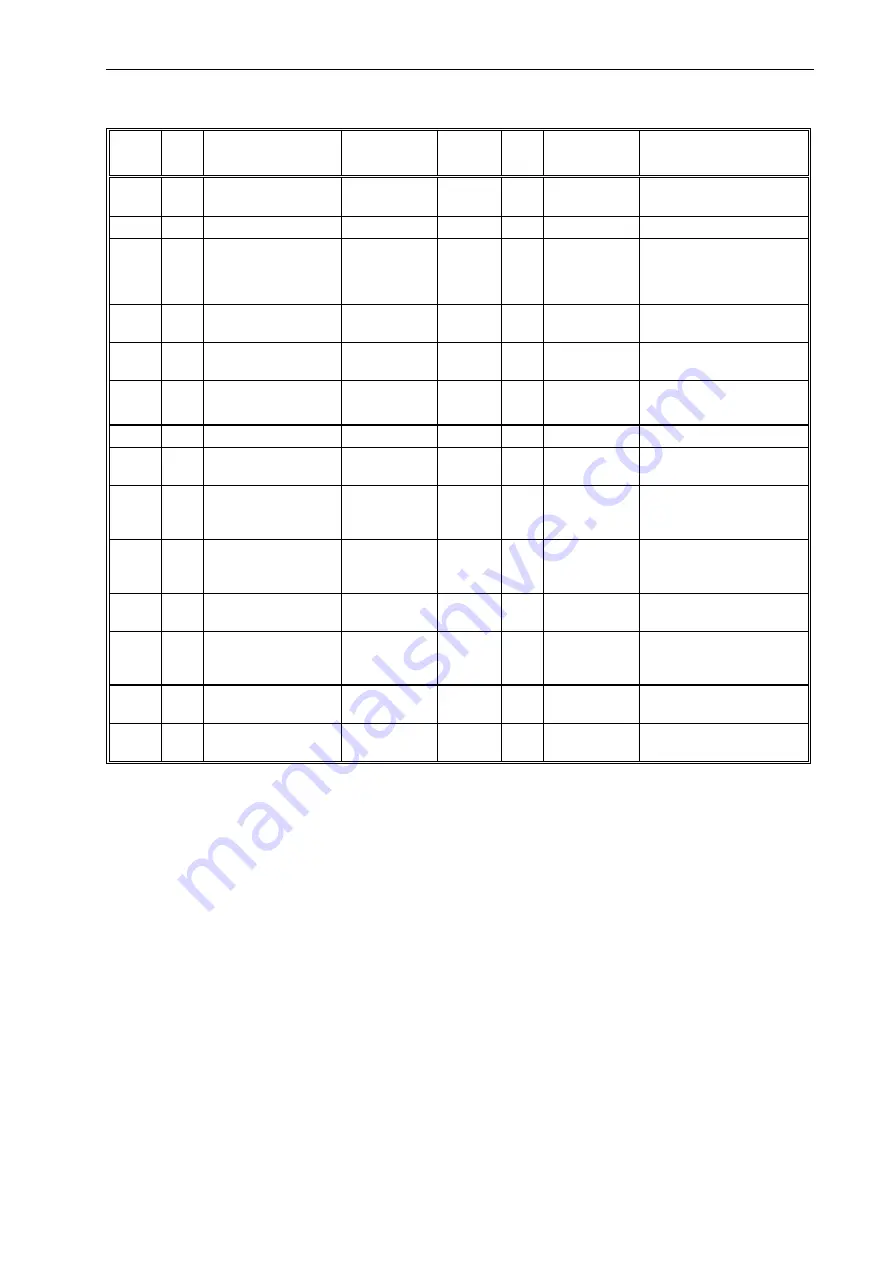
Positioning module UVE8112, IMD10 CanOpen
protocol
Synchronous control
Index Sub Name
Type
Attrib Map Default
value
Meaning
2043
Synchronous
control
RECORD
Control of the gantry axis
.
2043
00
Number of entries
Unsigned 8
CONST
N
3
Number of entries.
2043
01
Synchronous mode
Unsigned 8
RW
N
0
0
Æ
No gantry axis
1
Æ
Slave axis
2
Æ
Master axis
2043 02 Slave minimal node
ID
Unsigned 8
RW
N
127
Minimum CAN ID no. of
the slave axis.
2043 03 Slave maximal node
ID
Unsigned 8
RW
N
127
Maximum CAN ID no. of
the slave axis.
2043
04
Slave error
Unsigned 8
RW
N
0
0
Æ
Fault-free slave
1
Æ
Faulty slave
2043
05
Master status word
Unsigned 16
RW
Y
0x0027
Master axis status word.
2043 06 Master: current
position
Signed 32
RW
Y
0
Current position of the
master axis.
2043 07 Following error
window
Unsigned 32
RW
N
10000
Position window for the
monitoring of the gantry
axis.
2043
08
Following error
Signed 32
RO
Y
0
Current deviation of
position between the
master and the slave axis.
2043
09
Help variable
signed 32
RW
N
0
Help variable for the
synchronisation process.
2043
10
Max. following error
signed 32
RW
N
0
Max. deviation of position
between master and
slave.
2043
11
Coupling factor
unsigned 8
RW
N
4
Coupling factor with
master axis.
2043 12 Homing Follow Error
Check (Dummy)
Unsigned 8
RW
N
1
Homing Follow Error
Check (Dummy)
With the help of the synchronous control objects given above, the ISEL CNC control realises the operation
of the gantry axis. The “Synchronous Mode” object is set during the CNC operation by the control, if
applicable. Currently, up to 2 gantry axes are allowed per machine. The CAN node ID of the slave axes
are stored in the “Slave minimal node ID” and “Slave maximal node ID” for the monitoring of errors. The
“Slave Error” object is only used by one master axis. If the related slave axis is faulty, this object is set in
the master. In a slave axis, this object is of no importance. During the gantry, the slave axis receives the
status as well as the current position of the master axis in the objects “Master: status word” und “Master:
current position”. By means of these two objects, the slave axis recognises, if the master axis is faulty or
not and if the deviation of position between the master and the slave exceeds the limit value in the
“Following error window” object or not. The current value of the deviation of position between the master
and slave can be seen in the “Following error” object. The “Help variable” sub-index is intended for
internal use only. The “Max. following error” sub-index of the slave axis is an auxiliary means for the
commissioning. The user can launch the DCSetup in the declaration mode and this variable indicates the
maximum deviation of position between the master and the slave. The seven objects mentioned last are
used only by one slave axis. In the master operation, they are not taken into account.
With the exception of the two objects “Following error window” and “Coupling factor”, all objects of the
synchronous control are commissioned during operation by the ISEL CNC control. In the “Can
Interpolation” dialogue box of the slave axis, the position error of a gantry axis can be defined as a value
for the “Following error window” object and the coupling factor of the slave as the value of the “Coupling
107
Содержание IMD1
Страница 1: ...DC servo positioning module with CanOpen interface UVE8112 IMD10 www isel com ...
Страница 66: ...DcSetup programme Positioning module UVE8112 IMD10 66 ...
Страница 113: ...Positioning module UVE8112 IMD10 Appendix 113 Appendix UVE8112 package dimensions ...
Страница 114: ...Appendix Positioning module UVE8112 IMD10 114 IMD10 package dimensions ...