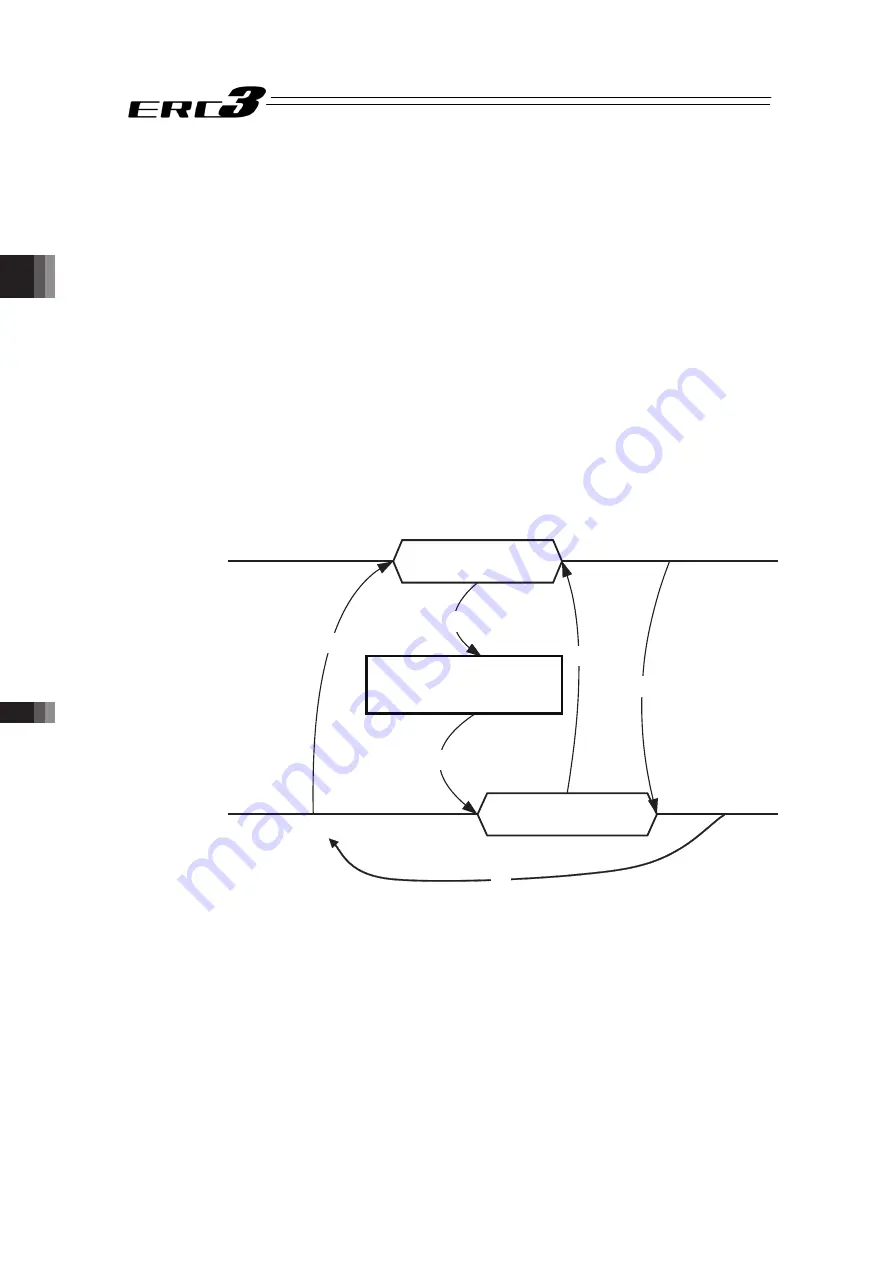
Chapter 3 Operation
3.5 Input and Output Signal Process for Field Network
120
(2) Command Sending and Receiving Timing (Reading and Writing of Position Data and Reading of
Alarm Axis)
By writing and reading the specified commands to the area of 5-word next to Gateway
control/status area, reading and writing of the position data and reading of alarm axis can be
conducted.
Gateway executes the command every time the control/status data exchange finishes for all the
axes. [Refer to Section 3.4.9 About Command.]
● Step
1) PLC confirms the area of response command is 0.
2) PLC sets the necessary commands and data to the indicated area and send them.
3) Gateway detects that the area of the command has become other than 0, and rewrites the
appropriate axis data if it is the writing command, and reads the requirement data from the
appropriate axis if reading command.
4) Gateway output the response result to PLC once the command is executed.
5) Once PLC has confirmed the response result, clear the area for the command to 0.
6) Gateway clears the response command area to 0 and waits for the next command after it
detects the command is cleared.
The procedures from 1) to 6) are repeated when continuously used.
Command and Data
1)
2)
3)
Response Command
and Response Data
4)
5)
Response Command Area = 0000
H
Gateway executes the reading
of each axis and data following
the command.
Command Area = 0000
H
6)
PLC side
ERC3
Gateway side
ME0302-4A
Содержание ERC3
Страница 1: ...IAI Corporation ERC3 Gateway Unit Instruction Manual Forth Edition ...
Страница 2: ......
Страница 4: ...ME0302 4A ...
Страница 8: ...ME0302 4A ...
Страница 35: ...Chapter 1 Specifications Check 1 6 Option 27 1 6 Option はケーブル長 ME0302 4A ...
Страница 54: ...Chapter 2 Wiring 2 3 Wiring Method 46 ME0302 4A ...
Страница 158: ...Chapter 3 Operation 3 8 Field Network LED Indication 150 ME0302 4A ...
Страница 160: ...Chapter 4 I O Parameter 152 ME0302 4A ...
Страница 176: ...Chapter 5 Troubleshooting 5 4 Alarm List 168 ME0302 4A ...
Страница 186: ......
Страница 187: ......