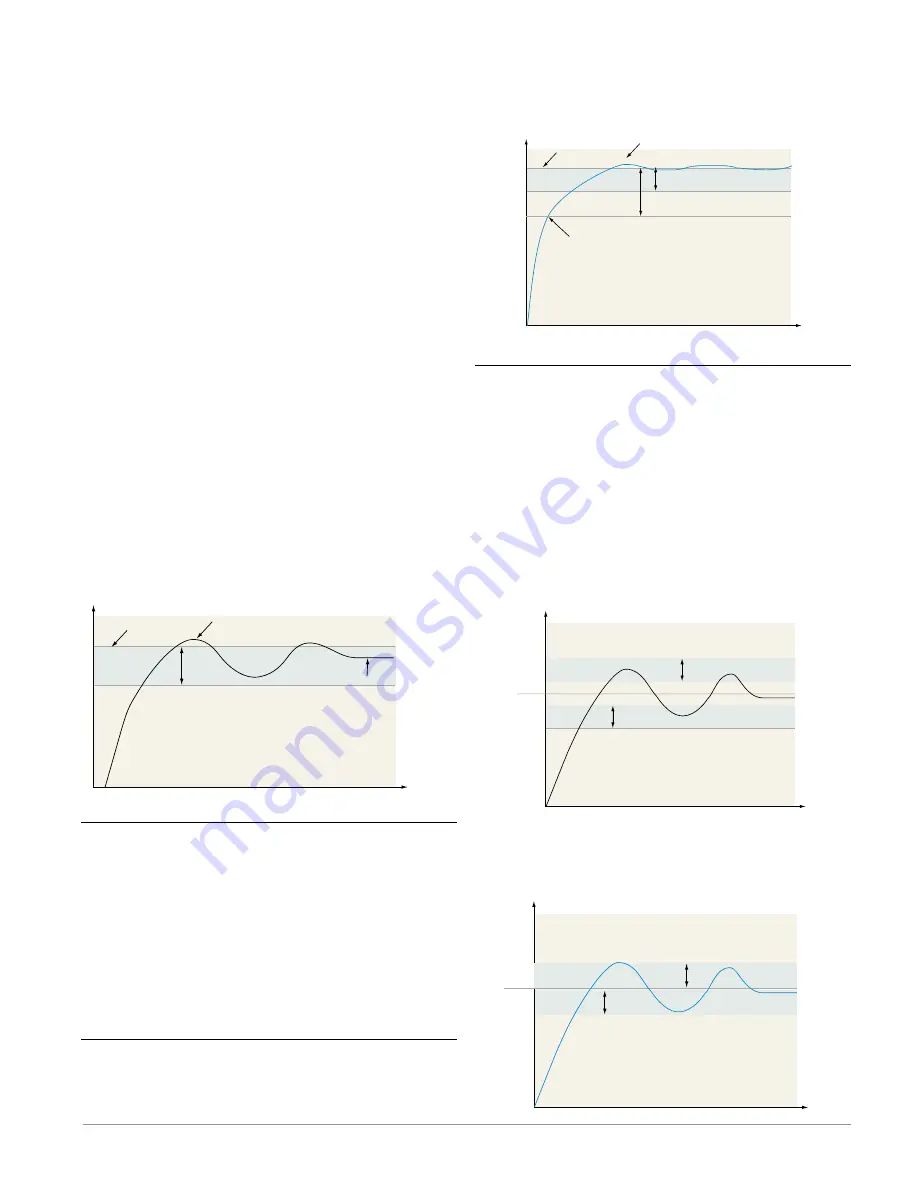
Watlow EZ-ZONE
®
RMC Module
•
155
•
Chapter 7 Features
Proportional (P) Control
Some processes need to maintain a temperature or
process value closer to the set point than on-off con-
trol can provide. Proportional control provides closer
control by adjusting the output when the temperature
or process value is within a proportional band. When
the value is in the band, the controller adjusts the
output based on how close the process value is to the
set point.
The closer the process value is to the set point, the
lower the output power. This is similar to backing
off on the gas pedal of a car as you approach a stop
sign. It keeps the temperature or process value from
swinging as widely as it would with simple on-off
control. However, when the system settles down, the
temperature or process value tends to “droop” short
of the set point.
With proportional control the output power level
equals (set point minus process value) divided by the
proportional band value.
In an application with one output assigned to
heating and another assigned to cooling, each will
have a separate proportional parameter. The heating
parameter takes effect when the process temperature
is lower than the set point, and the cooling param-
eter takes effect when the process temperature is
higher than the set point.
Adjust the proportional band with Heat Pro-
portional Band
[`h;Pb]
or Cool Proportional Band
[`C;Pb]
(Operations Page, Loop Menu).
Time
Temperature
Proportional Control
Set Point
Proportional Band
Droop
Overshoot
Proportional plus Integral (PI) Control
The droop caused by proportional control can be cor-
rected by adding integral (reset) control. When the
system settles down, the integral value is tuned
to bring the temperature or process value closer to
the set point. Integral determines the speed of the
correction, but this may increase the overshoot at
startup or when the set point is changed. Too much
integral action will make the system unstable. Adjust
the integral with Time Integral
[``ti]
(Operations
Page, Loop Menu).
Proportional, Integral and Derivative (PID) Control
Use derivative (rate) control to minimize the over-
shoot in a PI-controlled system. Derivative (rate) ad-
justs the output based on the rate of change in the
temperature or process value. Too much derivative
(rate) will make the system sluggish.
Adjust the derivative with Time Derivative
[``td]
(Operations Page, Loop Menu).
Time
Temperature
PID Control
Set Point
Reduced Overshoot
Proportional Band
Proportional Band x 2
Heating Slows
Dead Band
In a PID application the dead bands above and below
the set point can save an application’s energy and
wear by maintaining process temperature within ac-
ceptable ranges. Use Dead Band to set an offset for
the proportional band. With a negative value both
the heating and cooling outputs are active when the
process value is near the set point. A positive value
prevents heating and cooling outputs from being on
at the same time.
Proportional action ceases when the process value
is within the dead band. Integral action continues to
bring the process temperature to the set point.
Time
Temperature
Positive Dead Band
Set Point
Heat Output Active
Cool Output Active
When the
dead band value is zero
, the heat-
ing output activates when the temperature drops be-
low the set point, and the cooling output switches on
when the temperature exceeds the set point.
Time
Temperature
Zero Dead Band
Set Point
Heat Output Active
Cool Output Active