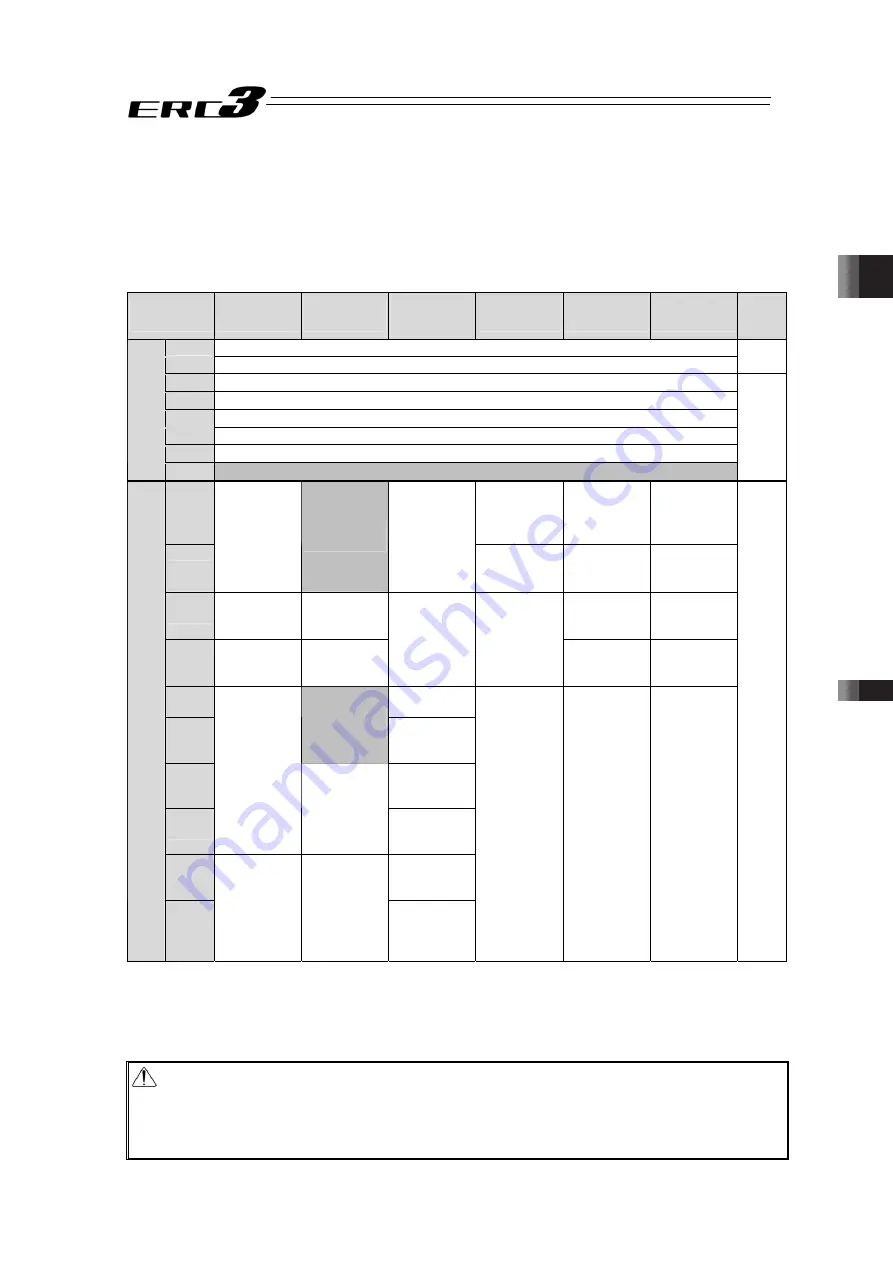
Chapter 3 Operation
3.4 Field Network
Address Map
65
3.4 Field Network Address Map
3.4.1 PLC Address Construction by each Operation Mode
The PLC address domain to be occupied differs depending on the operation mode.
Refer to the example in Section 3.4.2 for the assignment.
• PLC Output → ERC3 Input (n is PLC output top word address to ERC3)
(Note 1)
PLC Output
Area
Simple Direct
Mode
Positioner 1
Mode
Direct
Indication
(Full) Mode
Positioner 2
Mode
Positioner 3
Mode
Remote I/O
Mode
(Note 2)
Details
n
Gateway Control 0
n+1
Gateway Control 1
3.4.3
n+2
Command
n+3
Data 0
n+4
Data 1
n+5
Data 2
n+6
Data 3
ERC3 Gateway C
on
tro
l A
rea
n+7
Occupied Area
(Note 3)
3.4.9
n+8
Specified
Position No.
(Axis No.0)
Control
Signal/
Position No.
(Axis No.0)
Assignment
Area for Axis
No.0
n+9
Target
Position
(Axis No.0)
Occupied
Area
(Note 3)
Target
Position
(Axis No.0)
Control
Signal
(Axis No.0)
Assignment
Area for Axis
No.1
Assignment
Area for Axis
No.1
n+10
Specified
Position No.
(Axis No.0)
Specified
Position No.
(Axis No.0)
Assignment
Area for Axis
No.2
Assignment
Area for Axis
No.2
n+11
Control
Signal
(Axis No.0)
Control
Signal
(Axis No.0)
Positioning
Width
(Axis No.0)
Assignment
Area for Axis
No.1
Assignment
Area for Axis
No.3
Assignment
Area for Axis
No.3
n+12
Speed
(Axis No.0)
n+13
Occupied
Area
(Note 3)
Acceleration/
Deceleration
(Axis No.0)
n+14
Pressing
Current Limit
(Axis No.0)
n+15
Assignment
Area for Axis
No.1
Assignment
Area for Axis
No.1
Control
Signal
(Axis No.0)
n+16 to
n+23
Assignment
Area for Axis
No.1
Con
necte
d
Axes Control
Area
n+24 to
n+71
Assignment
Area for Axis
No.2 and
later
Assignment
Area for Axis
No.2 and
later
Assignment
Area for Axis
No.2 and
later
Assignment
Area for Axis
No.2 and
later
3.4.4
to
3.4.8
(Note 1) For CC-Link, n and n+1 are for input and output bit addresses, and n+8 is for the top
address of data register.
(Note 2) Remote I/O Mode occupies 12 words no matter how many axes are connected.
(Note 3) This is the
area
occupied unconditionally. Therefore, this
area
cannot be used for any
other purpose.
Caution : 1) Remote I/O Mode cannot be used together with other modes.
2) Only Remote I/O Mode can be selected in MEC Mode Type.
3) Only Positioner 3 Mode and Remote I/O Mode can be selected in
MECHATROLINK and CompoNet. (CompoNet occupies 32 bytes no matter of the
number of axes.)
ME0302-4A
Содержание ERC3
Страница 1: ...IAI Corporation ERC3 Gateway Unit Instruction Manual Forth Edition ...
Страница 2: ......
Страница 4: ...ME0302 4A ...
Страница 8: ...ME0302 4A ...
Страница 35: ...Chapter 1 Specifications Check 1 6 Option 27 1 6 Option はケーブル長 ME0302 4A ...
Страница 54: ...Chapter 2 Wiring 2 3 Wiring Method 46 ME0302 4A ...
Страница 158: ...Chapter 3 Operation 3 8 Field Network LED Indication 150 ME0302 4A ...
Страница 160: ...Chapter 4 I O Parameter 152 ME0302 4A ...
Страница 176: ...Chapter 5 Troubleshooting 5 4 Alarm List 168 ME0302 4A ...
Страница 186: ......
Страница 187: ......