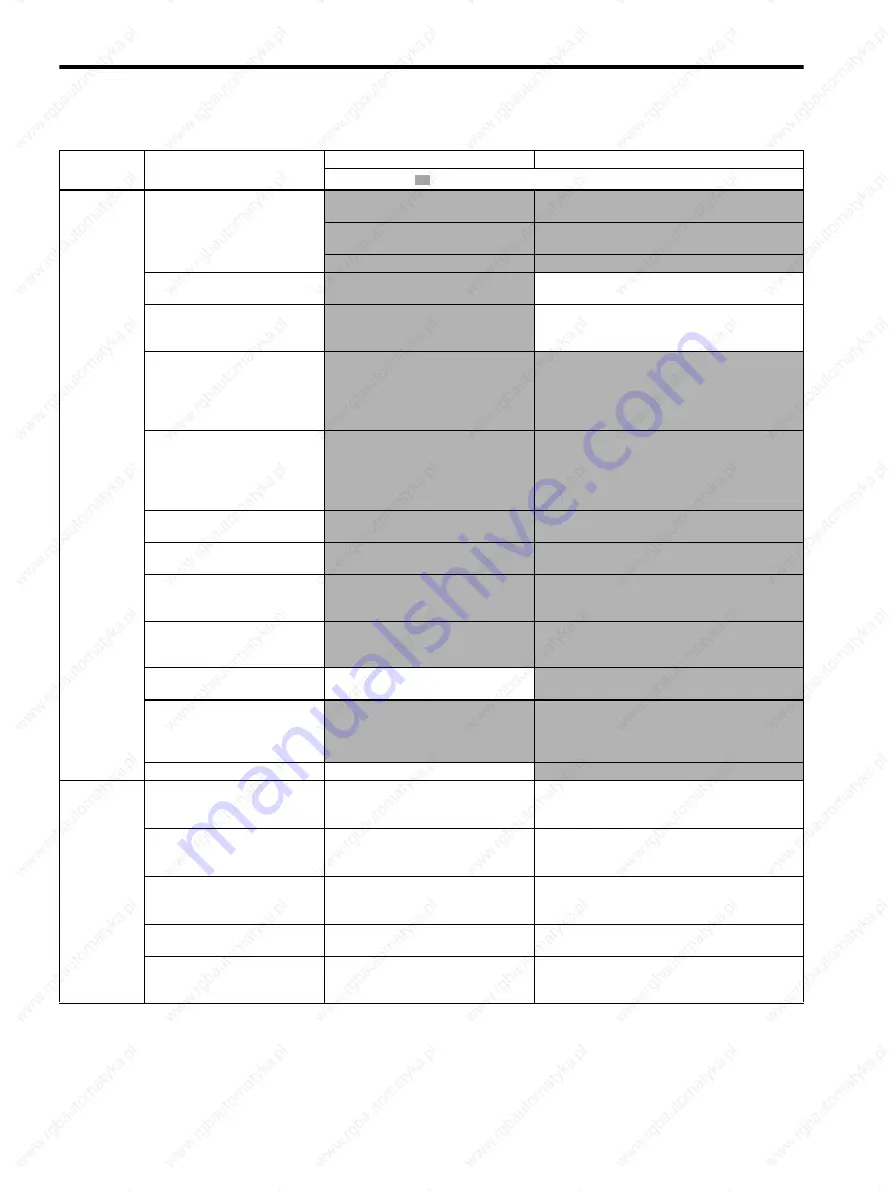
10 Inspection, Maintenance, and Troubleshooting
10.1.5 Troubleshooting for Malfunction without Alarm Display
10-22
Abnormal
Noise from
Servomotor
Mounting not secured
Check if there are any loosen mounting
screws.
Tighten the mounting screws.
Check if there are misalignment of
couplings.
Align the couplings.
Check if there are unbalanced couplings.
Balance the couplings.
Defective bearings
Check for noise and vibration around the
bearings.
If any problems, contact your Yaskawa representative.
Vibration source on the driven
machine.
Any foreign matter, damages, or
deformation on the machine movable
section.
Contact the machine manufacturer.
Noise interference due to incorrect
input signal wire specifications.
The specifications of input signal wires
must be:
Tinned annealed copper twisted-pair or
twisted-pair shielded wires with core 0.12
mm
2
(0.0002 in
2
) min.
Use the specified input signal wires.
Noise interference due to incorrect
encoder cable specifications.
The specifications of encoder cable must
be:
Tinned annealed copper twisted-pair or
twisted-pair shielded wires with core 0.12
mm
2
(0.0002 in
2
) min.
Use the specified encoder cable.
Noise interference due to long
encoder cable wiring distance
The wiring distance must be 20 m(65.6 ft)
max.
Shorten the encoder cable wiring distance to the
specified value.
Noise due to damaged encoder cable
Check if the encoder cable is not damaged
or bent.
Modify the encoder cable layout.
Excessive noise to the encoder cable
Check if the encoder cable is bundled with
high-current line or near the high-current
line.
Install a surge protector to the encoder cable.
FG varies by influence of machines
such as welder on the servomotor
side
Check if the machine is correctly grounded.
Ground the machine separately from PG side FG.
SERVOPACK pulse counting error
due to noise
Check if there is noise interference on the
signal line from encoder.
Take measure against noise for the encoder wiring.
Excessive vibration and shock to the
encoder
Vibration from the machine occurred or
servomotor installation is incorrect.
(Mounting surface accuracy, fixing,
alignment, etc.)
Reduce vibration from the machine, or secure the
servomotor installation.
Encoder fault
An encoder fault occurred.
Replace the motor.
Servomotor
Vibrates at
about 200 to
400 Hz
Speed loop gain value (Pn100) too
high.
Factory setting: Kv=40.0 Hz
Refer to the gain adjustment in User’s
Manual.
Reduce speed loop gain (Pn100) preset value.
Position loop gain value (Pn102) too
high
Factory setting: Kp=40.0,
Refer to the gain adjustment in User’s
Manual.
Reduce position loop gain (Pn102) preset value.
Incorrect speed loop integral time
constant Pn101 setting
Factory setting: Ti=20.00 ms
Refer to the gain adjustment in User’s
Manual.
Correct the speed loop integral time constant Pn101
setting.
When the autotuning is used:
Incorrect machine rigidity setting
Check the machine rigidity setting Fn001.
Select a proper machine rigidity setting Fn001.
When the autotuning is not used:
Incorrect moment of inertia ratio
Pn103.
Check the moment of inertia ratio Pn103.
Correct the moment of inertia ratio Pn103.
Table 10.5 Troubleshooting for Malfunction without Alarm Display (Cont’d)
Symptom
Cause
Inspection
Corrective Actions
: Turn OFF the servo system before executing operations.
Содержание SGDS Sigma III Series
Страница 3: ...SGDS Sigma III Servo Amplifier User Manual for Mechatrolink II Communications...
Страница 21: ......
Страница 29: ...1 Outline 1 8 2 Connecting to SGMSH SGMGH Servomotors Power Supply Three phase 200VAC SGMGH Servomotor...
Страница 59: ...2 System Selection 2 5 4 Regenerative Resistors 2 28...
Страница 68: ...3 3 SERVOPACK Internal Block Diagrams 3 9 3 3 3 Three phase 200 V 1 0 kW...
Страница 82: ...3 7 Dimensional Drawings of Base mounted SERVOPACK Model SGDS 12A 12A 3 23 Three phase 1 5kW...
Страница 133: ...5 Wiring 5 7 2 Connecting Externally Regenerative Resistors 5 28...
Страница 229: ...7 Operation 7 7 4 Absolute Encoder Home Position Offset 7 38...
Страница 375: ...Sigma II User s Manual Index Index 8...