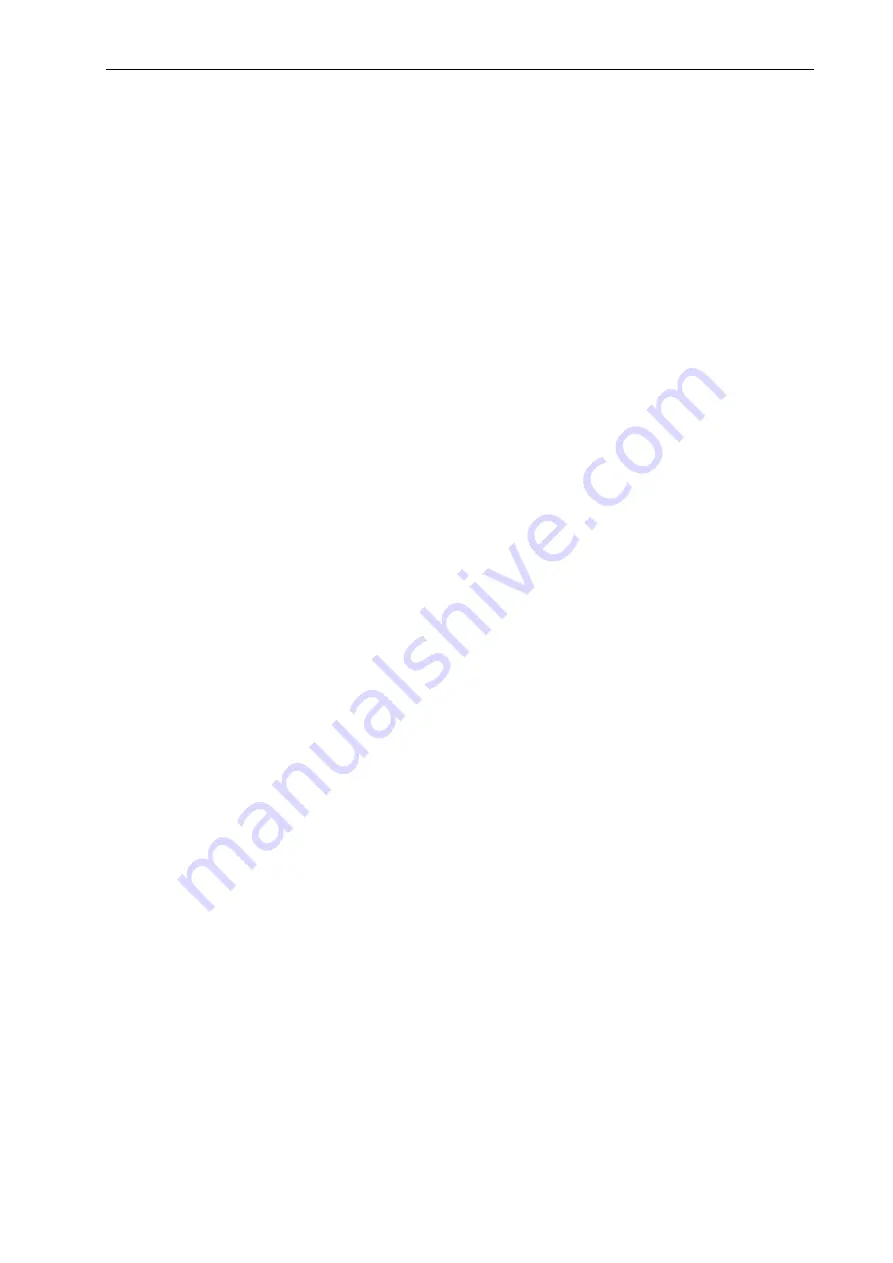
Positioning module UVE8112, IMD10 DcSetup
programme
mechanical axis during the reference run. In case of a reference run with index signal first the axis
reference distance and then sets the zero point of the axis. To determine the index offset first
you have to drive a reference run without index signal and then a reference run with index signal
(Dialog "Determine Index Offset" over button "Determine Index Offset ..."). After completion of the
both reference runs the index offset is determined by the positions the reference runs have reached.
For this the difference position of the two reference runs is calculated. If the difference position is
encoder resolution the index offset is set to
ifference position is out of this range the index offset is set to 1/2 encoder resolution.
pectivly changed index offset into the dialog
"Reference Run".
The dialogue box comprises all parameters influencing the execution of the reference run. By means
of <Type and direction of the reference run>, you define e.g. which switch is used and in which
direction the axis is to go. In order to achieve a high precision of the machine’s zero point, a
combination with the index signal is possible, provided the index signal is connected to the encoder.
be set here. Furthermore, there is the possibility
st the reference run.
, during the reference run, the
In case of a gantry axis, the master and slave axis may have different motion parameters and
rence run have to be identical for both axes. On the
the values indicated, the control calculates the optimum motion behaviour for both axes. The
Obj
The Object Directory dialogue box shows a tree view of all parameters (CanOpen objects) of the
drive module. Via this structure, you can directly access all objects and read and / or write the
parameter according to the respective characteristics. A description of all objects can be found in the
“Object Directory” chapter on page 78. Only users experienced in CanOpen standards may use this
dialogue box in order to set parameters. All other users shall realise the setting of parameters via the
“Commissioning” dialogue box (see Commands of the Commissioning menu on page 33).
The tree view on the left side is subdivided into Communication (DS301), Device Profile (DS402) and
Manufacturer-Specific Objects. On the right side, the characteristics and the content of the currently
selected object are displayed. By means of the <Assume> button, you can realise changes in the
current parameters. <OK> also confirms the current change and closes the dialogue box.
The “
Always update
” option has the effect that the value of the currently selected parameters is read
about 5 times per second from the drive module (in case of an enabled online mode).
Via the “
Save current values in module
” button, you can permanently store the currently set values
(set of parameters) in the drive module (the storing of individual parameters is not possible).
moves after switch off to the index offset without considering the index signal. After this the axis
moves as long as it recognizes the index signal. After recognition of the index signal the axis moves
to the
between 1/4 of the encoder resolution and 3/4 of the
zero. If the d
With "Assume Index Offset" you can assume the set res
Likewise, the speeds and the reference distance can
to te
Internally, the module is switched to the Homing Mode – Reference run CanOpen mode of operation
for the execution of the reference run; then the reference run is started and, after its termination, the
previous mode of operation is switched back to.
In case of a reference run on one of the two limit switches, note that
output for the shunting of the limit switch (safety circuit) is set in order to prevent the final stages from
switching off, when the limit switch is activated.
reference methods. Only the directions of the refe
basis of
reference distances can be used in order to adjust the deviation of position of both axes in the zero
point.
ect Directory dialogue box
65
Содержание IMD1
Страница 1: ...DC servo positioning module with CanOpen interface UVE8112 IMD10 www isel com ...
Страница 66: ...DcSetup programme Positioning module UVE8112 IMD10 66 ...
Страница 113: ...Positioning module UVE8112 IMD10 Appendix 113 Appendix UVE8112 package dimensions ...
Страница 114: ...Appendix Positioning module UVE8112 IMD10 114 IMD10 package dimensions ...