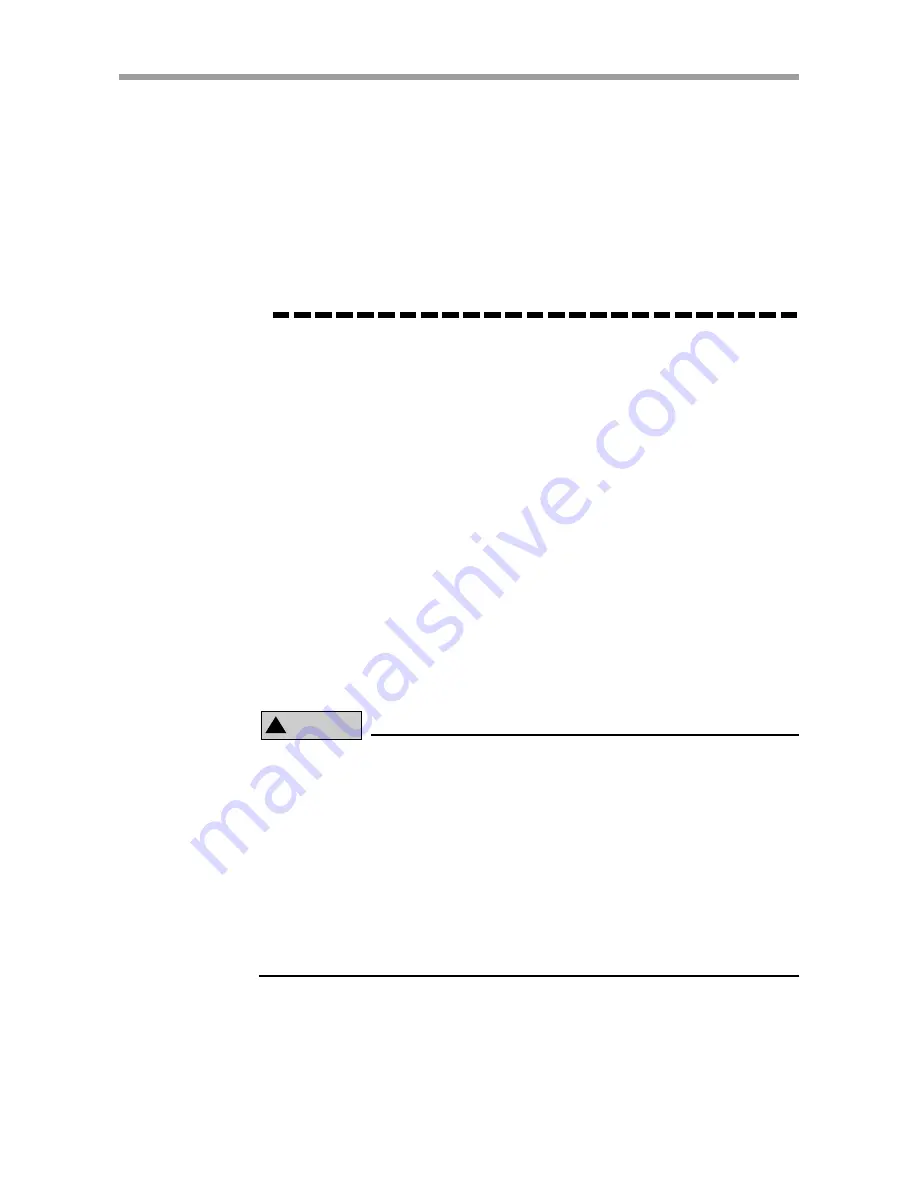
54
CHAPTER2 PROFIBUS Unit
(3)
The corresponding point number P6 is output to PO200 through PO203 (P201,
P202 are on; P200, P203 are off) because the robot is within the P6
±
OUT
valid position range (point zone output range), and because P6 is the move-
ment point. ZONE 0 remains off at this time because the robot is not within the
specified zone output range.
(4)
The ZONE 0 output turns on because the robot is within the specified zone
output range (P900 to P901). All the PO200 to PO203 target position point
number outputs are off at this time because the robot is not within any point
zone output range.
M E M O
M E M O
• The movement point zone output function is supported by the following controller
versions.
ERCX, SRCX
: Ver. 13.64 or later
DRCX
: Ver. 18.64 or later
SRCP, SRCD
: Ver. 24.21 or later
SRCP30 : Ver. 24.30H or later
• When using an option unit, the corresponding point number for the movement point
zone output function is output to both the corresponding parallel I/O (PO0 to PO5)
and the serial I/O (PO200 to PO205). In the SRCP/SRCD series, however, the point
number is only output to the serial I/O.
• The movement point number specified just prior to movement START by point
movement command (ABS-PT, INC-PT) is registered as the movement point.
• Because movement points are reset immediately after a controller power on, all PO
outputs turn off. Movement points are also reset when the RESET command is
executed, and movement point zone outputs by PO are cleared.
• The position judgment parameter for selecting the point zone judgment method can
be set to either "OUT valid position" or "Positioning-completed pulse" (this is speci-
fied in the "thousands" place of the I/O assignment selection parameter).
• The "OUT valid position" can be changed by parameter setting (single-axis con-
trollers: PRM20, dual-axis controllers: PRM56 for X-axis, PRM96 for Y-axis).
• The "Positioning-completed pulse" can be changed parameter setting (single-axis
controllers: PRM6, dual-axis controllers: PRM53 for X-axis, PRM93 for Y-axis).
!
CAUTION
• All the PO200 to PO205 outputs are off when the robot is not within the point
zone output range.
• A 10ms sampling time is needed for position monitoring, so the point zone
output may not be detected during high-speed robot motion.
• For movement point zone output and zone output, PO and ZONE0 to ZONE3
are output only when the all axes of the robot are within the output range
specified for each zone.
• When outputting point 0 (P0) as the corresponding point for the movement
point zone output function, all the PO200 to PO205 outputs remain off (be-
cause P0 = 000000
(binary)
). Therefore, the PO200 to PO205 statuses do not change
even after the robot has entered the zone specified by P0. This should be kept
in mind when monitoring P0.