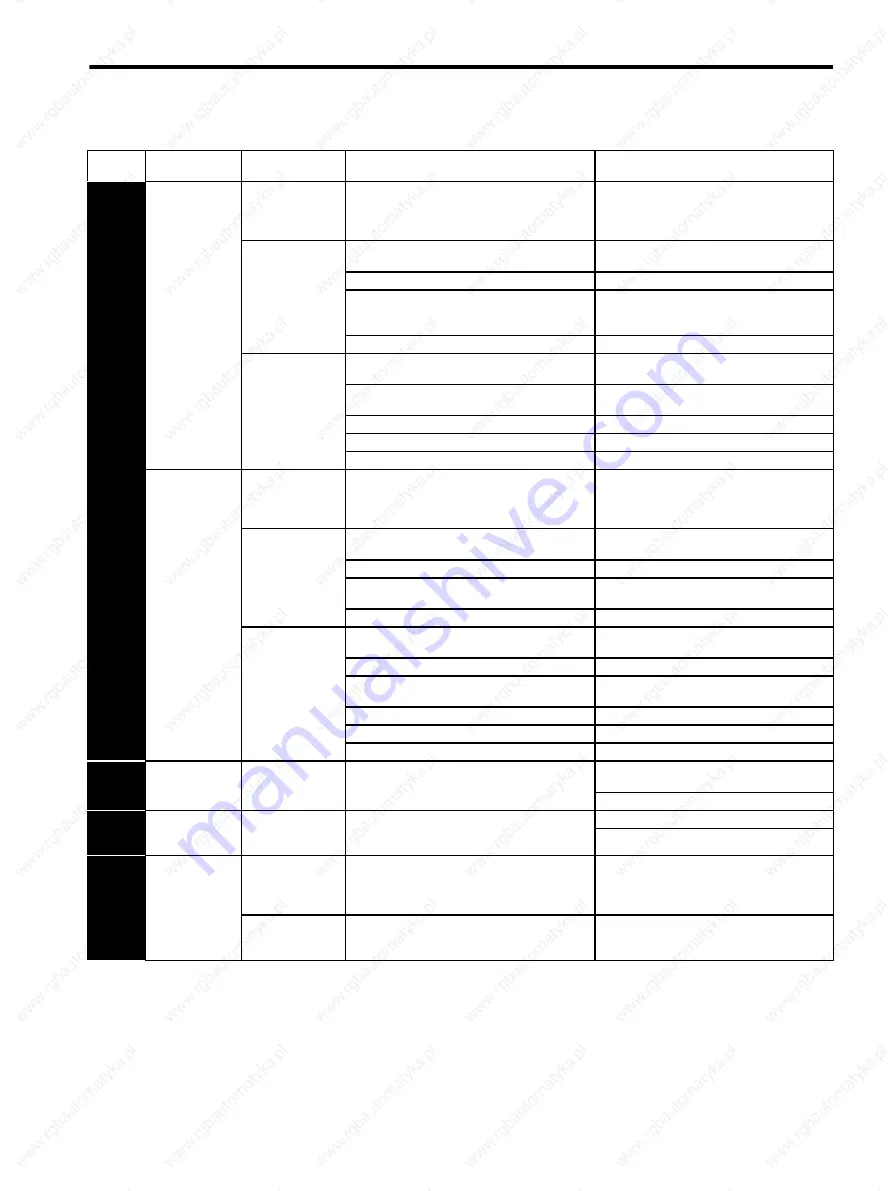
10.1 Troubleshooting
10-11
A.410
Undervoltage
Occurred when the
control power
supply was turned
ON.
A SERVOPACK board fault occurred.
Replace the SERVOPACK.
Occurred when the
main circuit power
supply was turned
ON.
The AC power supply voltage is 120 V or less.
The AC power supply voltage must be within the
specified range.
The fuse of the SERVOPACK is blown out.
Replace the SERVOPACK.
The inrush current limit resistor is disconnected, and
result in an abnormal power supply voltage or in an
overload of the inrush current limit resistor.
Replace the SERVOPACK. Check the power
supply voltage, and reduce the number of times
that the main circuit is turned ON or OFF.)
A SERVOPACK fault occurred.
Replace the SERVOPACK.
Occurred during
normal operation.
The AC power supply voltage was lowered, and
large voltage drop occurred.
The AC power supply voltage must be within the
specified range.
A temporary power failure occurred.
Clear and reset the alarm, and restart the
operation.
The servomotor cable shorts to ground.
Repair or replace the servomotor cable.
The servomotor shorts to ground.
Replace the servomotor.
A SERVOPACK fault occurred.
Replace the SERVOPACK.
A.510
Overspeed
Occurred when the
control power
supply was turned
ON.
A SERVOPACK board fault occurred.
Replace the SERVOPACK.
Occurred when
servo was ON.
The order of phases U, V, and W in the servomotor
wiring is incorrect.
Correct the servomotor wiring.
The encoder wiring is incorrect.
Correct the encoder wiring.
Malfunction occurred due to noise interference in
the encoder wiring.
Take measures against noise for the encoder
wiring.
A SERVOPACK fault occurred.
Replace the SERVOPACK.
Occurred when the
servomotor started
running or in a high
speed run.
The order of phases U, V, and W in the servomotor
wiring is incorrect.
Correct the servomotor wiring.
The encoder wiring is incorrect.
Correct the encoder wiring.
Malfunction occurred due to noise interference in
the encoder wiring.
Take measures against noise for the encoder
wiring.
The position or speed reference input is too large.
Reduce the reference value.
The setting of the reference input gain is incorrect.
Correct the reference input gain setting.
A SERVOPACK board fault occurred.
Replace the SERVOPACK.
A.511
Dividing Pulse
Output
Overspeed
Occurred while the
servomotor was
running.
The output frequency of the dividing pulse exceeds
1.6 MHz.
Lower the setting of the PG dividing pulse
(Pn212).
Reduce the servomotor speed.
A.520
Vibration Alarm
Occurred while the
servomotor was
running.
Abnormal vibration was detected.
Reduce the servomotor speed.
Reduce the speed loop gain (Pn100).
A.710
Overload:
Momentary
Overload
Occurred when the
control power
supply was turned
ON.
A SERVOPACK board fault occurred.
Replace the SERVOPACK.
Occurred when the
servo was turned
ON.
The servomotor wiring is incorrect or the connection
is faulty.
Correct the servomotor wiring.
Table 10.3 Alarm Display and Troubleshooting (Cont’d)
Alarm
Display
Alarm Name
Situation at Alarm
Occurrence
Cause
Corrective Actions
Содержание SGDS Sigma III Series
Страница 3: ...SGDS Sigma III Servo Amplifier User Manual for Mechatrolink II Communications...
Страница 21: ......
Страница 29: ...1 Outline 1 8 2 Connecting to SGMSH SGMGH Servomotors Power Supply Three phase 200VAC SGMGH Servomotor...
Страница 59: ...2 System Selection 2 5 4 Regenerative Resistors 2 28...
Страница 68: ...3 3 SERVOPACK Internal Block Diagrams 3 9 3 3 3 Three phase 200 V 1 0 kW...
Страница 82: ...3 7 Dimensional Drawings of Base mounted SERVOPACK Model SGDS 12A 12A 3 23 Three phase 1 5kW...
Страница 133: ...5 Wiring 5 7 2 Connecting Externally Regenerative Resistors 5 28...
Страница 229: ...7 Operation 7 7 4 Absolute Encoder Home Position Offset 7 38...
Страница 375: ...Sigma II User s Manual Index Index 8...