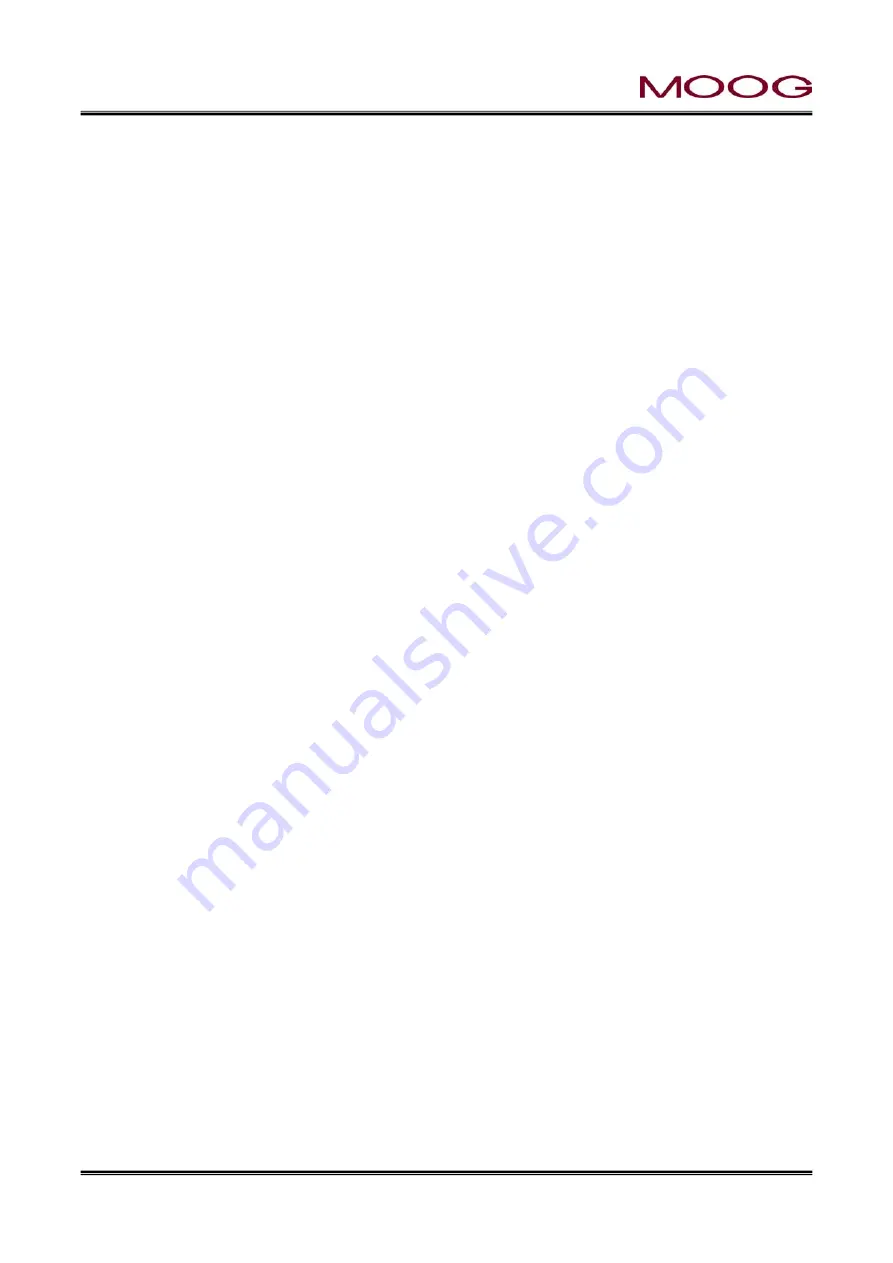
© MOOG 2010
This document is subject to MOOG INTELLECTUAL AND PROPRIETARY INFORMATION LEGEND . The details are on page II.
78
MRJ04410
DigiPackⅡ Manual, User
2-7.
SETTING UP
2-7-1.
OBJECTIVE
The container produced by the blow molding process must meet the customer’s specification. Customer’s
specifications normally involve standards for appearance, weight and physical characteristics such as
strength, endurance and dimensional accuracy.
The container design process will determine the material to be used, the shape of the mold and required
special features as well as the size and shape of the die gap tooling.
The task of the set up man is to use the above information with the DigiPackⅡto control the parison wall
thickness and placement in the mold to produce the container to its design specification.
The setup man must become familiar with the contents and definitions contained in Section 1-3 and 1-4.
2-7-2.
DIE GAP TOOLING SETUP
A feature of the DigiPackⅡis its ability to store the programmed parison wall thickness profile and other
settings required to produce a particular container. Up to 100 container files may be stored. The stored
container files in the DigiPackⅡeasily allow the change from one container to another.
The stored information for a particular container contains the closed tooling die gap position and the re-
lationship between the programmed wall thickness or die gap opening and the actual tooling die gap opening
produced by the desired wall thickness. In other words, the relationship between the programmed die gap
opening and the actual die gap opening has been calibrated. For example, a commanded die gap opening of
37% could be calibrated to cause an actual die gap opening of 6.7mm. The tooling die gap calibration in-
formation is contained in the container file.
In order to quickly change the blow molding machine production from one container to another with
minimum change over time, the tooling die gap calibration must be accurately established.
The DigiPackⅡInstallation and Maintenance Manual contains a tooling die gap calibration procedure in
Section 1-6, DIE GAP TOOLING SETUP. To achieve the minimum change over time it is essential that this
procedure be followed and the requested information recorded.