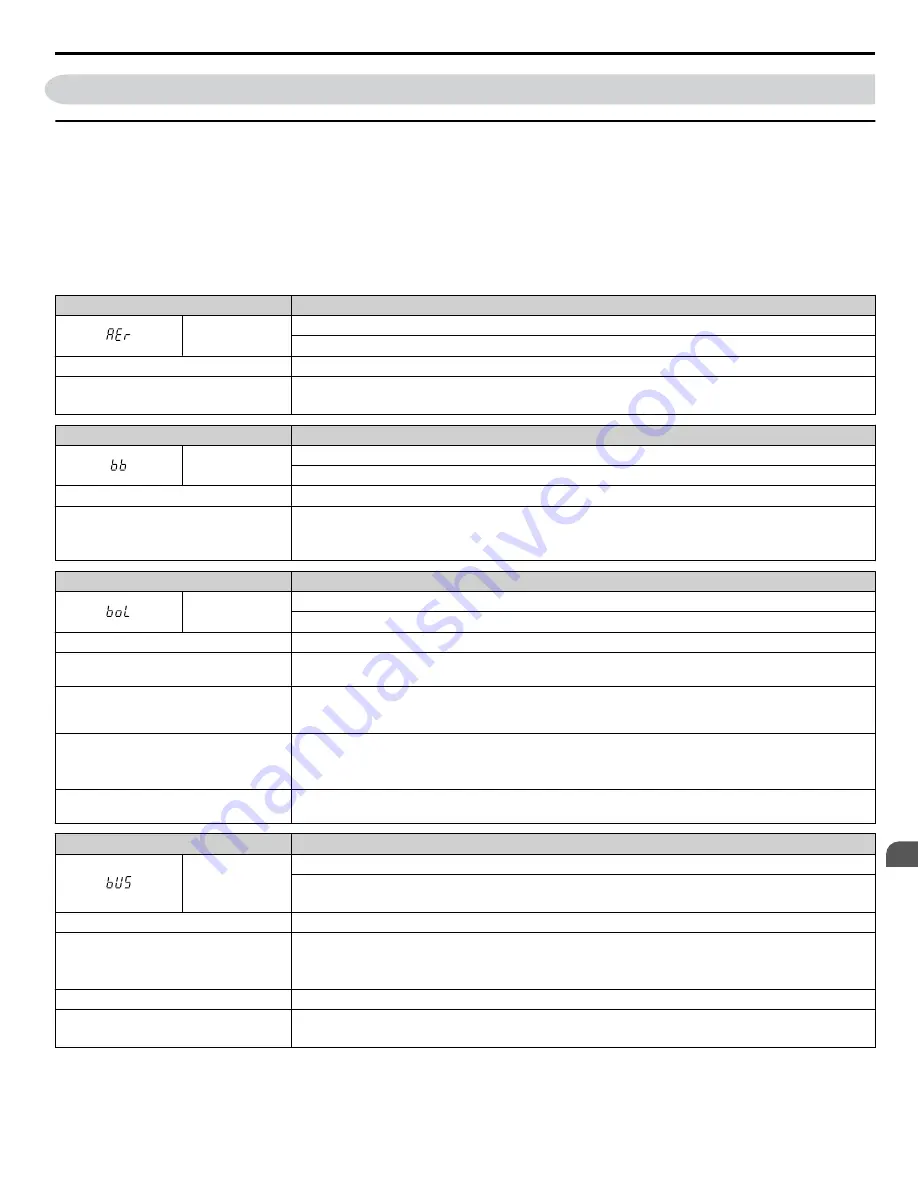
6.5 Alarm Detection
u
Alarm Codes, Causes, and Possible Solutions
Alarms are drive protection functions that do not necessarily cause the drive to stop. After removing the cause of an alarm,
the drive will return to the same status is was before the alarm occurred.
When an alarm has been triggered, the ALM light on the digital operator display blinks and the alarm code display flashes. If
a multi-function output is set for an alarm (H2-
oo
= 10), that output terminal will be triggered.
Note:
If a multi-function output is set to close when an alarm occurs (H2-
oo
= 10), it will also close when maintenance periods are reached,
triggering alarms LT-1 through LT-4 (triggered only if H2-
oo
= 2F).
Table 6.10 Alarm Codes, Causes, and Possible Solutions
Digital Operator Display
Minor Fault Name
AEr
Station Address Setting Error (CC-Link, CANopen, MECHATROLINK)
Option card node address is outside of the acceptable setting range.
Cause
Possible Solutions
Station number is set outside the possible
setting range.
• Set parameter F6-10 to the proper value when using a CC-Link option.
• Set parameter F6-35 to the proper value when using a CANopen option.
Digital Operator Display
Minor Fault Name
bb
Baseblock
Drive output interrupted as indicated by an external baseblock signal.
Cause
Possible Solutions
External baseblock signal was entered via
one of the multi-function input terminals
(S1 to S8).
Check external sequence and baseblock signal input timing.
Note:
Baseblock alarm “bb” will not activate a digital output programmed for minor fault
H2-0
o
= 10. Set H2-0
o
= 8 or 1B to activate a digital output for “bb”.
Digital Operator Display
Minor Fault Name
boL
Braking Transistor Overload Fault
The braking transistor in the drive has been overloaded.
Cause
Possible Solutions
The proper braking resistor has not been
installed.
Select the proper braking resistor.
Use a regen converter, regen unit, braking
unit, or other device to connect the +1 or +3
terminal to the - terminal.
Set L8-55 to 0 to disable Internal Braking Transistor Protection.
The use rate of the braking transistor is high
(i.e., the regen converter is large or the
repetition frequency is high).
• Change to a CDBR type braking unit.
• Change to a regen converter.
• Increase the deceleration time.
The braking transistor inside the drive is
faulty.
Replace the drive.
Digital Operator Display
Minor Fault Name
bUS
Option Communication Error
• The connection was lost after initial communication was established.
• Assign a Run command frequency reference to the option.
Cause
Possible Solutions
Connection is broken or master controller
stopped communicating.
• Check for faulty wiring.
• Correct the wiring.
• Check for disconnected cables and short circuits. Repair as needed.
Option is damaged.
If there are no problems with the wiring and the fault continues to occur, replace the option.
The option is not properly connected to the
drive.
• The connector pins on the option are not properly lined up with the connector pins on the drive.
• Reinstall the option.
6.5 Alarm Detection
YASKAWA SIEP YAIP1U 01C AC Drive - P1000 Technical Manual
311
6
Troubleshooting
Содержание P1000
Страница 4: ...This Page Intentionally Blank 4 YASKAWA SIEP YAIP1U 01C AC Drive P1000 Technical Manual...
Страница 26: ...i 2 General Safety This Page Intentionally Blank 26 YASKAWA SIEP YAIP1U 01C AC Drive P1000 Technical Manual...
Страница 140: ...4 11 Test Run Checklist This Page Intentionally Blank 140 YASKAWA SIEP YAIP1U 01C AC Drive P1000 Technical Manual...
Страница 430: ...A 4 Drive Derating Data This Page Intentionally Blank 430 YASKAWA SIEP YAIP1U 01C AC Drive P1000 Technical Manual...
Страница 504: ...B 16 Defaults by Drive Model This Page Intentionally Blank 504 YASKAWA SIEP YAIP1U 01C AC Drive P1000 Technical Manual...
Страница 568: ...D 3 UL and CSA Standards This Page Intentionally Blank 568 YASKAWA SIEP YAIP1U 01C AC Drive P1000 Technical Manual...
Страница 591: ...Index This Page Intentionally Blank YASKAWA SIEP YAIP1U 01C AC Drive P1000 Technical Manual 591...
Страница 593: ......