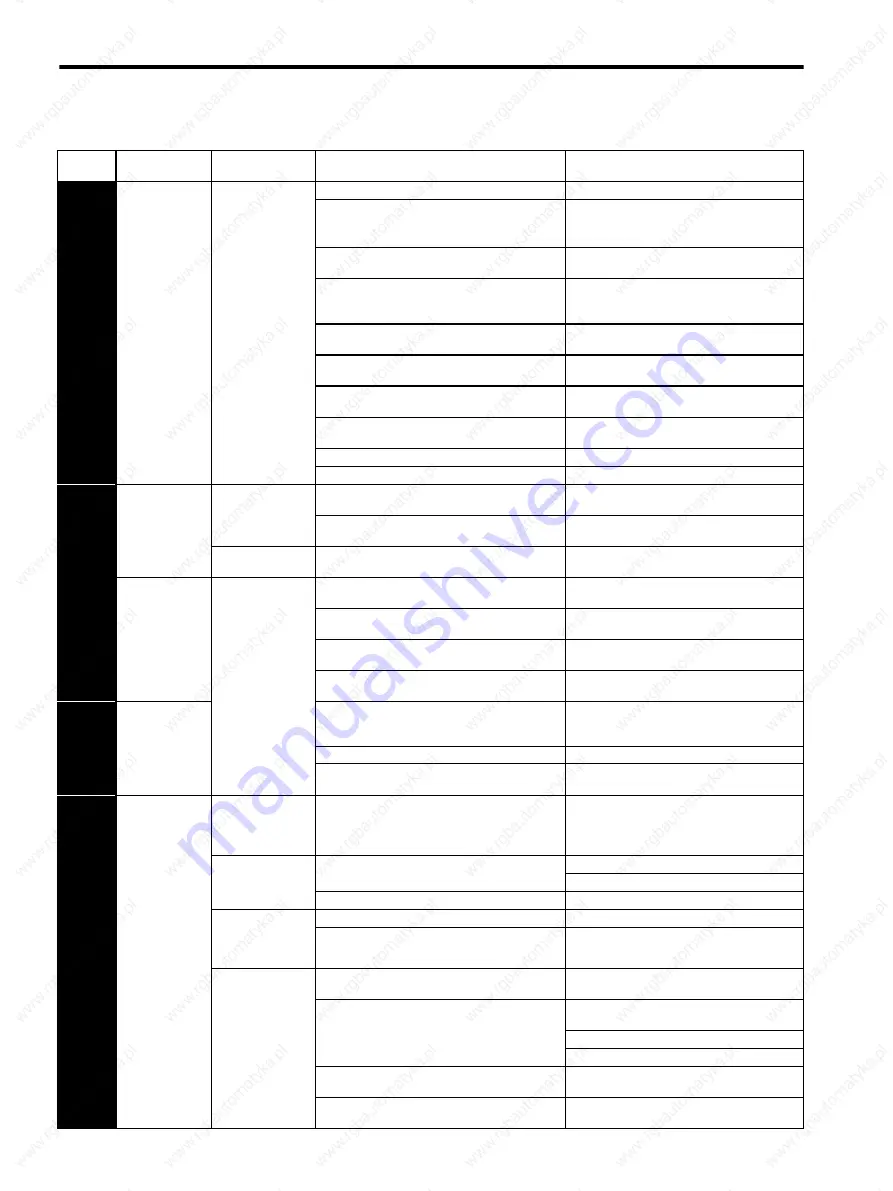
10 Inspection, Maintenance, and Troubleshooting
10.1.4 Troubleshooting of Alarm and Warning
10-16
A.Cb0
Encoder
Echoback Error
Occurred when the
control power
supply was turned
ON or during
operation.
The encoder wiring and contact are incorrect.
Correct the encoder wiring.
Noise interference occurred due to incorrect encoder
cable specifications.
Use tinned annealed copper twisted-pair or
twisted-pair shielded wire with a core of at least
0.12 mm
2
(0.0002 in
2
).
Noise interference occurred because the wiring
distance for the encoder cable is too long.
The wiring distance must be 20m (65.6 ft) max.
Noise interference occurred on the signal line,
because the encoder cable is bent and the sheath is
damaged.
Correct the encoder cable layout.
The encoder cable is bundled with a high-current
line or near a high-current line.
Correct the encoder cable layout so that no surge
is applied.
The FG varies because of the influence from the
servomotor side machines, such as welder.
Ground the machine separately from PG side FG.
Noise interference occurred on the signal line from
the encoder.
Take measures against noise for the encoder
wiring.
Excessive vibration and shocks to the encoder was
applied.
Reduce the machine vibration or mount the
servomotor securely.
An encoder fault occurred.
Replace the servomotor.
A SERVOPACK board fault occurred.
Replace the SERVOPACK.
A.CC0
Multi-turn Limit
Disagreement
Occurred when the
control power
supply was turned
ON.
The parameter settings for the SERVOPACK are
incorrect.
Correct the setting of Pn205 (0 to 65535).
The multi-turn limit value for the encoder is not set
or was changed.
Execute Fn013 at the occurrence of alarm.
Occurred during
operation.
A SERVOPACK board fault occurred.
Replace the SERVOPACK.
A.CF1
Fully-closed
Serial
Converter Unit
Communicatio
ns Error
(Reception
Error)
Occurred when the
control power
supply was turned
ON or during
operation.
Wiring of cable between serial converter unit and
SERVOPACK is incorrect or faulty contact.
Correct the cable wiring.
The specified cable is not used between serial
converter unit and SERVOPACK.
Use the specified cable.
Cable between serial converter unit and
SERVOPACK is too long.
Use 20-m cable max.
Sheath of cable between serial converter unit and
SERVOPACK is broken.
Replace the cable.
A.CF2
Fully-closed
Serial
Converter Unit
Communicatio
ns Error
(Timer Stopped)
Noise interferes with the cable between serial
converter unit and SERVOPACK.
Correct the wiring around serial converter unit,
e.g., separating signal line from power line or
grounding.
A serial converter unit fault occurred.
Replace the serial converter unit.
A SERVOPACK fault occurred.
Replace the SERVOPACK.
A.d00
Position Error
Pulse Overflow
Occurred when the
control power
supply was turned
ON.
A SERVOPACK board fault occurred.
Replace the SERVOPACK.
Occurred at the
servomotor high-
speed operation.
The contact in the servomotor U, V, and W wirings
is faulty.
Correct the servomotor wiring.
Correct the encoder wiring.
A SERVOPACK board fault occurred.
Replace the SERVOPACK.
The servomotor did
not run with
position reference
input.
Wirings of the servomotor U, V, and W are incorrect.
Correct the servomotor wiring.
A SERVOPACK board fault occurred.
Replace the SERVOPACK.
Normal movement,
but occurred with a
long distance
reference input.
The SERVOPACK gain adjustment is improper.
Increase the speed loop gain (Pn100) and position
loop gain (Pn102).
The position reference pulse frequency is too high.
Adjust slowly the position reference pulse
frequency.
Apply the smoothing function.
Correct the electronic gear ratio.
Setting of the parameter Pn520 (Position Error Pulse
Overflow Alarm Level) is incorrect.
Set the parameter Pn520 to proper value.
The servomotor specifications do not meet the load
conditions such as torque and moment of inertia.
Reconsider and correct the load and servomotor
capacity.
Table 10.3 Alarm Display and Troubleshooting (Cont’d)
Alarm
Display
Alarm Name
Situation at Alarm
Occurrence
Cause
Corrective Actions
Содержание SGDS Sigma III Series
Страница 3: ...SGDS Sigma III Servo Amplifier User Manual for Mechatrolink II Communications...
Страница 21: ......
Страница 29: ...1 Outline 1 8 2 Connecting to SGMSH SGMGH Servomotors Power Supply Three phase 200VAC SGMGH Servomotor...
Страница 59: ...2 System Selection 2 5 4 Regenerative Resistors 2 28...
Страница 68: ...3 3 SERVOPACK Internal Block Diagrams 3 9 3 3 3 Three phase 200 V 1 0 kW...
Страница 82: ...3 7 Dimensional Drawings of Base mounted SERVOPACK Model SGDS 12A 12A 3 23 Three phase 1 5kW...
Страница 133: ...5 Wiring 5 7 2 Connecting Externally Regenerative Resistors 5 28...
Страница 229: ...7 Operation 7 7 4 Absolute Encoder Home Position Offset 7 38...
Страница 375: ...Sigma II User s Manual Index Index 8...