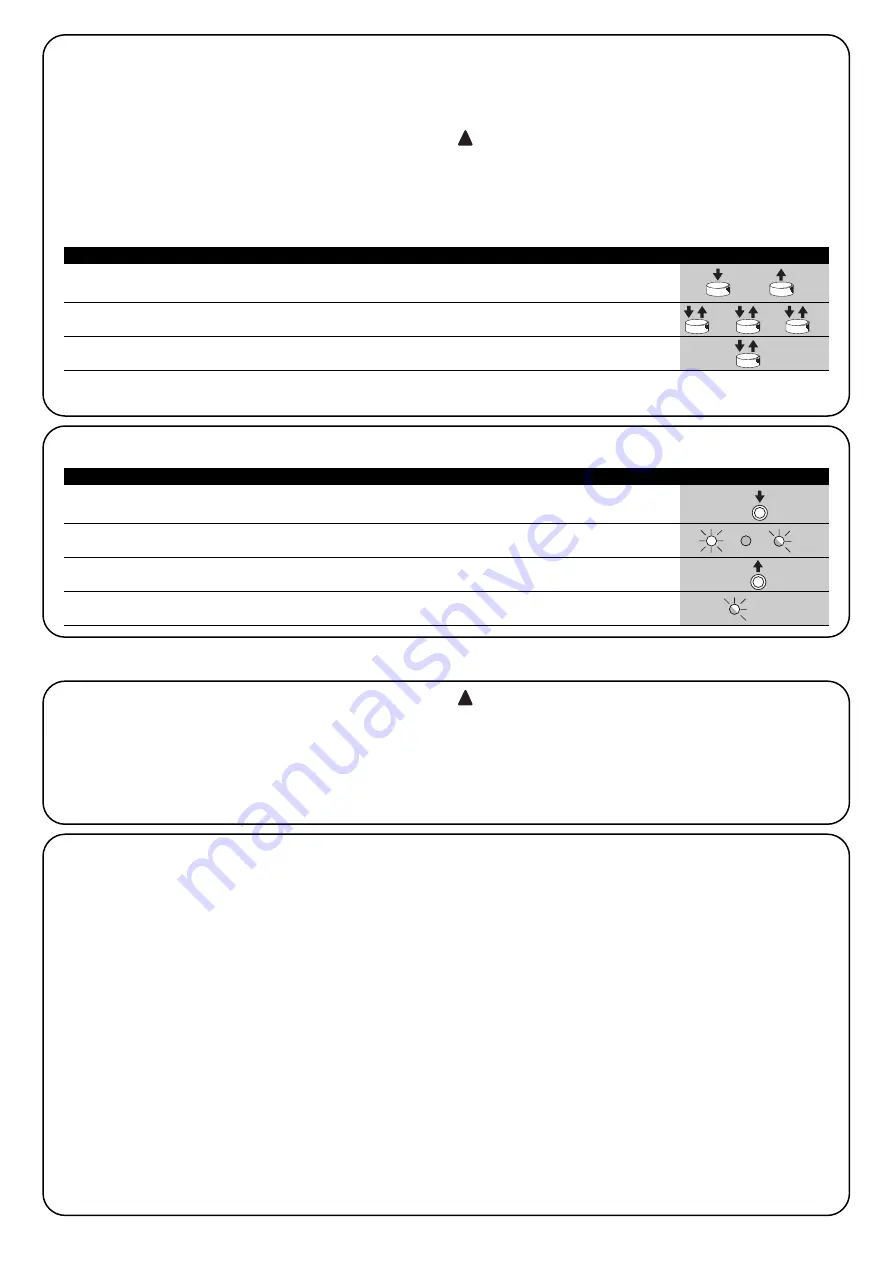
14
1.
Press the key on the new radio transmitter and hold it down for at least 5s, then release it.
5s
2.
Press the key on the previously memorized transmitter slowly 3 times.
1s
1s
1s
3.
Press the key on the new radio transmitter once slowly.
1s
At this point the new radio transmitter will be recognized by the receiver and will assume the characteristics of the previously memorized
one. If there are other transmitters to be memorized, repeat all the steps above for each new transmitter.
Table 13: for the “Remote” memorization of a transmitter
Example
4.5.4) “Remote” memorization
A new radio transmitter can be memorized without directly operating
the keys on the receiver. You need to have a pre-memorized opera-
tional radio transmitter. The “new” radio transmitter will inherit the char-
acteristics of the old one, i.e. if the old radio transmitter was memo-
rized in Mode 1, the new one will also be memorized in Mode 1. In this
case, during the memorization stage you can press any key on the
transmitters. If, on the other hand, the old transmitter was memorized
in Mode II, the new one will also be memorized in Mode II: you must
press the key on the old transmitter which corresponds to the
desired command, and the key on the new transmitter to which you
wish to associate that command.
Programming via radio may be done on all the receivers
within the range of the transmitter; therefore, only the one
involved in the operation should be kept switched on.
!
Holding the two transmitters, position yourself within the operating range of the automation and perform the following operations:
1.
Press the radio key on the control unit and hold it down
2.
Wait until the radio LED lights up, then wait until it goes off, then wait until it has flashed 3 times
x3
3.
Release the radio key precisely upon the third flash.
4.
If the procedure is successful, after a few moments the LED will flash 5 times.
x5
Table 14: to delete all the radio transmitters
Example
4.5.5) Deleting the Radio Transmitters
This is the most important stage in the automation system installa-
tion procedure in order to ensure the maximum safety levels.
Testing can also be adopted as a method of periodically checking
that all the various devices in the system are functioning correctly.
Testing of the entire system must be performed by qual-
ified and experienced personnel who must establish which
tests to conduct on the basis of the risks involved, and ver-
ify the compliance of the system with applicable regula-
tions, legislation and standards, in particular with all the
provisions of EN standard 12445 which establishes the test
methods for automation systems for gates and doors.
!
5) Testing and commissioning
5.1) Testing
Each component of the system, e.g. safety edges, photocells, emer-
gency stop, etc. requires a specific testing phase. We therefore rec-
ommend observing the procedures shown in the relative instruction
manuals.
To test SPIN proceed as follows:
1. Make sure that the provisions contained in chapter 1 «WARN-
INGS» have been carefully observed.
2. Release the door by pulling the release cord downwards. Check
that the door can be manually manoeuvred with a force no
greater than 225N.
3. Engage the carriage again.
4. Using the selector switch or the radio transmitter, test the open-
ing and closing of the door and make sure that the door moves
in the intended direction.
5. The test should be carried out a number of times to make sure
that the gate moves smoothly, that there are no points of exces-
sive friction and that there are no defects in the assembly or
adjustments.
6. Check the proper operation of all the safety devices, one by one
(photocells, sensitive edges, etc.).
In particular, each time a device is activated the “OK” LED on the
control unit flashes 2 times quickly, confirming that the control unit
recognizes the event.
7. To check the photocells and make sure that there is no interfer-
ence with other devices, pass a 5 cm diameter, 30 cm long cylin-
der on the optical axis, first near TX, then near RX and finally at
the mid-point between them and make sure that in all these cas-
es the device is triggered, switching from the active to the alarm
status and vice-versa; finally, that it causes the intended action in
the control unit; for example that it causes the reversal of the
movement during the closing manoeuvre.
8. If the dangerous situations caused by the movement of the door
have been safeguarded by limiting the force impact, the user
must measure the impact force according to EN Standard 12445.
If the adjustment of the “speed” and control of the “motor force”
are used to assist the system for the reduction of the impact
force, try to find the adjustment that gives the best results