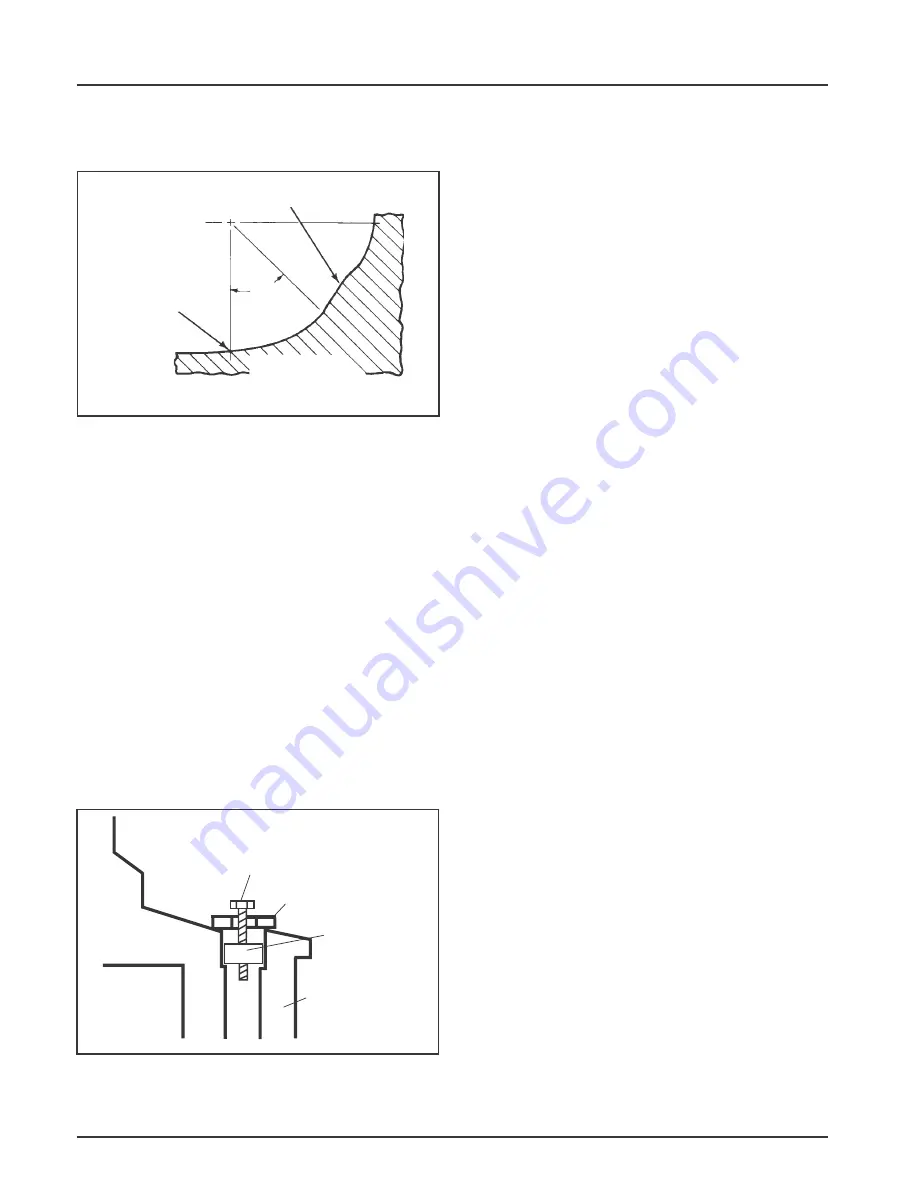
Section 9
Inspection and Reconditioning
9.2
NOTE
: If the crankpin is reground, visually check to
ensure that the fillet blends smoothly with
the crankpin surface. See Figure 9-1.
Procedure to Install New Plug:
1. Use a single cylinder camshaft pin, Kohler Part
No.
47 380 09-S
as a driver and tap the plug into
the plug bore until it seats at the bottom of the
bore. Make sure the plug is tapped in evenly to
prevent leakage.
Crankcase
Inspection and Service
Check all gasket surfaces to make sure they are free of
gasket fragments. Gasket surfaces must also be free of
deep scratches or nicks.
Inspect the main bearing (if so equipped) for wear or
damage (refer to Section 1, Specifications, Tolerances,
and Special Torque Values). Replace the bearing or
crankcase using a miniblock or short block as
required.
Check the cylinder bore for scoring. In severe cases,
unburned fuel can cause scuffing and scoring of the
cylinder wall. It washes the necessary lubricating oils
off the piston and cylinder wall. As raw fuel seeps
down the cylinder wall, the piston rings make metal
to metal contact with the wall. Scoring of the cylinder
wall can also be caused by localized hot spots
resulting from blocked cooling fins or from
inadequate or contaminated lubrication.
If the cylinder bore is badly scored, excessively worn,
tapered, or out-of-round, resizing is necessary. Use an
inside micrometer to determine the amount of wear
(refer to the Specifications, Tolerances, and Special
Torque Values, in Section 1), then select the nearest
suitable oversize of either
0.25 mm (0.010 in.)
or
0.50 mm (0.020 in.)
. Resizing to one of these oversizes
will allow usage of the available oversize piston and
ring assemblies. Initially, resize using a boring bar,
then use the following procedures for honing the
cylinder.
Honing
While most commercially available cylinder hones
can be used with either portable drills or drill
presses, the use of a low speed drill press is preferred
as it facilitates more accurate alignment of the bore in
relation to the crankshaft crossbore. Honing is best
accomplished at a drill speed of about
250 RPM
and
60 strokes
per minute. After installing coarse stones in
hone, proceed as follows:
Figure 9-1. Crankpin Fillets.
The connecting rod journal can be ground one size
under. When grinding a crankshaft, grinding stone
deposits can get caught in the oil passages, which
could cause severe engine damage. Removing the
crankpin plug when the crankshaft is ground
provides easy access for removing any grinding
deposits that may collect in the oil passages.
Use the following procedure to remove and replace
the plug.
Procedure to Remove Crankshaft Plug:
1. Drill a 3/16" hole through the plug in the
crankshaft.
2. Thread a 3/4" or 1" long self-tapping screw with
a flat washer into the drilled hole. The flat
washer must be large enough to seat against the
shoulder of the plug bore. See Figure 9-2.
Flat Washer
Self-Tapping Screw
12345678
12345678
12345678
12345678
12345678
Plug
Crankshaft
45
°
High Point from
Fillet Intersections
This Fillet Area
Must Be
Completely Smooth
Minimum
The Fillet Must
Blend Smoothly
with the Bearing
Journal Surface
Figure 9-2. Removing Crankpin Plug.
3. Tighten the self-tapping screw until it draws the
plug out of the crankshaft.