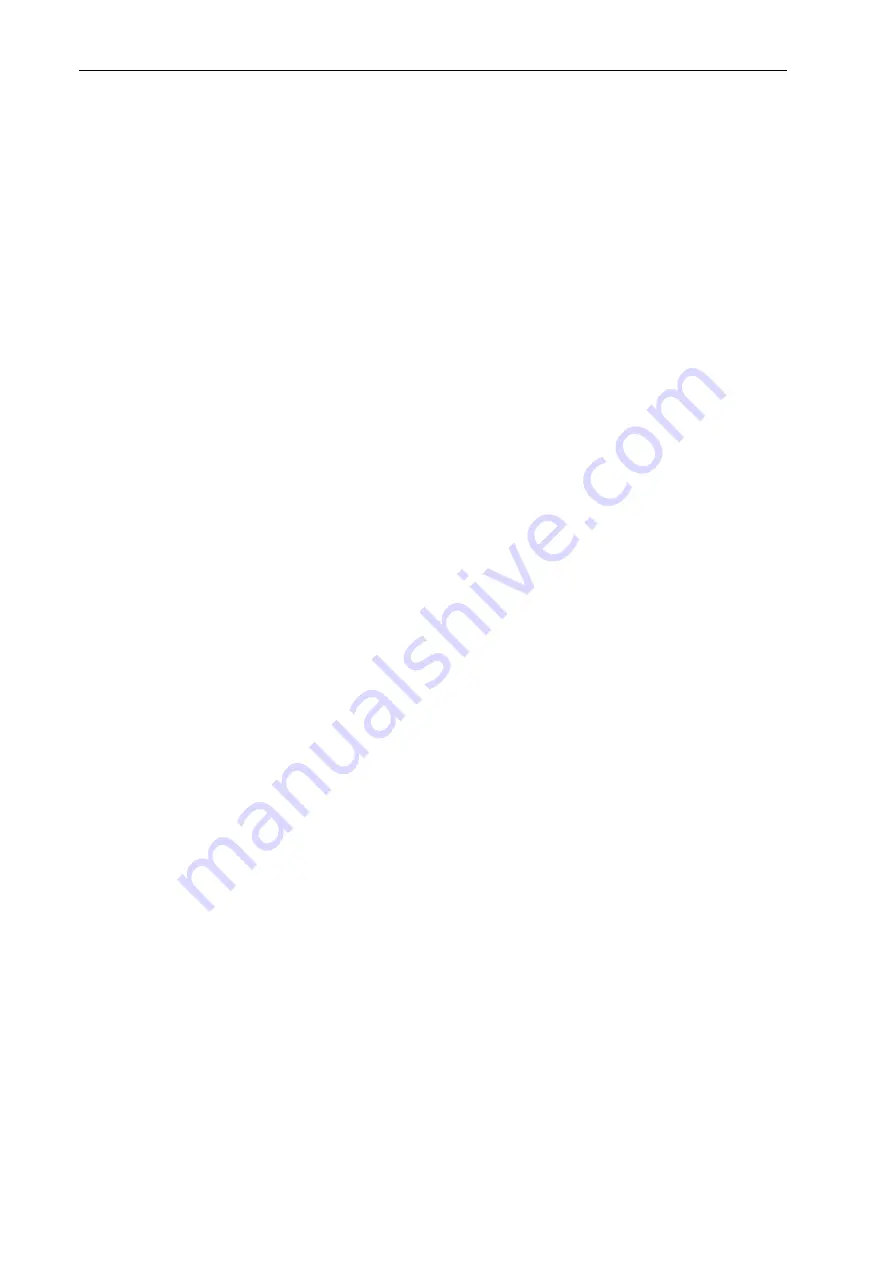
Description of the drive module
Positioning module UVE8112, IMD10
Commissioning
Overview
An essential condition for the successful commissioning is the correct pin assignment of all required
signals and connections.
The DIP switch has to be configured according to the desired mode of operation and communication
interface, before the module is switched on.
An auxiliary means for the commissioning is the supplied DCSetup programme. It contains a special
menu point allowing a step-by-step commissioning of the module.
See "Step-by-step commissioning" on page 41.
After the completion of the step-by-step commissioning, all drive- and motor-specific parameters
should be set. If additional settings have to be carried out, e.g. the configuration of different
communication parameters or device parameters which are not changed through the step-by-step
commissioning, this can also be done by means of the setting programme.
See "Object Directory dialogue box" on page 65.
Particularities as regards the commissioning of a gantry axis
In the gantry operation, two axes are synchronously controlled without a toothed belt or a bevel gear
system. One axis works as the master and the other works as the slave. In order to commission a
gantry axis, each axis (master or slave) has to be commissioned separately, before the machine is
assembled. These parameters are stored as usual in the UVE8112 module. On the basis of the
control and motion parameters of the master and slave axis, the ISEL CNC control determines the
optimum motion behaviour for the gantry axis during the initialisation phase.
By means of the CANSET programme, it can be stipulated, if an axis is in the gantry operation or not
and which axis is the master and which the slave. In case of a slave axis, the user also has to define
the maximum admissible deviation of position and the coupling factor between the master and the
slave during the gantry operation in the “Can interpolation” dialogue box. The reference point is the
start of the synchronous control. Every axis (master or slave) has its own reference switch or a limit
switch serving as reference switch. In order to compensate for the tolerance during the installation of
the switch, users may define different reference distances for the master and the slave (see
“Reference run” dialogue box).
The following settings have to be identical for the master and the slave:
- axis directions (see “Direction” dialogue box)
- axis type: Linear and Rotary Axis (see “Can interpolation” dialogue box)
- motion parameter unit µm or “...” (see “Transmission” dialogue box)
All other parameters may differ for the master and slave.
Examples for the motion control
Example 1:
Communication:
Can
Baud rate:
1 Mbit/s (RS232: 57600 baud)
Node address:
2
Mode of operation:
Velocity control with ramp profile (profile velocity mode)
26
Содержание IMD1
Страница 1: ...DC servo positioning module with CanOpen interface UVE8112 IMD10 www isel com ...
Страница 66: ...DcSetup programme Positioning module UVE8112 IMD10 66 ...
Страница 113: ...Positioning module UVE8112 IMD10 Appendix 113 Appendix UVE8112 package dimensions ...
Страница 114: ...Appendix Positioning module UVE8112 IMD10 114 IMD10 package dimensions ...