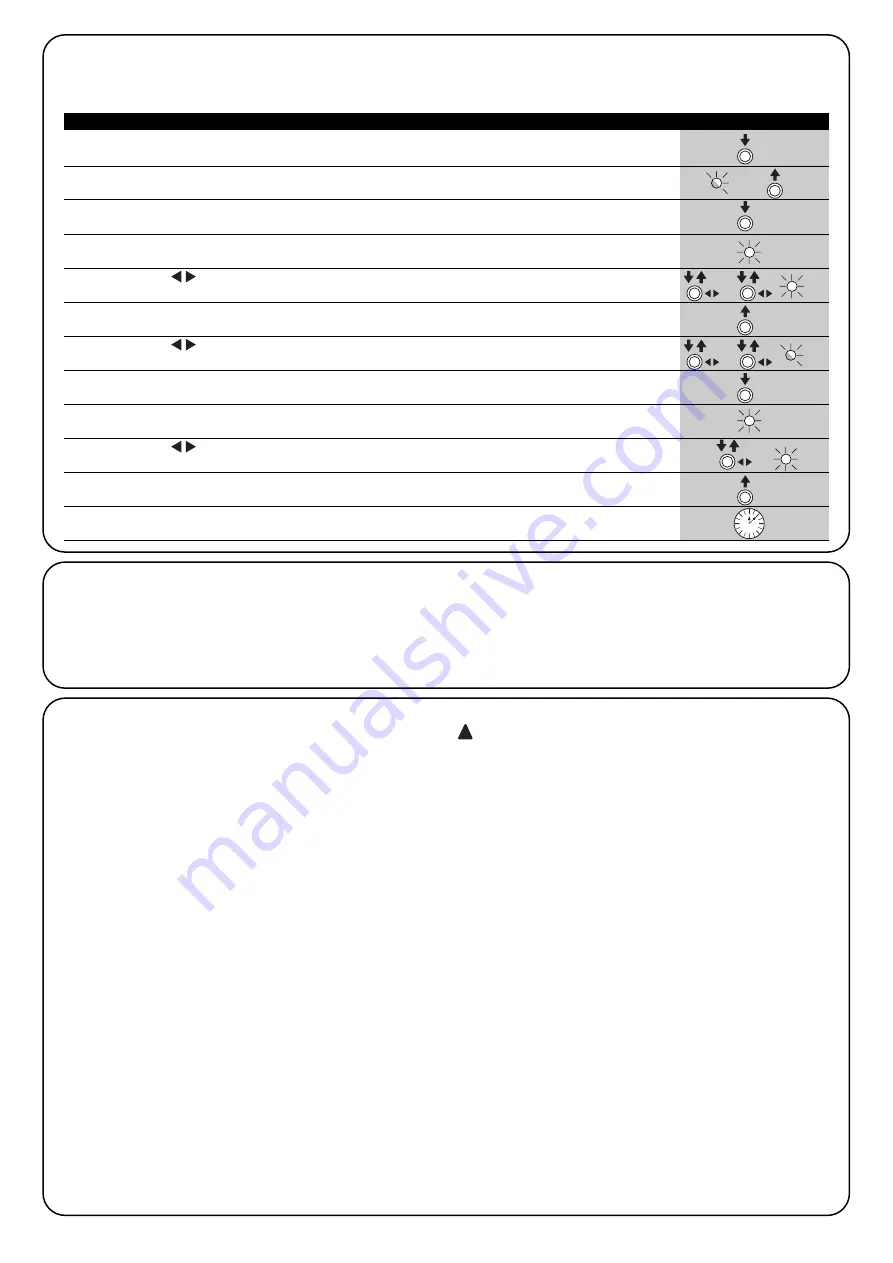
18
7.2.6) Level two programming example (adjustable parameters)
The sequence to follow in order to change the factory settings of the parameters and adjust the average “Motor force” (input on L1 and lev-
el on L2) and increase the “Pause time” to 60” (input on L3 and level on L3), is as follows.
1.
Press the key
[Set]
and hold it down (approx. 3 s)
3s
2.
Release the
[Set]
key when L1 LED starts flashing
L1
3.
Press the key
[Set]
and hold it down during step 4 and 5
4.
Wait approx. 3 seconds, after which the LED L3 representing the current level of the “Motor Force”
will light up
L3
3s
5.
Press the
[
]
key twice to move the LED which is lit on to LED L2 which represents the new
“Motor Force” value
L2
6.
Release the key
[Set]
7.
Press the
[
]
key twice to move the flashing LED to LED L3
L3
8.
Press the key
[Set]
and hold it down during step 9 and 10
9.
Wait approx. 3 seconds, after which the LED L2 representing the current level of the “Pause Time”
will light up
L2
3s
10.
Press the
[
]
key once to move the LED which is lit on to LED L3 which represents
the new “Pause Time” value
L3
11.
Release the key
[Set]
12.
Wait 10 seconds before leaving the program to allow the maximum time to lapse.
10s
Table 20: Level two programming example
Example
SET
SET
SET
SET
SET
SET
7.3) Adding or Removing Devices
Devices can be added to or removed from the SPIN automation sys-
tem at any time. In particular, various devices types can be connect-
ed to the “STOP” input as explained in paragraph “7.3.1 STOP
Input”.
7.3.1) STOP Input
STOP is the input that causes the immediate interruption of the
manoeuvre (with a short reverse run). Devices with output featuring
normally open “NO” contacts and devices with normally closed
“NC” contacts, as well as devices with 8,2K
Ω
constant resistance
output, like sensitive edges, can be connected to this input.
During the recognition stage the control unit recognizes the type of
device connected to the STOP input (see paragraph “4.2 Recogni-
tion of the door opening and closing positions”); subsequently it
commands a STOP whenever a change occurs in the recognized
status.
Multiple devices, even of different type, can be connected to the
STOP input if suitable arrangements are made.
• Any number of NO devices can be connected to each other in par-
allel.
• Any number of NC devices can be connected to each other in
series.
• More devices with 8.2K
Ω
constant resistance can be connected
in “cascade” with a single 8.2K
Ω
termination resistance
• The NO and NC combination can be obtained by placing the two
contacts in parallel, and placing in series to the NC contact an
8.2K
Ω
resistance (therefore, the combination of 3 devices is also
possible: NO, NC and 8,2K
Ω
).
if the STOP input is used to connect devices with safe-
ty functions, only the devices with 8,2K
Ω
constant resis-
tance output guarantee the fail-safe category 3 according
to EN standard 954-1.
!