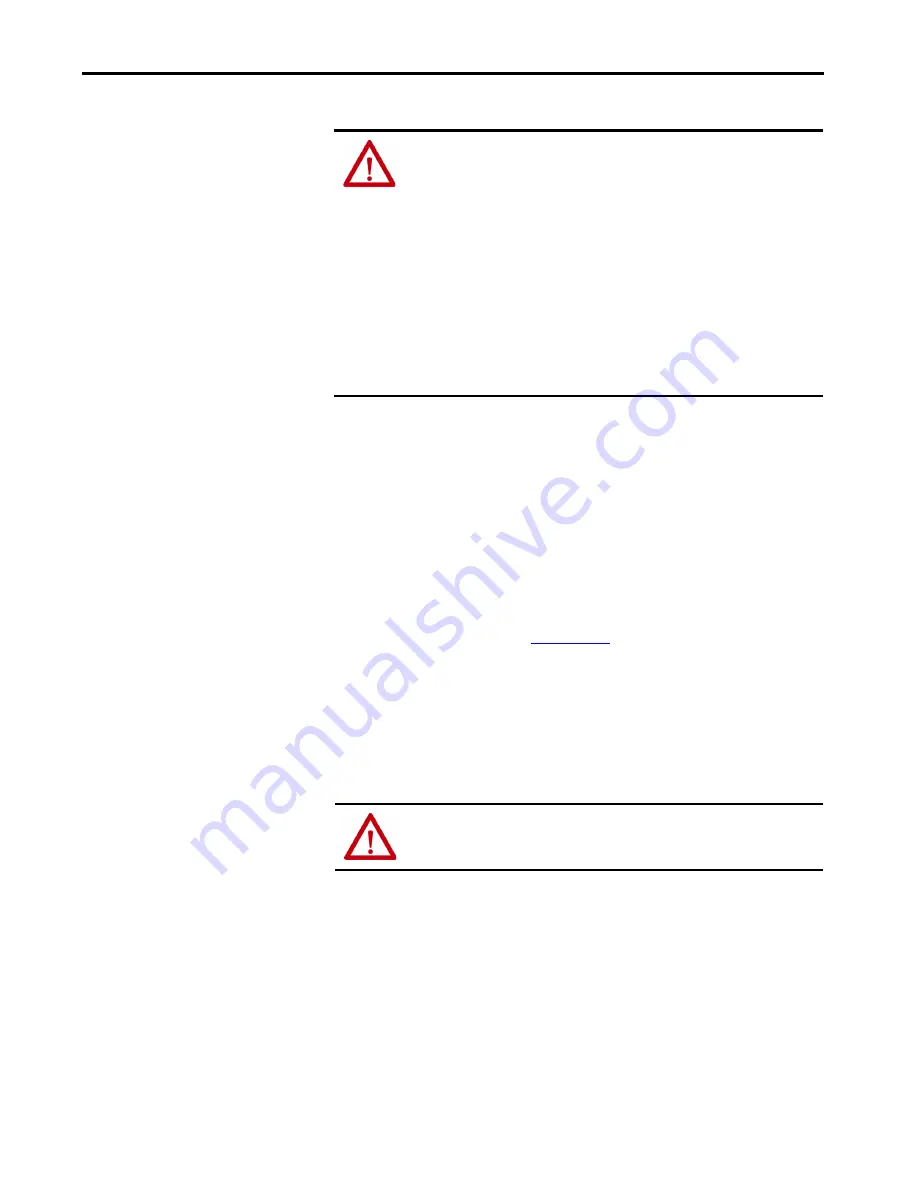
Rockwell Automation Publication 750-UM006C-EN-P - March 2022
197
Periodic and Preventive Maintenance
Chapter 7
Maintenance of Industrial
Control Equipment
Periodic Inspection
— Industrial control equipment must be inspected
periodically. Inspection intervals are based on environmental/operating
conditions, and adjusted as indicated by experience. We recommend an initial
inspection within 3…4 months after installation. We recommend an annual
inspection after initial inspection, and on an ongoing basis.
Real-time Clock
- Factory-installed CR1220 lithium coin cell battery
provides power to the real-time clock (supplied). Preserves the clock setting in
the event power to the drive is lost or cycled. Approximate life is 4.5 years with
drive unpowered, or lifetime if drive is powered. For configuration and
replacement information, refer to the PowerFlex 750-series AC Drives
Reference Manual, publication
Contamination
— If inspection reveals that dust, dirt, moisture, or other
contamination has reached the control equipment, the cause must be
eliminated. This contamination can indicate an incorrect or ineffective
enclosure, unsealed enclosure openings (conduit or other), or incorrect
operating procedures. Dirty, wet, or contaminated parts must be replaced
unless they can be cleaned effectively by vacuuming or wiping.
Cooling Devices
—Inspect the heatsink fan on the back side of the drive.
Replace if the shaft does not turn freely, if blades are missing, or if the fan is not
functioning properly. Apply power momentarily to check operation. If unit
does not operate, replace fan as appropriate.
Predictive Maintenance for Drives
— Predictive Maintenance with Logix
PowerFlex 755 drives contain algorithms for Predictive Maintenance that are
used to improve the uptime of machines, processes, and facilities. These
algorithms monitor the lifespan of certain components. They can be used to
alert personnel when the components are nearing the end of their lifespan so
the components can be replaced before they fail.
ATTENTION:
Performing service on energized Industrial Control Equipment
can be hazardous. Severe injury or death can result from electrical shock,
bumping, or unintended actuation of controlled equipment. Recommended
practice is to disconnect and lock out / tag out control equipment from power
sources, and release stored energy, if present. See National Fire Protection
Association Standard No. NFPA 70E, Part II (as applicable) OSHA rules for
Control of Hazardous Energy Sources (lock out / tag out), and OSHA Electrical
Safety Related Work Practices for safety-related work practices. These
publications include procedural requirements for lock out / tag out,
appropriate work practices, personnel qualifications, and training
requirements where it is not feasible to de-energize and lock out / tag out
electric circuits and equipment before working on or near exposed circuit
parts.
ATTENTION:
Do not use compressed air or similar to clear dust or debris. Use
of compressed air can cause equipment damage or failure.