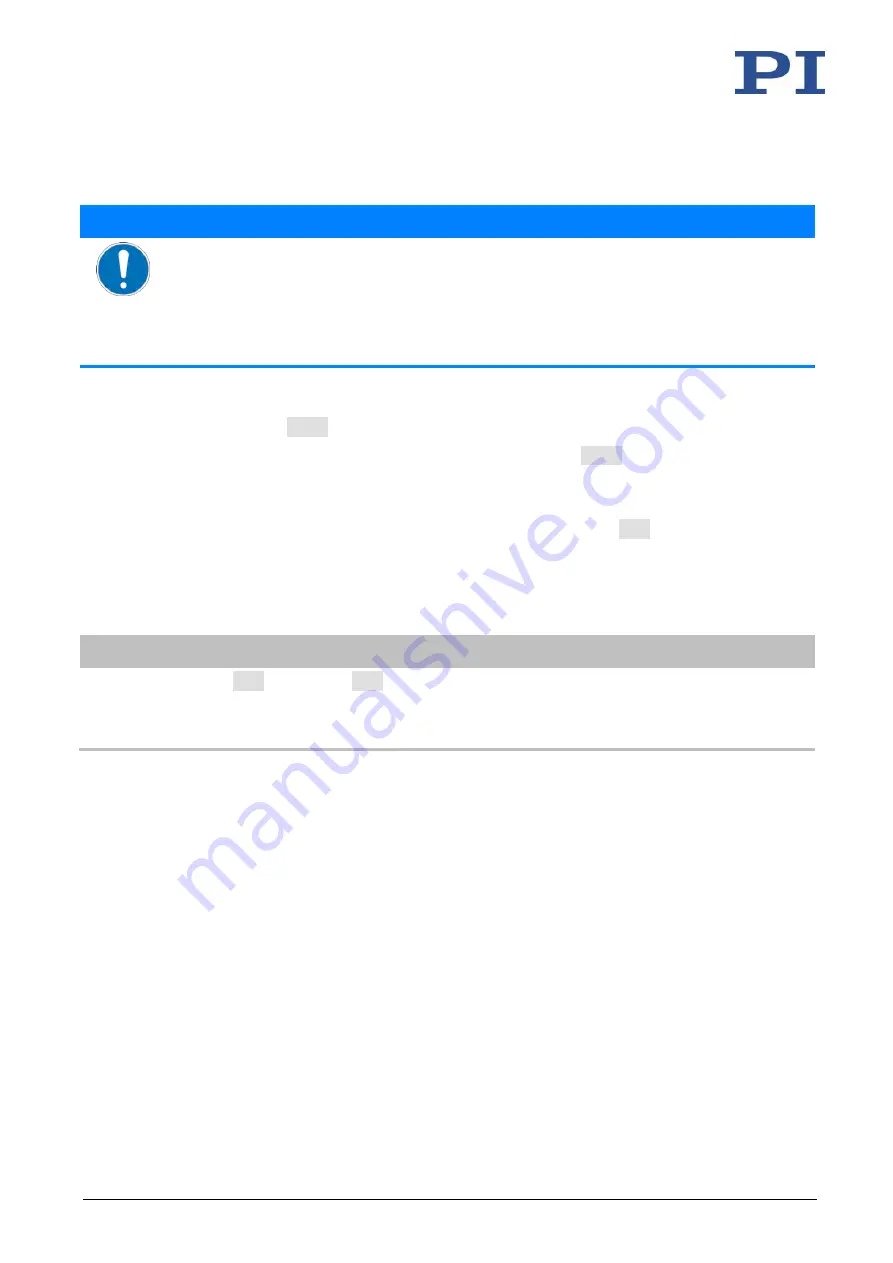
7 Operation
74
Version: 1.2.1
MS249E
C-863.12 Mercury Controller
7.1.2
Re-establishing Readiness for Operation
NOTICE
Unintentional motion after brake deactivated!
If servo mode is switched off, e.g., after a motion error occurs, the brake of the positioner can
be deactivated by command. Deactivating the brake can cause the positioner to move
unintentionally.
➢
Secure the positioner against moving unintentionally before you deactivate the brake by
command!
Re-establishing readiness for operation
1.
Send the
ERR?
command to read out the error code.
If there is a motion error, error code -1024 is output.
ERR?
resets the error code to
zero during the query.
2.
Check your system and make sure that all axes can be moved safely.
3.
Switch on the servo mode for the axis in question with the
SVO
command (p. 195).
When switching on the servo mode, the target position is set to the current axis
position and the brake is deactivated, if necessary. Now the axis can move again and
you can command a new target position.
INFORMATION
With the
CTO
(p. 136) and
TRO
(p. 200) commands, you can program the digital output lines
of the C-863.12 so that they are activated in the case of motion errors. The programmed
output lines remain activated until the error code is reset to 0. Refer to "Configuring the
"Motion Error" Trigger Mode" (p. 80) for details.
7.2
Data Recorder
7.2.1
Configuring the Data Recorder
The C-863.12 contains a real-time data recorder. The data recorder can record for example, the
current position of the axis.
The recorded data is stored temporarily in 4 data recorder tables with 1024 points each. Each
data recorder table contains the data of one data source.
You can configure the data recorder for example, by defining the data type to be recorded and
the data sources, and by specifying how the recording is to be started.