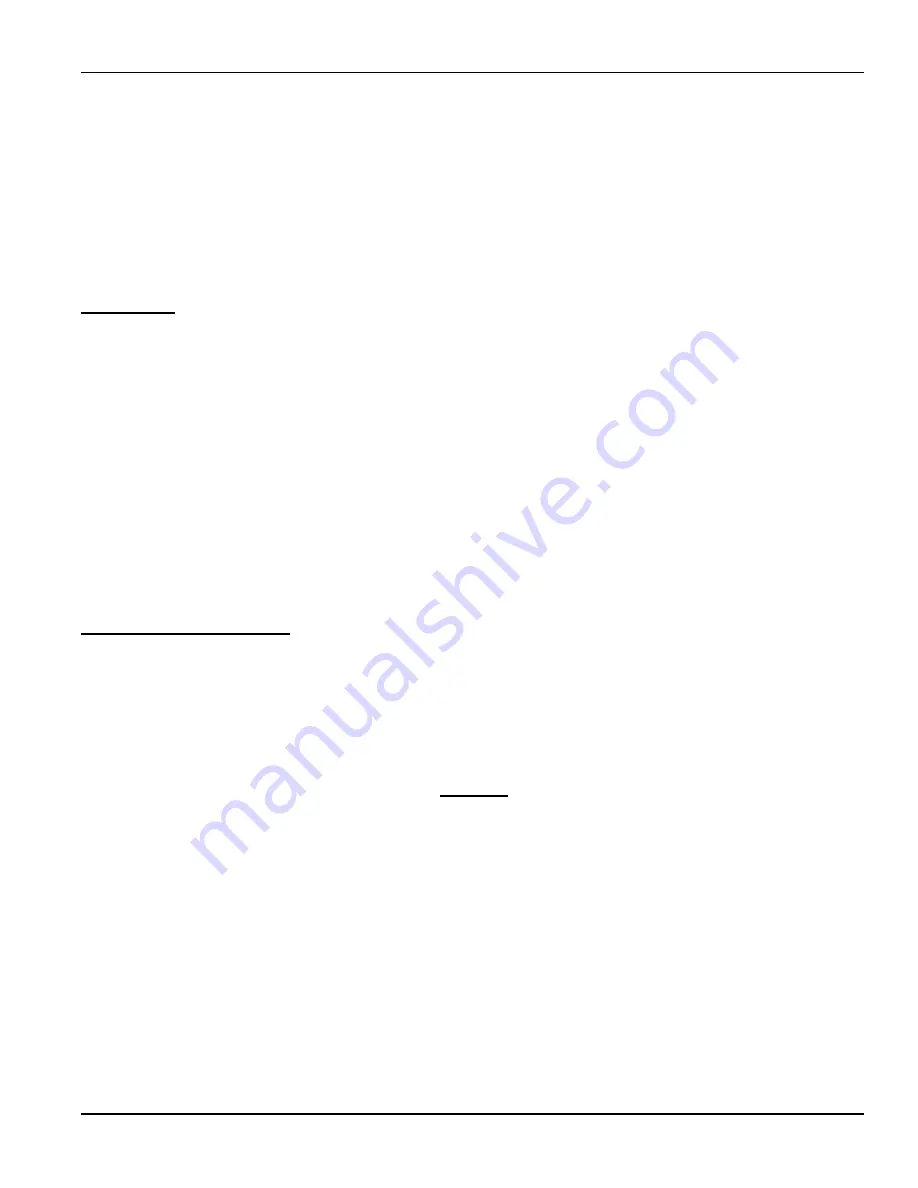
DIGISPENSE 3009 CONTROLLER MODULE, STYLE B
Page 3-99
29 October, 2019
IVEK Corp. P03R017E
19 Motor/Base Not Selected
- Serial command sent to begin motion and motor/base is not selected. (y2)
20 Command Missing
- The command string did not contain an alphabetic character. The '?' character will be
inserted in
place of the <cmd> field in the response.
21 Command String Overflow
- The length of the command string exceeded the input buffer.
22 Unexpected Character in Command String
- There was a character in the command string that was not
alphabetic,
numerical, or a field delimeter .
24 Fluidic Mode Disabled
- A Fluidic Mode operation was initiated but Fluidic Mode is disabled.
25 Invalid Permission for Command
- The permission setting is too low for the command sent.
26 Can't Start, Other Operation Active
- An operation was attempted while another operation is active.
29 Invalid Address Mode
–
The communication command string uses an address mode that is inconsistent with the
configuration for that communication channel.
3.4.11 Faults
Faults are a result of the system detecting improper operation of the Motor/Base Module. All fault numbers will be
greater than or equal to 1000. The ‘clear faults’ command must be used before any subsequent operation of the
affected channel is performed. For any faults other than 1002, 1013 and 1017, the Controller Module will have to be
returned to IVEK Technical Support if a power-cycle does not clear the fault.
1002 Motor Stall Fault
-
“Home” position sensor for rotary motion was not detected, most likely due to a stalled motor.
Clear
faults re-reference using 'c' command.
1005 Motor Module Fault
– The module that drives the motor has faulted.
1013 Non-Volatile Memory Fault
– A fault occurred while trying to access the non-volatile memory. The description
on the fault screen will provide additional information.
1014 Low Motor Voltage Fault
– The voltage to the motor module is very low, possibly a blown fuse.
1015 Motor Control Hardware Fault
-
A fault in the hardware that sets the motor current threshold was detected.
1016 Internal Operation Fault
- An internal software fault has occurred.
1017 Motion Disable during Operation
- Either the Motion Enable signal or the serial command disabling motion
occurred
during an operation.
3.4.12 Operating The System
There are several different modes of operation providing the Controller Module with its vast functional flexibility. On
initial power-up, these modes must each be sequenced in the proper order to assure proper operation.
3.4.12.1 Setup
The following steps will guide you through a basic setup for turning your system on for the first time:
CAUTION
The Motor/Base Module number selection in the Setup C screen MUST match the Motor/Base Module
attached to the Controller Module. An incorrect setting could overheat the motor and damage the equipment
and cause a hazardous condition.
1. On the rear of the Controller Module
a. Make sure the 1/0 (On/Off) switch is set to 0 (Off).
b. Connect the power cord to the Controller Module and the power source.
c. Connect the Motor Cable, the larger connector connects to the Controller Module.
2. On the Motor/Base Module
a. Connect the other end of the Motor Cable
b. Set the AP Style displacement adjust to 4.5 or
c. Set the Heavy Duty Style displacement adjust to 10