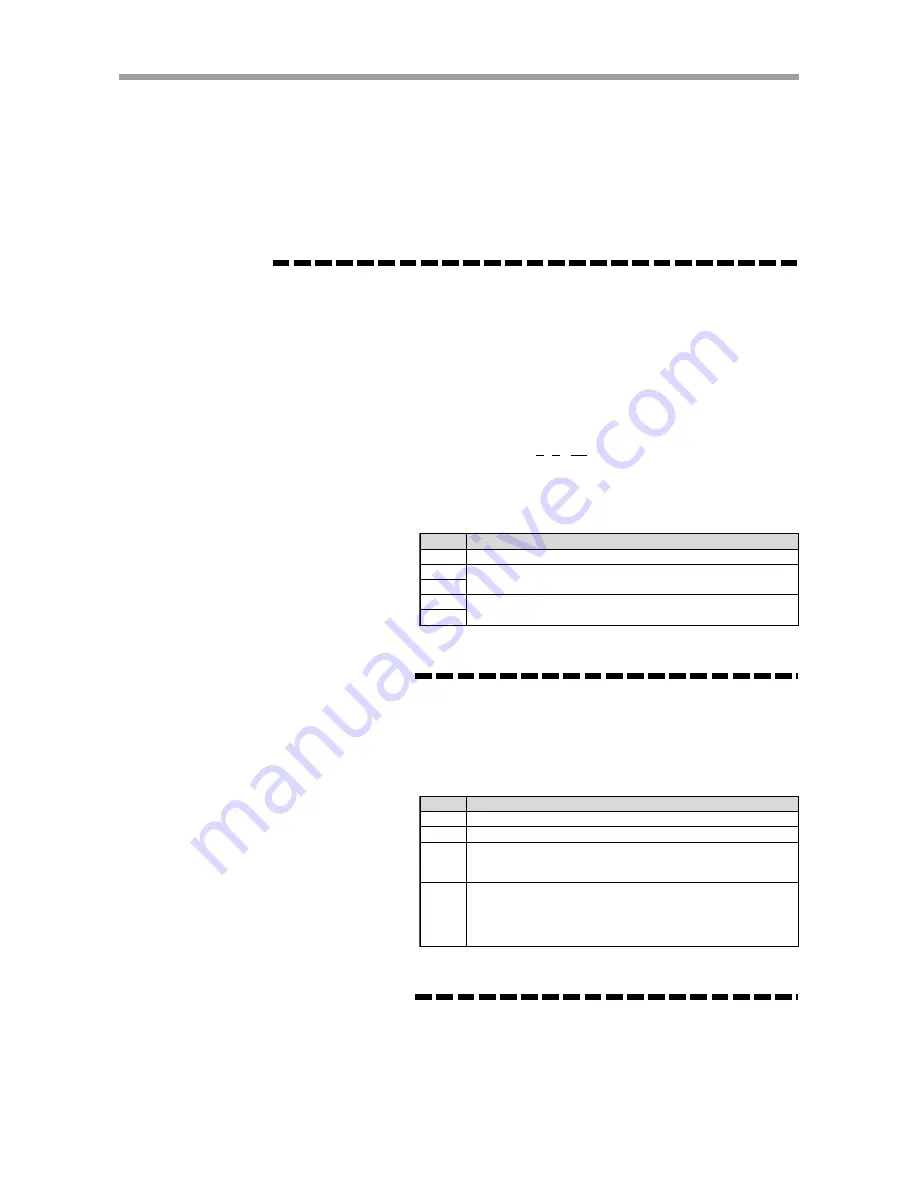
38
CHAPTER2 PROFIBUS Unit
2-9-3
I/O assignment selection parameter description
The I/O assignment selection parameter (single-axis controllers: PRM59, dual-axis con-
trollers: PRM26) selects the function to be assigned to each I/O signal.
This parameter setting allows changing the function assigned to each I/O signal. This
makes it possible to output the destination point number and perform jog movement.
After changing the I/O assignment, the controller must be restarted to enable the changes.
M E M O
M E M O
The I/O assignment selection parameter is supported by the following controller ver-
sions:
ERCX, SRCX : Ver. 13.57 or later
DRCX
: Ver. 18.57 or later
SRCP, SRCD
: Ver. 24.17 or later
SRCP30
: Ver. 24.30H or later
I/O assignment selection parameter
Parameter number
Single-axis controllers : PRM59
Dual-axis controllers
: PRM26
Input range
0 or another number (Refer to "2-9-2 I/O assignment list".)
Meaning
PRM59/PRM26 = x x xx
↑ ↑ ↑
e w q
q
I/O assignment type selection
00
20
21
30
31
Description
Value
Type 0 (Conventional type/standard)
Type 2 (Point number output type)
Type 3 (Point teaching type)
M E M O
M E M O
Type 1 cannot be used with the SRCP, SRCD, SRCX, SRCX,
and DRCX.
w
Point output selection
Make setting only for Type 2 (Point number output type) or
Type 3 (Point teaching type).
0
1
2
3
Description
Value
Outputs PO when movement ends normally.
Outputs PO when movement command is received.
Point zone output
Outputs PO when the robot enters the
±
position judgment parameter
range for point data registered in the controller.
Movement point zone output
Outputs PO when the robot enters the
±
position judgment parameter
range for point data that is registered in the controller and serves as the
movement target position of a point movement command (ABS-PT,
INC-PT).
M E M O
M E M O
The movement point zone output is supported by the following
controller versions:
ERCX, SRCX : Ver. 13.64 or later DRCX : Ver. 18.64 or later
SRCP, SRCD : Ver. 24.21 or later SRCP30 : Ver. 24.30H or later