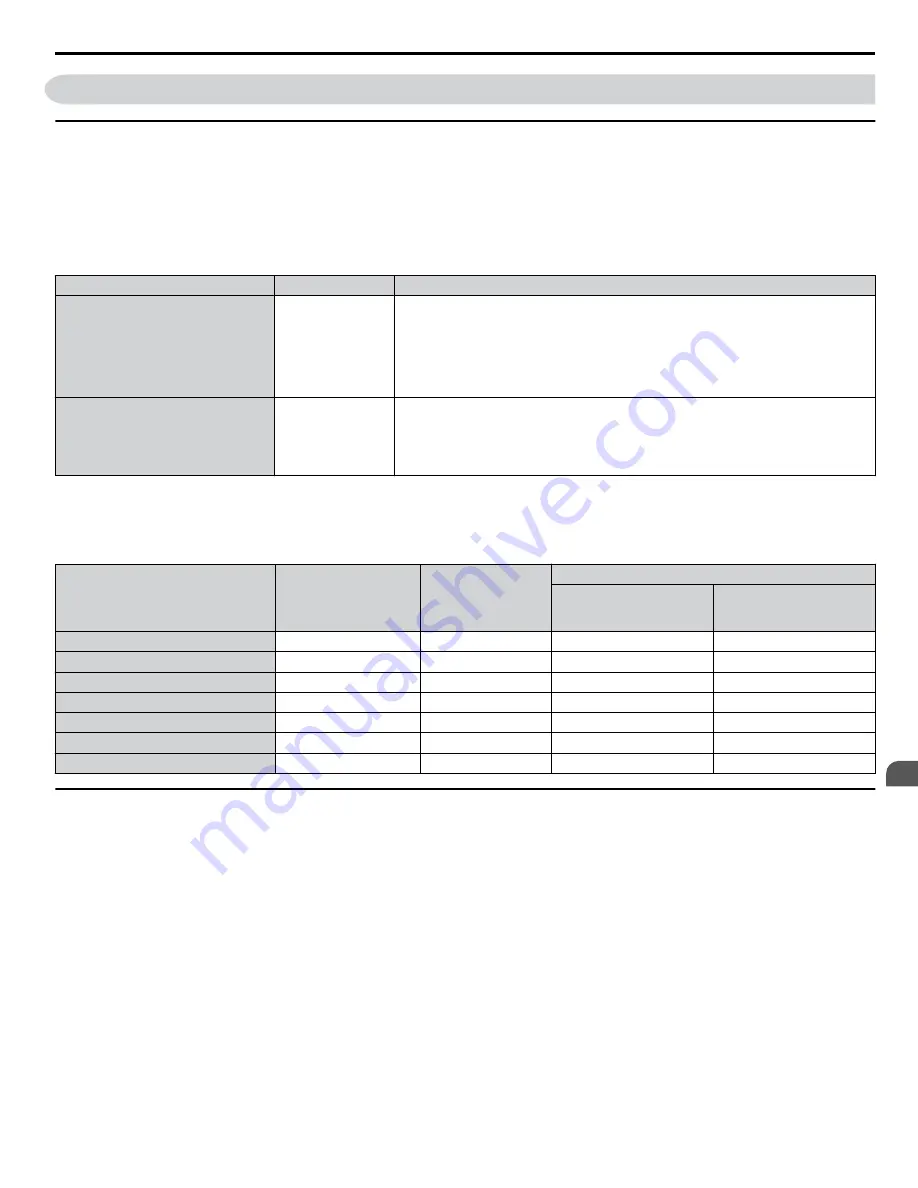
4.7 Auto-Tuning
u
Types of Auto-Tuning
The drive offers different types of Auto-Tuning for induction motors. Refer to the tables below to select the type of Auto-
Tuning that bests suits the application.
Refer to Start-Up Flowchart on page 124
for directions on executing Auto-Tuning.
n
Auto-Tuning for Induction Motors
This feature automatically sets the V/f pattern and motor parameters E1-
oo
and E2-
oo
for an induction motor.
Table 4.12 Types of Auto-Tuning for Induction Motors
Type
Setting
Application Conditions and Benefits
Stationary Auto-Tuning for Line-to-
Line Resistance
T1-01 = 2
• The drive is used in V/f Control and other Auto-Tuning selections are not possible.
• Perform when entering motor data manually while using motor cables longer than 50
m.
• Drive and motor capacities differ.
• Tunes the drive after the cable between the drive and motor has been replaced with a
cable over 50 m long. Assumes Auto-Tuning has already been performed.
Rotational Auto-Tuning for V/f
Control
T1-01 = 3
• Recommended for applications using Speed Estimation Speed Search or using the
Energy Saving function in V/f Control.
• Assumes motor can rotate while Auto-Tuning is executed. Increases accuracy for
certain functions like torque compensation, slip compensation, Energy Saving, and
Speed Search.
The necessary information is usually listed on the motor nameplate or in the motor test report provided by the motor
Refer to Start-Up Flowchart on page 124
for details on the Auto-Tuning process.
Table 4.13 Auto-Tuning Input Data
Input Value
Input Parameter
Unit
Tuning Type (T1-01)
2
Line-to-Line Resistance
3
Rotational for V/f
Control
Motor rated power
T1-02
kW
YES
YES
Motor rated voltage
T1-03
Vac
–
YES
Motor rated current
T1-04
A
YES
YES
Motor rated frequency
T1-05
Hz
–
YES
Number of motor poles
T1-06
-
–
YES
Motor rated Speed
T1-07
r/min
–
YES
Motor iron loss
T1-11
W
–
YES
u
Before Auto-Tuning the Drive
Check the items below before Auto-Tuning the drive.
n
Basic Auto-Tuning Preparations
• Auto-Tuning requires the user to input data from the motor nameplate or motor test report. Make sure this data is available
before Auto-Tuning the drive.
• For best performance, the drive input supply voltage must be at least equal to or greater than the motor rated voltage.
Note:
Better performance is possible when using a motor with a base voltage that is lower than the input supply voltage (20 V for 200 V class
models, 40 V for 400 V class models, and 60 V for 600 V class models). This is particularly important when operating the motor above
90% of base speed, where high torque precision is required.
• To cancel Auto-Tuning, press the STOP key on the digital operator.
• When using a motor contactor, make sure it is closed throughout the Auto-Tuning process.
describes digital input and output terminal operation while Auto-Tuning is executed.
4.7 Auto-Tuning
YASKAWA SIEP YAIP1U 01C AC Drive - P1000 Technical Manual
129
4
Start-Up Programming & Operation
Содержание P1000
Страница 4: ...This Page Intentionally Blank 4 YASKAWA SIEP YAIP1U 01C AC Drive P1000 Technical Manual...
Страница 26: ...i 2 General Safety This Page Intentionally Blank 26 YASKAWA SIEP YAIP1U 01C AC Drive P1000 Technical Manual...
Страница 140: ...4 11 Test Run Checklist This Page Intentionally Blank 140 YASKAWA SIEP YAIP1U 01C AC Drive P1000 Technical Manual...
Страница 430: ...A 4 Drive Derating Data This Page Intentionally Blank 430 YASKAWA SIEP YAIP1U 01C AC Drive P1000 Technical Manual...
Страница 504: ...B 16 Defaults by Drive Model This Page Intentionally Blank 504 YASKAWA SIEP YAIP1U 01C AC Drive P1000 Technical Manual...
Страница 568: ...D 3 UL and CSA Standards This Page Intentionally Blank 568 YASKAWA SIEP YAIP1U 01C AC Drive P1000 Technical Manual...
Страница 591: ...Index This Page Intentionally Blank YASKAWA SIEP YAIP1U 01C AC Drive P1000 Technical Manual 591...
Страница 593: ......