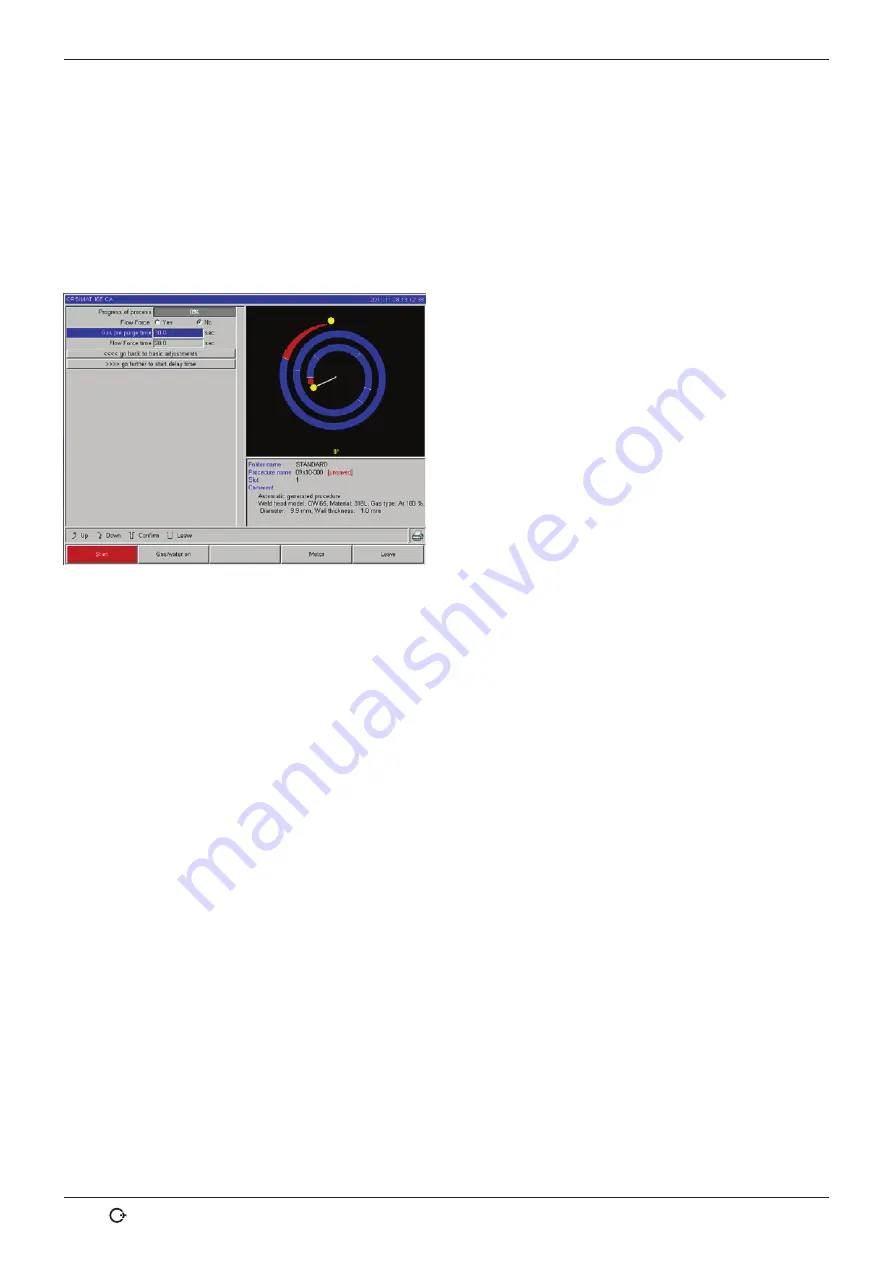
Operation
ORBIMAT CA
| Operating instructions
38
orbitalum tools
GmbH, D-78224 Singen, www.orbitalum.com, Tel. +49 (0) 77 31 792-0
(09.03.15) OW_ORBIMAT_CA_BA_871060202_04_EN
The space to be filled with gas also depends on the weld head size and pipe diameter. It may therefore be necessary to
shorten the gas pre purge time for smaller weld heads. If the seam (with closed weld heads) is bare and nearly free of
annealing colors right from the beginning, the gas pre purge time is correct. For special materials (e.g. titanium), it may
be necessary to lengthen the gas times. The gas after-flow time must at least be long enough that the material no longer
reacts to oxygen in the air when opening the closed weld heads. This also depends on the energy introduced during weld-
ing.
Cassette weld heads:
Due to electrode oxidation, do not use a gas post purge time of less than 10 seconds.
LP weld tongs:
Do not change the gas times specified by auto programming.
1. Press softkey 1 "
Weld
".
2. Using the "
go back to gas post purge time
" or "
go
further to gas pre purge time
" button, select, adjust
and save the individual parameters.
– or –
1. In the main menu, select "
Manual/Adjust program-
ming
" > "
Adjust parameters
".
2. Select, highlight, adjust and save parameters.
X
Press softkey 1 ("
Weld
") or softkey 2 ("
Test
").
The machine is ready to start.
Fig. 17:
Input field - Gas post purge time
8.3.5
Adjusting ignition current, end current and current slope-off
X
Adjust values specified by auto programming only in exceptional cases (e.g. with extremely thin-walled pipes).
Ignition current:
Value specified during ignition. The ignition current is active only very briefly and affects the ignition
behavior itself. If the ignited arc is detected, the machine switches to the current programmed on level 1 within a few
tenths of a second.
Final current:
Current level reached by the final slope-off immediately before switch-off of the arc at the end of the welding
process. The value must be greater than 0. Otherwise, the arc will cut out before the end of the welding process.
X
Ensure that the value (3 A) is not zero.
For extremely large arc gaps (LP tongs):
X
If the arc cuts out at the end of current slope-off: Increase value.
Slope-off time:
Time from the end of the last-used weld sector to the switch-off of the arc. This is identified by an in-
creasingly narrower weld seam on the welded part.
The current slope-off is necessary to prevent a final crater (formed due to immediate switch-off) from being formed.
Is a longer or shorter run-out of the weld seam desired?
X
Increase or decrease value.