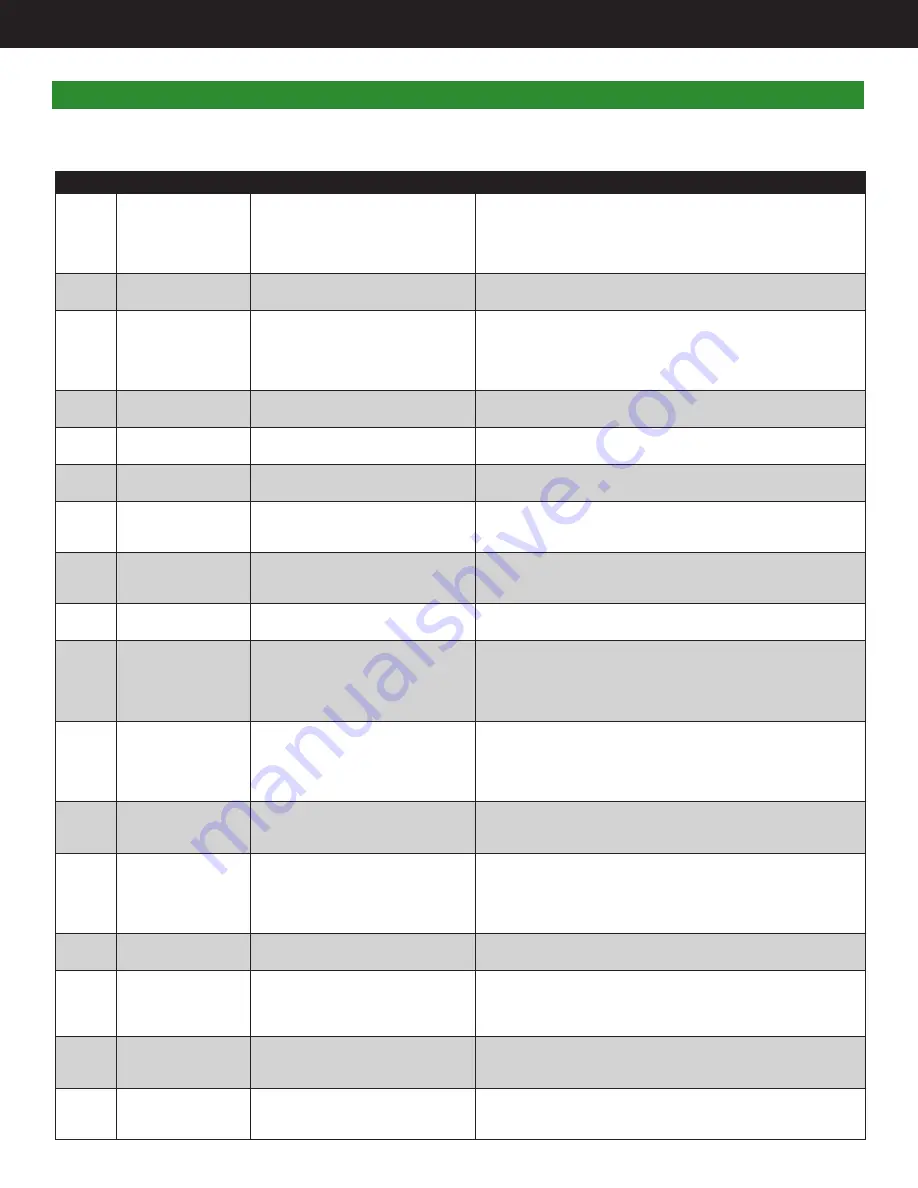
44
AcraDyne Gen IV iAC Controller Manual
Code
Fault Type
Description
Possible Causes
FA01
Torque signal out
of Range
Tool torque signal voltage is
beyond electrical limits
• Tool not connected
• Faulty tool cable
• Faulty transducer
• Transducer electronics not calibrated
• Faulty tool electronics or wiring
FA02
Torque tare value
out of range
Tool torque signal no load
voltage is out of range
•
Transducer electronics significantly out of calibration
• Faulty transducer
FA03
Torque Cal signal
out of Range
Tool does not respond to the full
scale voltage CAL single
• Tool not connected
• Faulty tool cable
• Faulty transducer
• Transducer electronics not calibrated
• Faulty tool electronics or wiring
FH17
1.8vdc MB out of
tolerance
Main board 1.8 bus voltage
exceeds electrical limits
• Faulty Controller main board or other Controller
electronics
FH18
1.8vdc SOM out of
tolerance
System on Module 1.8 bus
voltage exceeds electrical limits
• Faulty Controller main board or other Controller
electronics
FH19
3.3vdc out of
tolerance
Main board 3.3 bus voltage
exceeds electrical limits
• Faulty Controller main board or other Controller
electronics
FH20
5vdc out of
tolerance
5 Volt bus voltage out of range
• Faulty power supply or wiring
• Faulty Controller main board or other Controller
electronics
FH22
24 volt level low
24 Volt I/O power not detected
• Faulty power supply or wiring
• Short or other problem with external connections to
the 24Volt I/O port.
FH23
Controller temp
high
Controller’s internal temperature
exceeds limit
• Ambient air temperature exceeds rating of Controller
FH24
+15vdc out of
tolerance
+15 Volt bus voltage out of
range
• Faulty power supply or wiring
• Faulty Controller main board or other Controller
electronics
• Faulty tool cable
• Faulty tool electronics or wiring
FH25
-15vdc out of
tolerance
-15 Volt bus voltage out of
range
• Faulty power supply or wiring
• Faulty Controller main board or other Controller
electronics
• Faulty tool cable
• Faulty tool electronics or wiring
FS26
Power on throttle
Run command on power up
• Tool laying on lever on power up
• Tool buttons out of calibration
• Run command from logic I/O on power up.
FS27
Locked rotor
Motor has stalled for more than
100 milliseconds
• Poor parameter settings for application.
• Torque signal out of calibration
• Faulty tool gearing or motor
• Corrupted TID parameters
• Faulty Controller or tool electronics
FS28
Target out of
range of tool
Parameter set torque target out
of range of rated tool capability
• Target torque exceeds tool capability
• Corrupted TID parameters
FS29
Invalid tool
Tool configuration not
compatible with parameter set
• Tube nut tool commanded to run a parameter set with
left hand thread direction or with an unfastening stage
• Tube nut tool commanded to go in the disassembly
direction
FS31
Lost Master Start
Signal
Lost Connection to Master
Spindle
• Faulty Ethernet Connection
•
RTOS processor firmware corrupted or not loaded
• Faulty SOM board or connector
FH32
Processor Fault
RTOS processor not
communicating with the
Application processor
• Faulty mainboard electronics
•
RTOS processor firmware corrupted or not loaded
• Faulty SOM board or connector
If an error condition is detected that prevents the tool from running, a fault code will appear on the LED display.
Any active faults are also displayed on GUI RUN screen. Fault history can be viewed in the Controller Error Log.
9. Error Codes