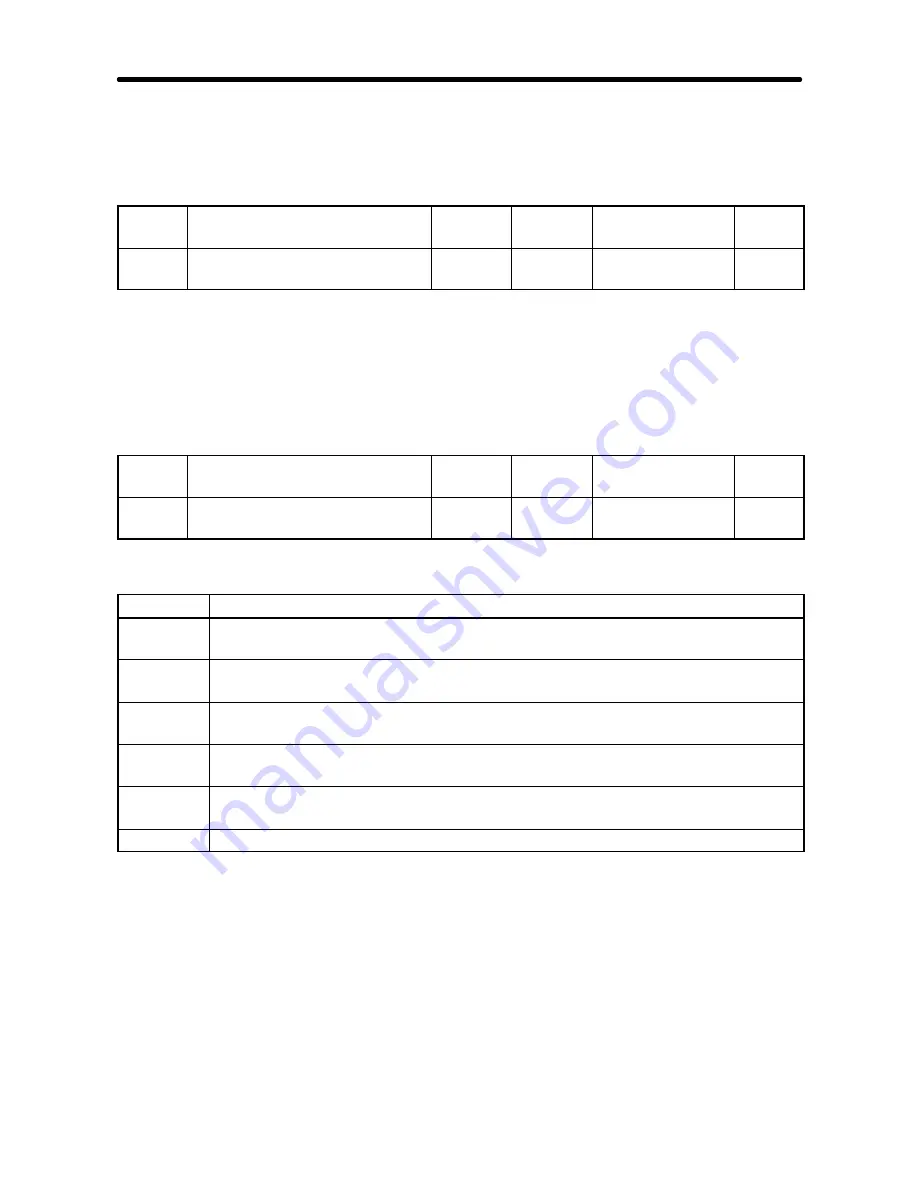
6-21
·
Set n137 to the feedback level in percentage based on the feedback level at maximum
frequency as 100%.
·
Set n138 in 0.1-s increments for the permissible continuous period of
t
he feedback sig-
nal level that is the same as or less than the feedback level set in n137.
n163
PID Output Gain
Register
01A3
Hex
Changes during
operation
No
Setting
range
0.0 to 25.0
Unit of
setting
0.1
Default setting
1.0
Set Values
·
Set this parameter to a rate by which PID control value is multiplied for PID control.
·
Normally, the default setting does not need to be changed.
·
This parameter is used for the adjustment of the PID control value to be added with the
frequency reference.
n164
PID Feedback Input Block
Selection
Register
01A4
Hex
Changes during
operation
No
Setting
range
0 to 5
Unit of
setting
1
Default setting
0
Set Values
Value
Description
0
Frequency reference control terminal for 0- to 10-V voltage input is enabled.
(see note 1)
1
Frequency reference control terminal for 4- to 20-mA current input is enabled.
(see note 2)
2
Frequency reference control terminal for 0- to 20-mA current input is enabled.
(see note 2)
3
Multi-function analog voltage (0- to 10-V) input is enabled.
Used only if two analog inputs are required in PID control.
4
Multi-function analog current (4- to 20-mA) input is enabled.
Used only if two analog inputs are required in PID control.
5
Pulse train reference control terminal is enabled. (see note 3)
Note 1.
The maximum frequency (FMAX) is reached with 10-V input.
Note 2.
The maximum frequency (FMAX) is reached with 20-mA input, if the SW2 on
the control PCB was changed from V (voltage) to I (current).
Note 3.
Set n149 for the pulse train input scale to the pulse train frequency that is equiv-
alent to the maximum frequency (FMAX).
Note 4.
Make sure that the target value input and feedback value input do not overlap
with each other.
Advanced Operation
Chapter 6
Содержание SYSDRIVE 3G3MV A2002
Страница 1: ...USER S MANUAL SYSDRIVE 3G3MV Multi function Compact Inverter Cat No I527 E2 02...
Страница 15: ...Chapter 1 Overview 1 1 Function 1 2 Nomenclature 1 3 New Features 1...
Страница 24: ...Chapter 2 Design 2 1 Installation 2 2 Wiring 2...
Страница 69: ...Chapter 3 Preparing for Operation and Monitoring 3 1 Nomenclature 3 2 Parameter Copy and Verify Function 3...
Страница 89: ...Chapter 4 Test Run 4 1 Procedure for Test Run 4 2 Operation Example 4...
Страница 286: ...Chapter 9 Specifications 9 1 Inverter Specifications 9 2 Option Specifications 9...
Страница 296: ...9 11 D 3G3MV PFI1040 E Three 5 dia holes Four M4 holes for Inverter mounting use Specifications Chapter 9...
Страница 298: ...9 13 D 3G3MV PFI2030 E Four M4 holes for Inverter mounting use Three 5 dia holes Specifications Chapter 9...
Страница 299: ...9 14 D 3G3MV PFI2050 E Four M5 holes for Inverter mounting use Three 6 dia holes Specifications Chapter 9...
Страница 301: ...9 16 D 3G3MV PRS3030V Four M5 holes for Inverter mounting use Three 6 dia holes Specifications Chapter 9...
Страница 311: ...Chapter 10 List of Parameters 10...
Страница 342: ...Chapter 11 Using the Inverter for a Motor 11...
Страница 348: ...Appendix A Standard Models...