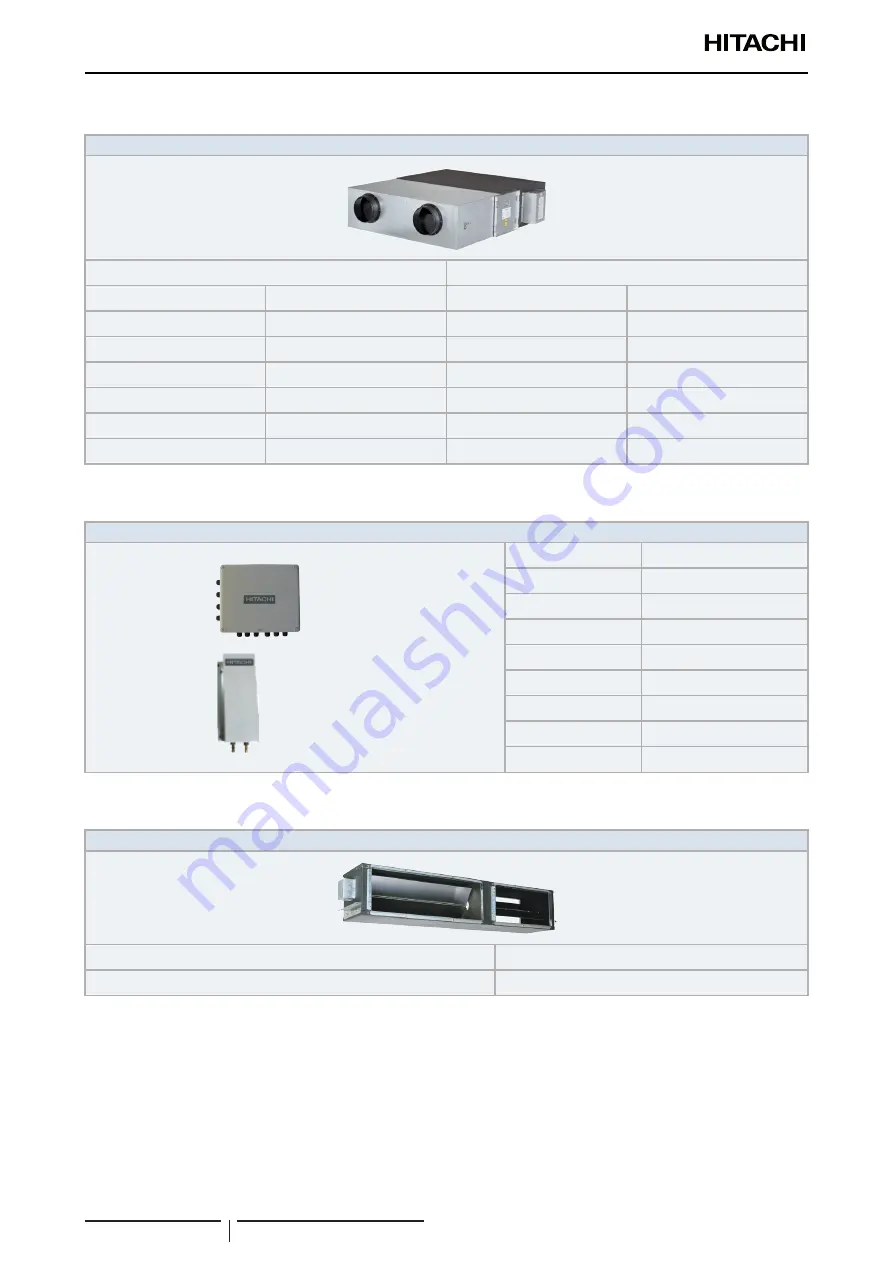
1 General information
Product classification and line-up
SMGB0137 rev.0 - 05/2021
10
1.4.6
Product line-up: KPI energy recovery unit
KPI
Energy recovery
Active (Energy R R410A DX section)
Unit
Code
Unit
Code
KPI-252E4E
70603000
KPI-502E4E
70603001
KPI-502X4E
70603201
KPI-802E4E
70603002
KPI-802X4E
70603202
KPI-1002E4E
70603003
KPI-1002X4E
70603203
KPI-1502E4E
70603004
KPI-2002E4E
70603005
1.4.7
Product line-up: DX-Interface
DX-Interface (R410A)
Control box
Expansion valve box
Unit
Code
EXV-2.0E2
7E611000
EXV-2.5E2
7E611001
EXV-3.0E2
7E611002
EXV-4.0E2
7E611003
EXV-5.0E2
7E611004
EXV-6.0E2
7E611005
EXV-8.0E2
7E611006
EXV-10.0E2
7E611007
1.4.8
Product line-up: Econofresh
Econofresh (R410A)
Unit
Code
EF-456N1E
7E560001
?
N O T E
The EF-456N1E unit can only be installed in combination with the following units:
• RPI-4.0FSN6E-EF (7E426027)
• RPI-5.0FSN6E-EF (7E426028)
• RPI-6.0FSN6E-EF (7E426029)