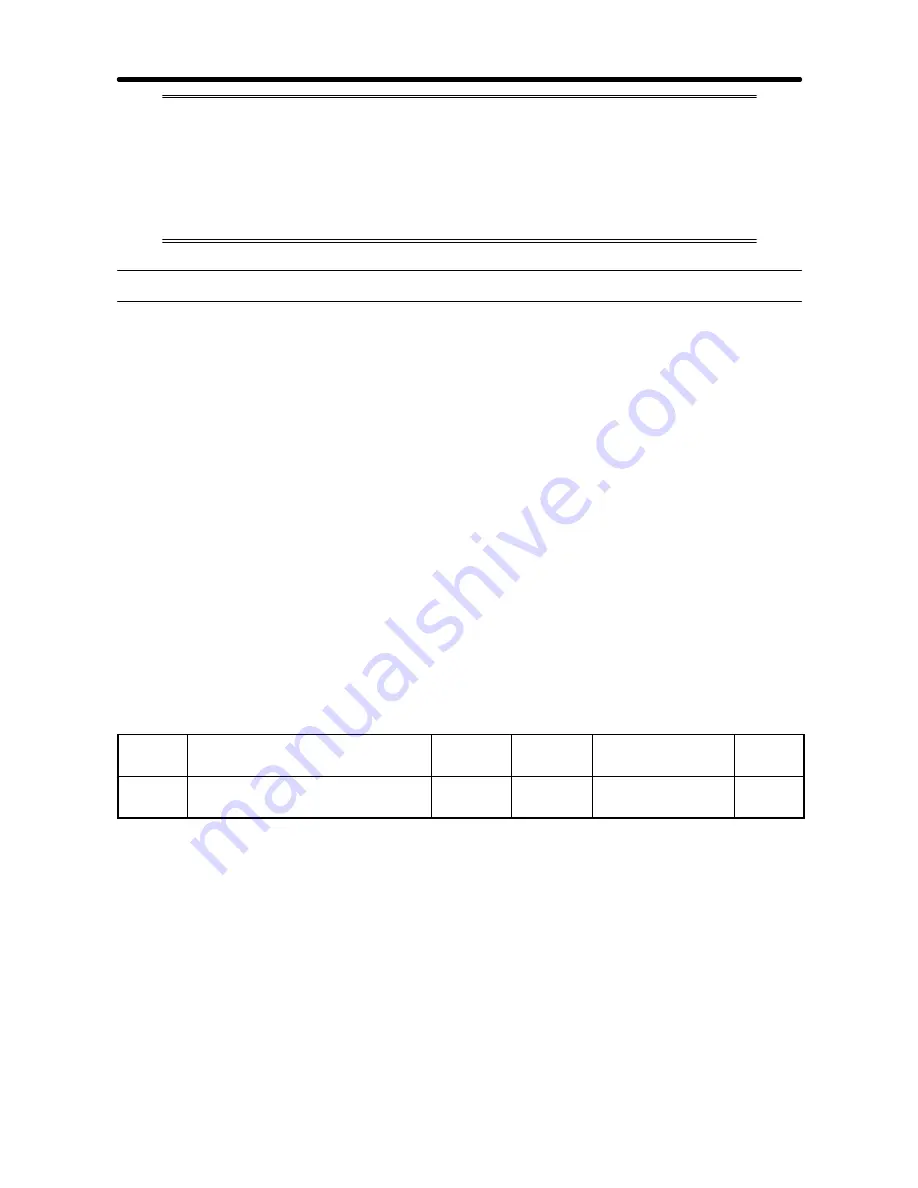
6-2
This chapter provides information on the use of advanced functions of the
Inverter for operation.
Refer to this chapter to use the various advanced functions, such as pre-
cise vector control setting, energy-saving control, PID control, carrier fre-
quency setting, DC injection braking, stall prevention, overtorque detec-
tion, torque compensation, and slip compensation.
6-1 Precise Vector Control Settings and Adjustments
6-1-1 Precise Vector Control Settings
·
In addition to the settings described in
5-2 Operation in Vector Control
, check the motor
test report and precise motor constants and make the following settings in order to
make full use of the Inverter in vector control.
H
Setting the Motor Phase to neutral Resistance (n107)
·
Set this parameter to 1/2 of the phase-to-phase resistance of the motor, or phase to
neutral resistance at 50
°
C.
·
Obtain from the manufacturer of each motor the test report of the motor or equivalent
datasheet including precise specifications of the motor. Use the the applicable formula
from those listed in the following and calculate the phase to neutral resistance at 50
°
C
from the insulation class and phase-to-phase resistance of the motor described in the
test report.
Insulation class E: Phase-to-phase resistance at 75
°
C (
W
) x 0.92 x 1/2
Insulation class B: Phase-to-phase resistance at 75
°
C (
W
) x 0.92 x 1/2
Insulation class F: Phase-to-phase resistance at 115
°
C (
W
) x 0.87 x 1/2
n107
Motor Phase to neutral
Resistance
Register
016B
Hex
Changes during
operation
No
Setting
range
0.000 to 65.50 (
W
)
Unit of
setting
See note
1
Default setting
See
note 2
Note 1.
The value will be set in 0.001-
W
increments if the resistance is less than 10
W
and 0.01-
W
increments if the resistance is 10
W
or over.
Note 2.
The default setting for this parameter is the standard phase to neutral resis-
tance of the maximum applicable motor.
H
Setting the Motor Leakage Inductance (n108)
·
Set the motor leakage inductance in 1-mH increments.
·
Motor leakage inductance is a magnetic field that is leaking externally or consumed as
core loss, and is not used for torque generation.
Advanced Operation
Chapter 6
Содержание SYSDRIVE 3G3MV A2002
Страница 1: ...USER S MANUAL SYSDRIVE 3G3MV Multi function Compact Inverter Cat No I527 E2 02...
Страница 15: ...Chapter 1 Overview 1 1 Function 1 2 Nomenclature 1 3 New Features 1...
Страница 24: ...Chapter 2 Design 2 1 Installation 2 2 Wiring 2...
Страница 69: ...Chapter 3 Preparing for Operation and Monitoring 3 1 Nomenclature 3 2 Parameter Copy and Verify Function 3...
Страница 89: ...Chapter 4 Test Run 4 1 Procedure for Test Run 4 2 Operation Example 4...
Страница 286: ...Chapter 9 Specifications 9 1 Inverter Specifications 9 2 Option Specifications 9...
Страница 296: ...9 11 D 3G3MV PFI1040 E Three 5 dia holes Four M4 holes for Inverter mounting use Specifications Chapter 9...
Страница 298: ...9 13 D 3G3MV PFI2030 E Four M4 holes for Inverter mounting use Three 5 dia holes Specifications Chapter 9...
Страница 299: ...9 14 D 3G3MV PFI2050 E Four M5 holes for Inverter mounting use Three 6 dia holes Specifications Chapter 9...
Страница 301: ...9 16 D 3G3MV PRS3030V Four M5 holes for Inverter mounting use Three 6 dia holes Specifications Chapter 9...
Страница 311: ...Chapter 10 List of Parameters 10...
Страница 342: ...Chapter 11 Using the Inverter for a Motor 11...
Страница 348: ...Appendix A Standard Models...