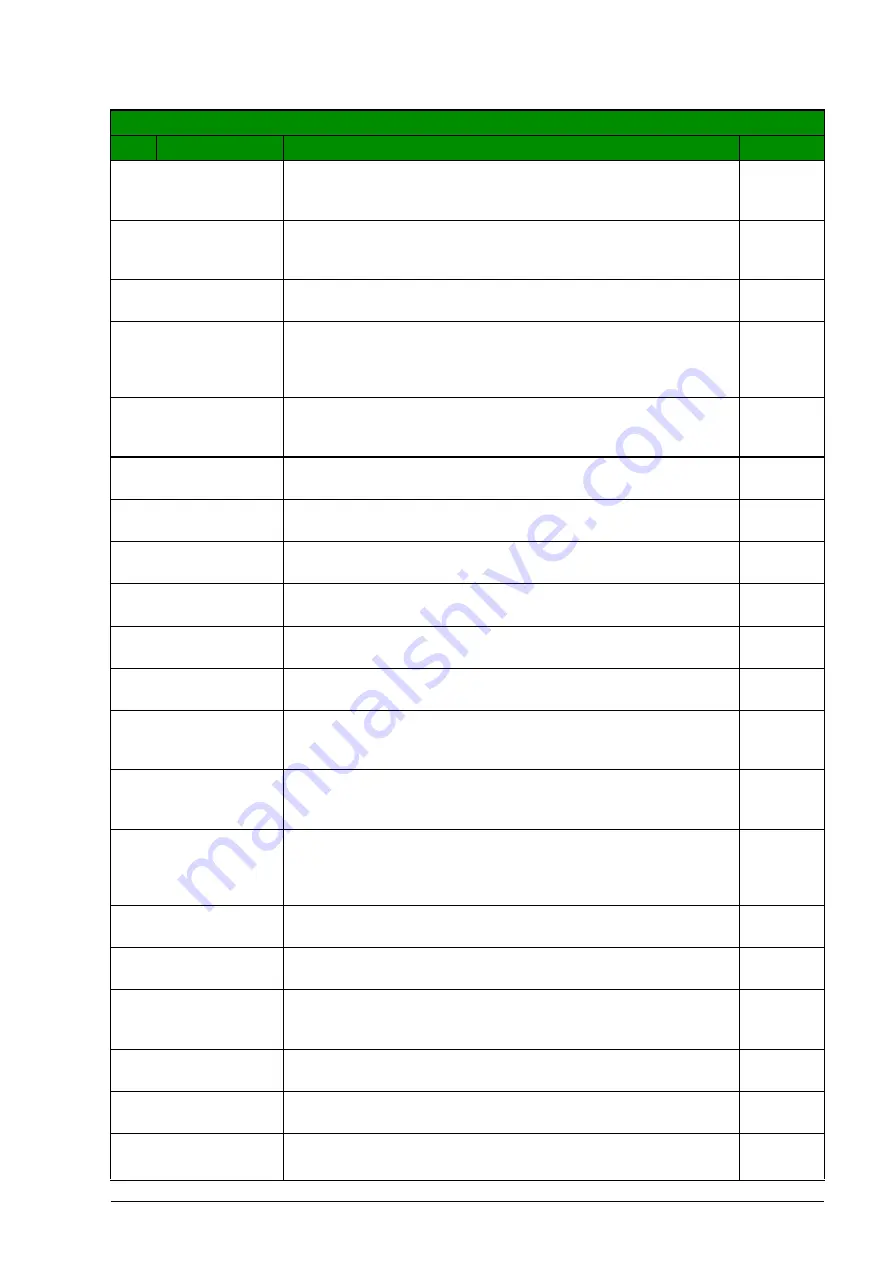
Actual signals and parameters 171
0129 PID 2 SETPNT Setpoint signal (reference) for the PID2 controller. Unit
settings.
-
0130 PID 1 FBK
Feedback signal for the process PID1 controller. Unit
depends on parameter
,
and
settings.
-
0131 PID 2 FBK
Feedback signal for the PID2 controller. Unit depends on
settings.
-
0132 PID 1
DEVIATION
Deviation of the process PID1 controller, ie the difference
between the reference value and the actual value. Unit
depends on parameter
,
and
settings.
-
0133 PID 2
DEVIATION
Deviation of the PID2 controller, ie the difference between
the reference value and the actual value. Unit depends on
settings.
-
0134 COMM RO
WORD
Relay output Control word through fieldbus (decimal). See
.
1 = 1
0135 COMM VALUE
1
Data received from fieldbus
1 = 1
0136 COMM VALUE
2
Data received from fieldbus
1 = 1
0137 PROCESS
VAR 1
Process variable 1 defined by parameter group
-
0138 PROCESS
VAR 2
Process variable 2 defined by parameter group
-
0139 PROCESS
VAR 3
Process variable 3 defined by parameter group
-
0140 RUN TIME
Elapsed drive running time counter (thousands of hours).
Runs when the drive is modulating. Counter cannot be
reset.
1 =
0.01 kh
0141 MWH
COUNTER
MWH counter. The counter value is accumulated till it
reaches 65535 after which the counter rolls over and starts
again from 0. Cannot be reset.
1 =
1 MWh
0142 REVOLUTION
CNTR
Motor revolution counter (millions of revolutions). The
counter can be reset by pressing UP and DOWN keys
simultaneously when the control panel is in the Parameter
mode.
1 =
1 Mrev
0143 DRIVE ON
TIME HI
Drive control board power-on time in days. Counter cannot
be reset.
1 =
1 days
0144 DRIVE ON
TIME LO
Drive control board power-on time in 2 second ticks (30
ticks = 60 seconds). Counter cannot be reset.
1 = 2 s
0145 MOTOR TEMP Measured motor temperature. Unit depends on the sensor
type selected by group
parameters.
1 = 1
0158 PID COMM
VALUE 1
Data received from fieldbus for PID control (PID1 and PID2) 1 = 1
0159 PID COMM
VALUE 2
Data received from fieldbus for PID control (PID1 and PID2) 1 = 1
0160 DI 1-5 STATUS Status of digital inputs.
Example:
10000 = DI1 is on, DI2…DI5 are off.
All actual signals
No.
Name/Value
Description
FbEq
Aotewell Ltd
www.aotewell.com
Industry Automation
HongKong|UK|China
+86-755-8660-6182