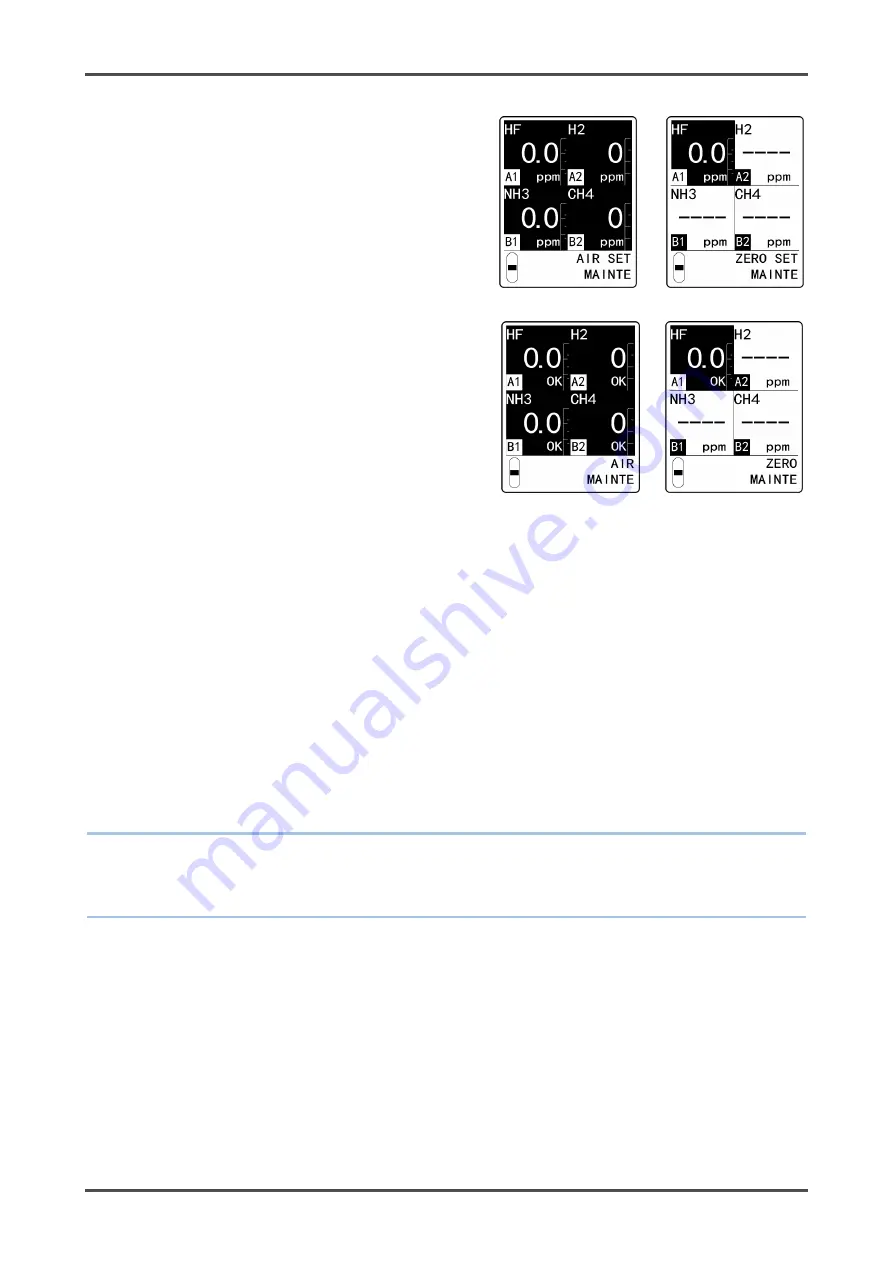
5. Usage Instructions
5-5 Performing air calibration (AIR)
56 / 191
5 Introduce the air calibration gas. Press the
TEST/SET key when the readings stabilize.
Air calibration starts.
6 Check the air calibration results.
If air calibration is successful
[OK] is displayed. The display returns to the
display in step 2.
If air calibration failed
[NG] is displayed. The display returns to the
display in step 2.
7 Disconnect the calibration gas from this product.
When air calibration is complete, disconnect the gas sampling bag for air calibration and the gas
sampling bag for the exhaust gas. (Refer to ‘7-5-4 Disconnecting the calibration gas'.)
After performing air calibration for each sensor, return the chamber switching unit to the [D] (detection
mode) position.
8 Press the MODE key.
The display reverts to the [1- 1 AIR] display.
9 Hold down the MODE key for about three seconds to switch to detection mode.
NOTE
The information displayed in the maintenance display section during air calibration will depend on
the sensor selected.
When all are selected
When [A1] is selected
When all are selected
When [A1] is selected
Содержание GD-84D-EX Series
Страница 192: ...Revision History Issue Revision details Issue date 0 First issue PT2 3041 12 20 2022 ...
Страница 193: ......
Страница 194: ......