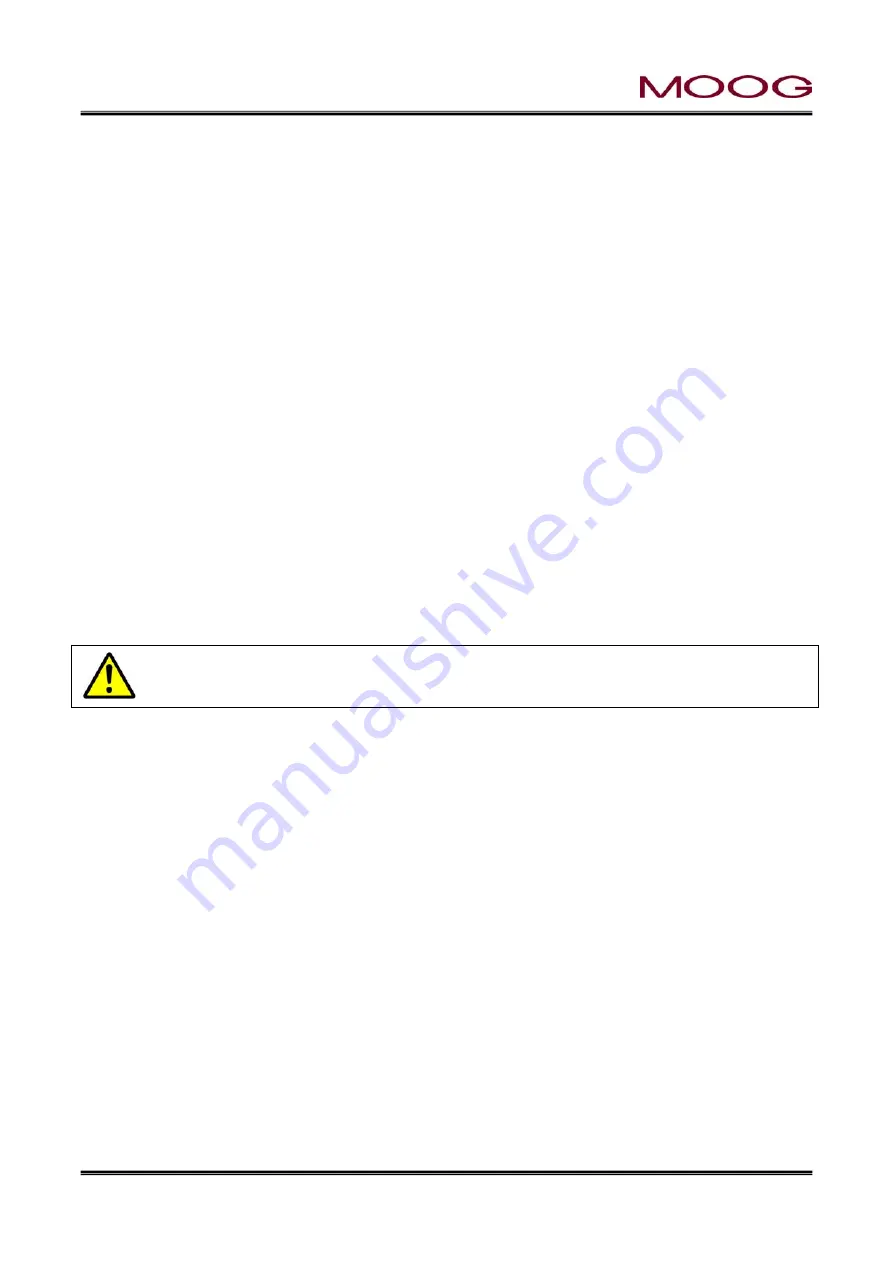
© MOOG 2010
This document is subject to MOOG INTELLECTUAL AND PROPRIETARY INFORMATION LEGEND . The details are on page II.
18
MRJ04410
DigiPackⅡ Manual, Installation and Maintenance
1-6.
ELECTRICAL INSTALLATION
1-6-1.
GENERAL
Electrical installation includes several phases of work:
A)
mounting the DigiPackⅡin a suitable location
B)
determining the correct phasing so the servovalve, tooling position transducer and, possibly,
accumulator position transducer may be connected to the DigiPackⅡ
C)
determining the blow molding machine interface interaction with the DigiPackⅡand then
wiring the machine-DigiPackⅡinterface
D)
connect the DigiPackⅡto electrical power supply from the stable 24VDC
DigiPackⅡ MOUNTING
The DigiPackⅡmust be mounted in a location free of vibration, with protection from the environment and
most important, located in a position allowing the operator and setup man easy visual and physical access.
It is recommended that the mounting be on a swing out panel allowing easy access to the front and back
sides of the DigiPackⅡ.
Mounting information is shown in “
Figure 1-17
”. Brackets providing simple panel mounting are included.
All wiring from the DigiPackⅡmust be shielded. The shield is to be grounded to the DigiPackⅡ
ground at the DigiPackⅡonly Any other ground paths may cause damage.
1-6-2.
TB-1, TB-2 WIRING
The wire size for TB-1 and TB-2 are able to use AWG26 - 14, and required using Solder less Pin type
terminal
TB-1 provides the interface between the DigiPackⅡand the servovavle, die gap sensor, accumulator po-
sition sensor. TB-1 also provides outputs to optional customer monitors MFB Valve current, EFB spool
monitor, DCDT input voltage, Accumulator voltage, Position command, these signals can be select at set-
ting display (See 2-4-8. ). A schematic of TB- 1 is shown as “
Figure 1-19
” and TB-1 functions are outlined
in the table, “
Figure 1-20
”.
Phasing definitions for the servovalve, die gap position and accumulator position (if used) transducers are
given in “
Figure 1-18
”.
Some connections to TB-1 are shown in parenthesis, (), in “
Figure 1-19
”. The parenthesis, (), indicate
alternate connection possibilities result from particular directions of motion or phasing determined during
the design of the mechanical installation. Phasing requires that a defined direction of motion of the tooling
actuator will result from TB-1-1 being negative with respect to TB-1-2; that the output voltage of the die
gap position transducer be positive or negative when the die gap is moving in a specific direction; and that
the accumulator position transducer output voltage direction be defined when the accumulator is ejecting
molten plastic into the die head. Terminal TB-2 is using the external power supply to isolate logic inputs,
“
Figure 1-22
”, TB-2 functions are outlined in “
Figure 1-23
”.