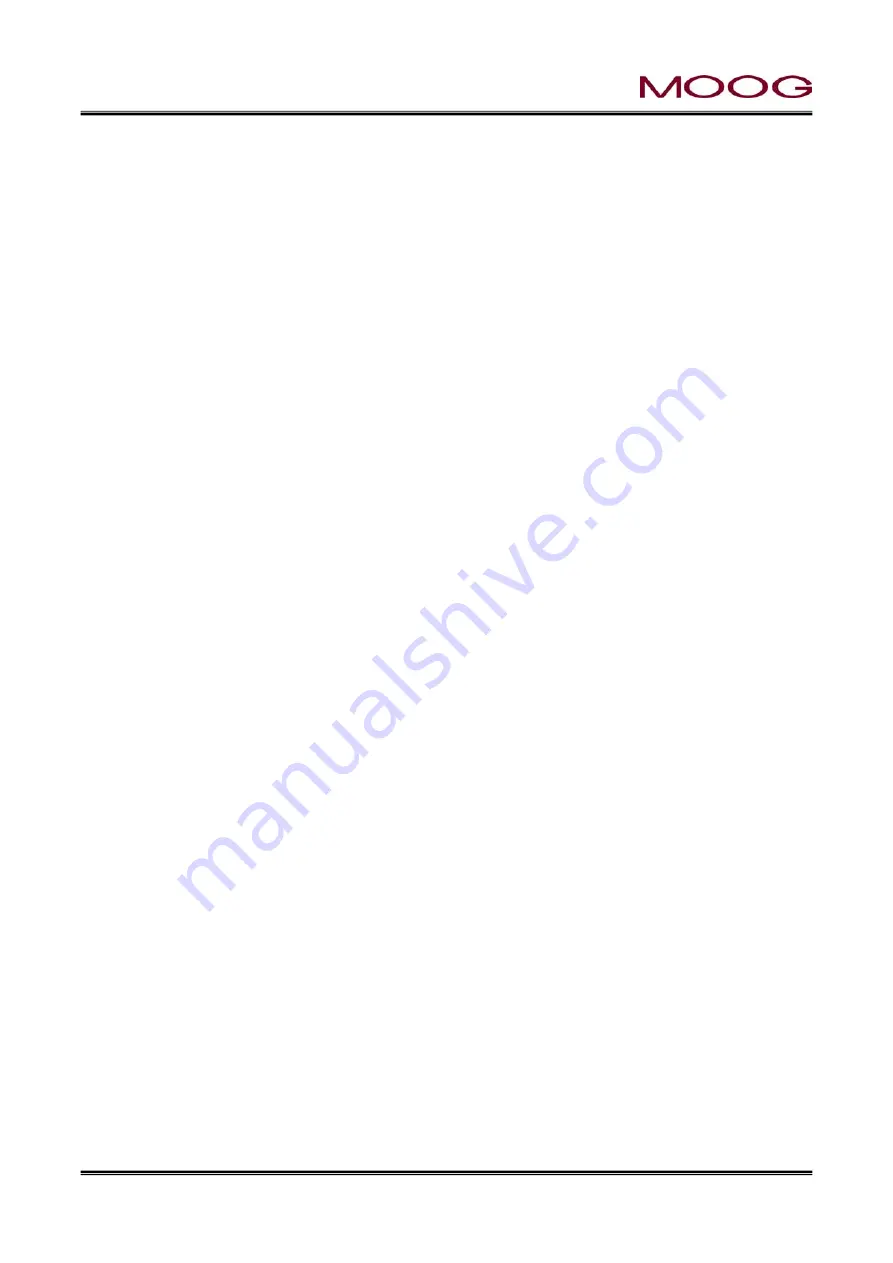
© MOOG 2010
This document is subject to MOOG INTELLECTUAL AND PROPRIETARY INFORMATION LEGEND . The details are on page II.
43
MRJ04410
DigiPackⅡ Manual, User
2-2.
PARISON CONTROL
2-2-1.
HISTORY
Many different products are produced by the Blow Molding process. Any food, drug or toy store is filled with
items using blow molded products. Many automobiles use blow molded windshield cleaning fluid. From a
small beginning many years ago, the blow molding process has grown to a major industry.
The value of parison wall thickness control was recognized when the industry was young. Some of the early
machines used two position hydraulic control of the die-mandrel gap. Others used heavy cams in strong
structures to withstand the large forces involved. The first electro-hydraulic blow molding system replaced
the heavy cams with light cams that were easy to modify. This was quickly followed by a readily adjustable
electronic master cam used to determine the correct cam shape. Electronic interpolation then eliminated
the cam. Today’s parison programming systems provide reliable programming of parison wall thickness and
in addition, may provide control of mold motion; screw speed; injection barrel heater temperatures, etc. or
the capability to control all machine functions.
2-2-2.
PARISON PROGRAMMING BENEFITS
Parison programming provides improved container quality, higher production rates and increased profits.
Control of parison wall thickness as a function of parison length results in constant container wall thickness
after the parison is blown to conform to the mold.
Quality tests determine the ability of a container to withstand drop tests without bursting or leakage of its
contents. Parison programming provides constant wall thickness throughout the container, insuring im-
proved mechanical endurance at minimum weight.
Container wall thickness control reduces the container weight, eliminates the hot spots, resulting in de-
creased parison cooling time. The parison programmed blow molding machine’s shorter cycle time results
in increased production rates, combining with the decrease in material cost to ensure higher profits.
2-2-3.
CONTINUOUS EXTRUSION MACHINES
A continuously rotating extruder screw pressurizes the granular plastic material, driving it through a heated
tubular barrel. The resulting molten plastic is then extruded through the mandrel die gap, forming a con-
tinuous tubular parison.
As the parison never stops being formed, multiple molds are required to receive the parison in turn. One
mold is in the cooling position, where the plastic cools until the container can stand alone when the mold is
opened. The open mold has been moved to a position surrounding the parison, and when the parison is long
enough, the mold is closed. The parison is then pressurized with air through the blow pin, causing it to