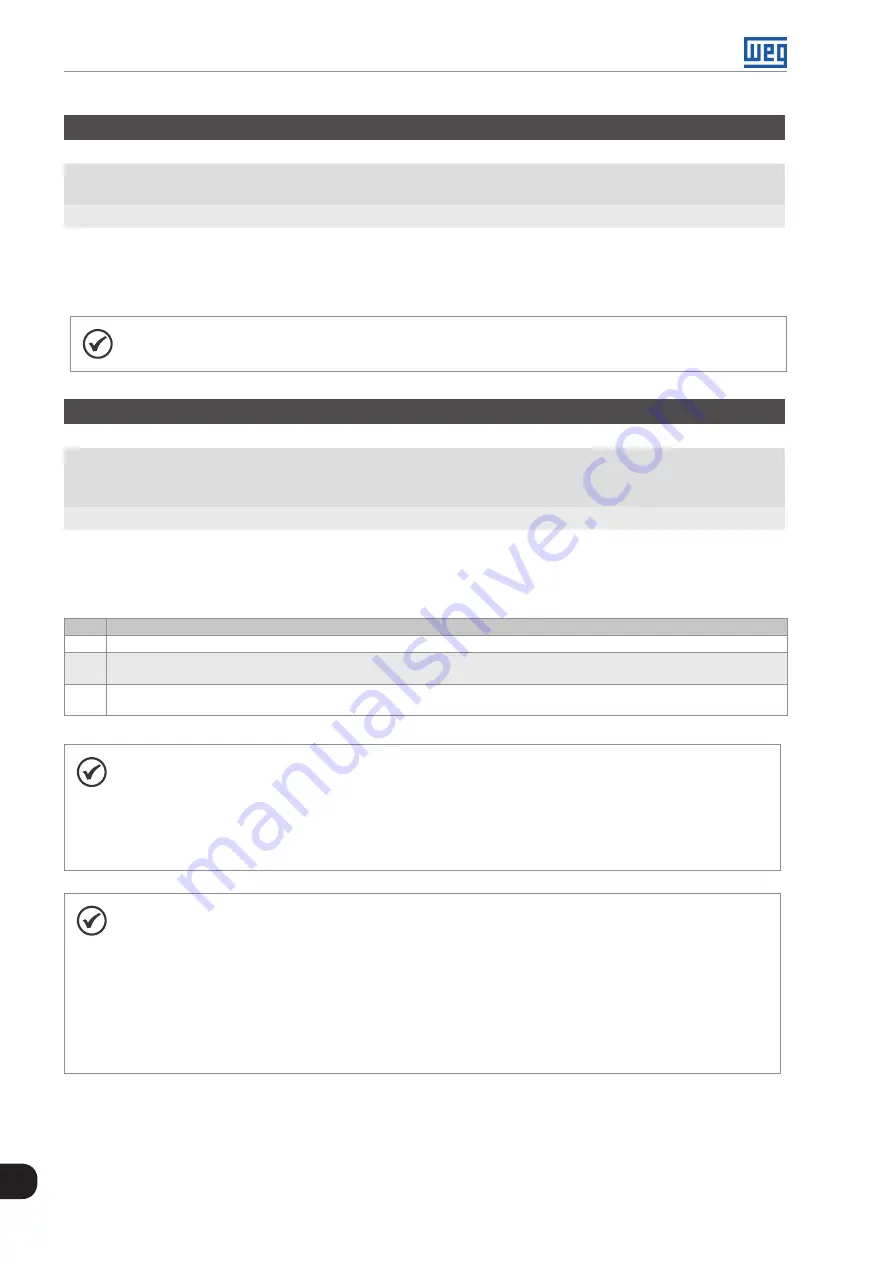
SoftPLC
18-14 | CFW300
18
P927 – Time for Low Level Fault for the Control Process Variable (F763)
Adjustable
Range:
0.0 to 999.9 s
Factory
Setting:
0.0 s
Properties:
Description:
This parameter defines how long the high level alarm condition should remain so that the control process variable
(A762) will generate fault “F763: High Level Fault of the Control Process Variable”.
NOTE!
Setting it to "0.0 s" disables the high level fault for the control process variable.
P928 – Selection of the PID Controller Control Action
Adjustable
Range:
0 = Disable PID Controller
1 = Enable PID Controller in Direct Mode
2 = Enable PID Controller in Reverse Mode
Factory
Setting:
0
Properties:
cfg
Description:
This parameter enables the PID controller and defines how the control action will be.
Table 18.9:
Description of the PID controller control action
P928
Description
0
It defines that the PID controller will be disabled
1
It defines that the PID controller will be enabled, and the regulation or control action will be in direct mode. In other words, the
error will be the control setpoint value (P911) minus the control process variable value (P916)
2
It defines that the PID controller will be enabled, and the regulation or control action will be in reverse mode. In other words, the
error will be the control process variable value (P916) minus the control setpoint value (P911)
NOTE!
When enabling the PID controller, that is, changing the content of parameter P928 from 0 to 1 or 2,
the following parameters related to the PID controller application will be loaded: P100, P101, P133,
P134, P205, P207, P208, P209, P210, P213, P220, P221, P224, P231, P232, P233, P234, P235,
P263, P264, P510, P511, P911, P918, P920, P921, P922, P923, P924, P925, P926, P927, P929,
P930, P931, P932, P933, P934, P935, P936, P937, P938, P939.
NOTE!
The control action of the PID controller must be selected for direct mode when it is necessary to
increase the PID controller output in order to increase the process variable value. E.g.: Pump driven
by an inverter and filling a tank. For the level of the tank (process variable) to increase, it is necessary
that the flow increase, which is accomplished by increasing the speed of the motor.
The control action of the PID controller must be selected for reverse mode when it is necessary to
decrease the PID controller output in order to increase the process variable value. E.g.: Fan driven by
inverter cooling a refrigeration tower. When an increase in temperature is desired (process variable),
it is necessary to reduce the ventilation by reducing the motor speed.
Содержание CFW300 V1.3X
Страница 2: ......
Страница 8: ...Contents...
Страница 46: ...Identification of the Inverter Model and Accessories 6 4 CFW300 6...
Страница 60: ...Logical Command and Speed Reference 7 14 CFW300 7...
Страница 72: ...V f Scalar Control 9 10 CFW300 9...
Страница 80: ...VVW Vector Control 10 8 CFW300 10...
Страница 116: ...Digital and Analog Inputs and Outputs 12 24 CFW300 12...
Страница 132: ...Reading Parameters 15 6 CFW300 15...