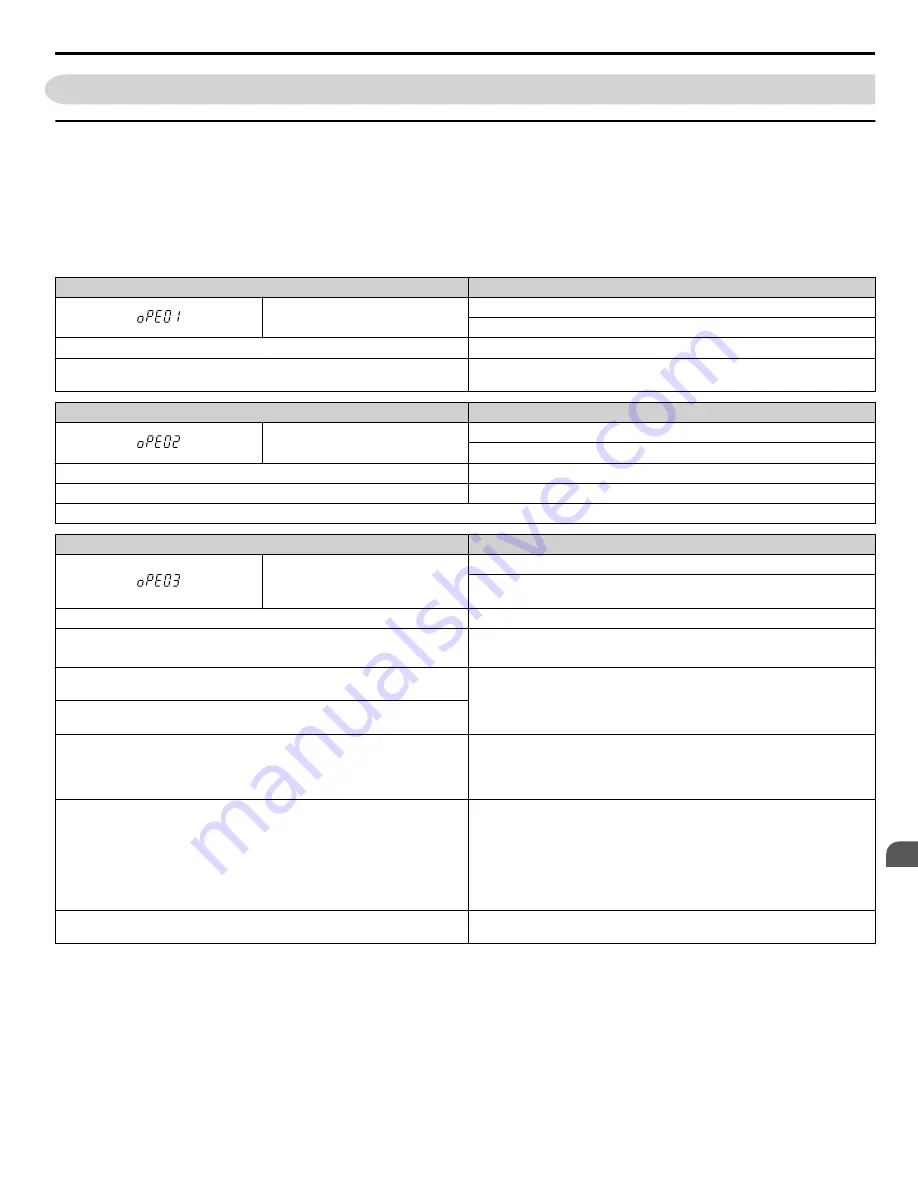
6.6 Operator Programming Errors
u
Operator Programming Error Codes, Causes, and Possible Solutions
An Operator Programming Error (oPE) occurs when a contradictory parameter is set or an individual parameter is set to an
inappropriate value.
The drive will not operate until the parameter or parameters causing the problem are set correctly. An oPE, however, does not
trigger an alarm or fault output. If an oPE occurs, investigate the cause and refer to
for the appropriate action. When
an oPE appears on the operator display, press the ENTER button to view U1-18 and see which parameter is causing the oPE.
Table 6.11 oPE Codes, Causes, and Possible Solutions
Digital Operator Display
Error Name
oPE01
Drive Capacity Setting Fault
Drive capacity and the value set to o2-04 do not match.
Cause
Possible Solutions
The drive model selection (o2-04) and the actual capacity of the drive are
not the same.
Correct the value set to o2-04.
Digital Operator Display
Error Name
oPE02
Parameter Range Setting Error
Use U1-18 to find parameters set outside the range.
Cause
Possible Solutions
Parameters were set outside the possible setting range.
Set parameters to the proper values.
Note:
When multiple errors occur simultaneously, other errors are given precedence over oPE02.
Digital Operator Display
Error Name
oPE03
Multi-Function Input Selection Error
A contradictory setting is assigned to multi-function contact inputs H1-01
to H1-08.
Cause
Possible Solutions
• The same function is assigned to two multi-function inputs.
• Excludes “Not used” and “External Fault.”
• Ensure all multi-function inputs are assigned to different functions.
• Re-enter the multi-function settings to ensure this does not occur.
The Up command was set but the Down command was not, or vice versa
(settings 10 vs. 11).
Properly set the functions that required for use in combination with other
functions.
The Up 2 command was set but the Down 2 command was not, or vice versa
(settings 75 vs. 76).
• Run/Stop command for a 2-wire sequence was set (H1-
oo
= 42), but
Forward/Reverse command (H1-
oo
= 43) was not.
• “Drive Enable” is set to multi-function input S1 or S2 (H1-01 = 6A or
H1-02 = 6A).
Properly set the functions that required for use in combination with other
functions.
Two of the following functions are set simultaneously:
• Up/Down Command (10 vs. 11)
• Up 2/Down 2 Command (75 vs. 76)
• Hold Accel/Decel Stop (A)
• Analog Frequency Reference Sample/Hold (1E)
• Offset Frequency 1, 2, 3 Calculations (44, 45, 46)
• Check if contradictory settings have simultaneously been assigned to the
multi-function input terminals.
• Correct setting errors.
The Up/Down command (10, 11) and PID control (b5-01) are enabled
simultaneously.
Set b5-01 to 0 to disable control PID or disable the Up/Down command.
6.6 Operator Programming Errors
YASKAWA SIEP YAIP1U 01C AC Drive - P1000 Technical Manual
319
6
Troubleshooting
Содержание P1000
Страница 4: ...This Page Intentionally Blank 4 YASKAWA SIEP YAIP1U 01C AC Drive P1000 Technical Manual...
Страница 26: ...i 2 General Safety This Page Intentionally Blank 26 YASKAWA SIEP YAIP1U 01C AC Drive P1000 Technical Manual...
Страница 140: ...4 11 Test Run Checklist This Page Intentionally Blank 140 YASKAWA SIEP YAIP1U 01C AC Drive P1000 Technical Manual...
Страница 430: ...A 4 Drive Derating Data This Page Intentionally Blank 430 YASKAWA SIEP YAIP1U 01C AC Drive P1000 Technical Manual...
Страница 504: ...B 16 Defaults by Drive Model This Page Intentionally Blank 504 YASKAWA SIEP YAIP1U 01C AC Drive P1000 Technical Manual...
Страница 568: ...D 3 UL and CSA Standards This Page Intentionally Blank 568 YASKAWA SIEP YAIP1U 01C AC Drive P1000 Technical Manual...
Страница 591: ...Index This Page Intentionally Blank YASKAWA SIEP YAIP1U 01C AC Drive P1000 Technical Manual 591...
Страница 593: ......