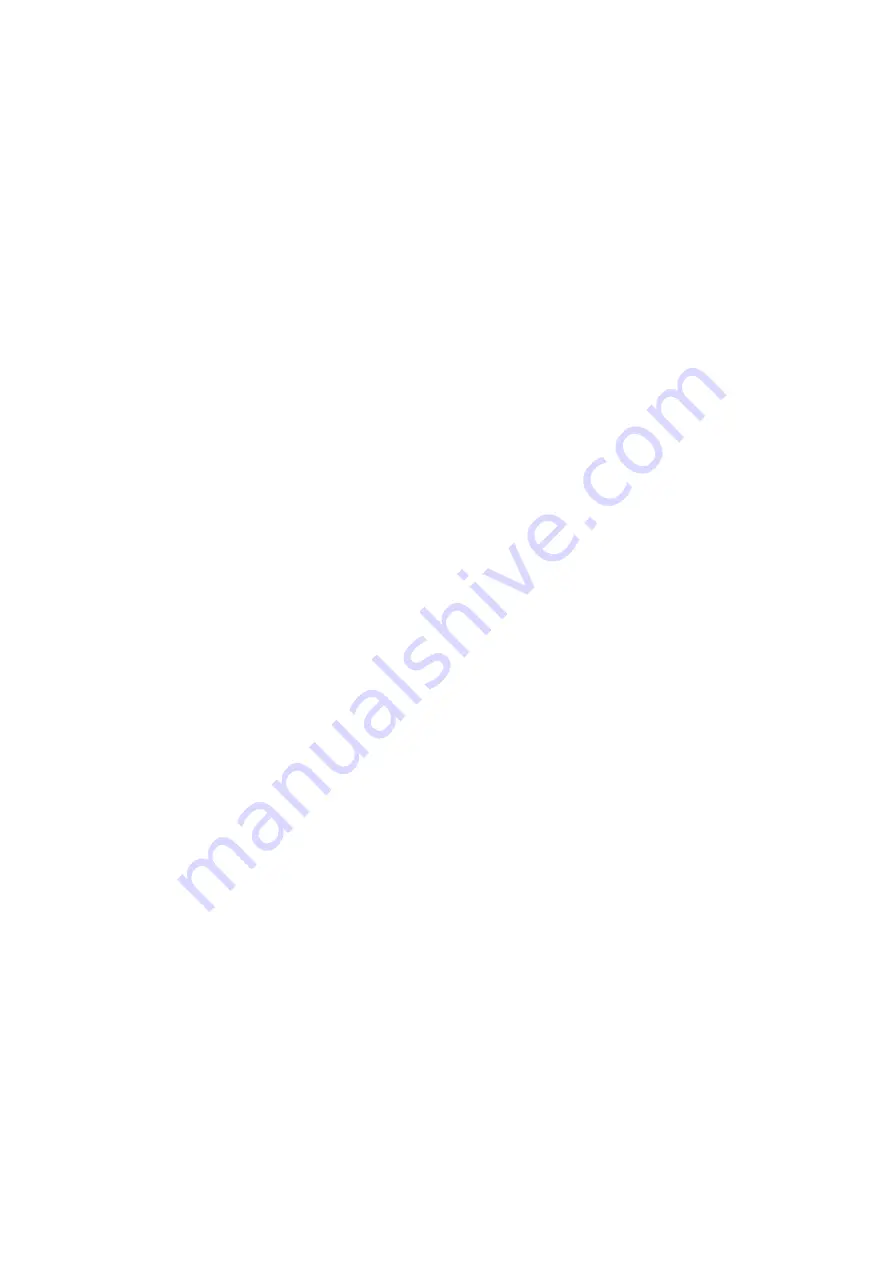
73
Further details about those sensors and devices connections are indicated on
the wiring diagrams.
NOTE: Some other devices not listed here above, such as the ones for the
emergency procedures, are also indicated by the wiring diagrams.
9.6
INCLINATION SENSOR SYSTEM
The inclination system is composed by inclination sensor (one each axles) and
the master board (ECM1).
Inclination sensor detects the machine inclination on both axels, each axles
sensor has a double line, the two signals are compared verifying their
coherency (same values within a certain tolerance), then they are translated
by the inclination sensor itself into one value for
“X” inclination and
one value
for
“Y” inclination
.
Then those two values (X and Y) are communicated to the master board
(ECM1).
Depending on the machine condition, if an inclination is exceeding the limit or
in case of anomalies such as a discordance between the two lines machine will
avoid the movements showing an error message.
ECM1 must be calibrated with the inclination sensor, in case of one of these
components need to be replaced the calibration must be carried out as indicated
by the APPENDIX 1.
9.7
LOAD CELL SYSTEM
The load cell system has two components, load cell board (ECM3) and the load
cell sensor.
The load cell sensor is located under the basket and it has four extensimeters
so that send a double signal for both the lines to the ECM3.
ECM3 is located into the jib arm box and it elaborates that double signal
communica
ting it translation in “Kg”
to the master board (ECM1) through CAN-
BUS line.
ECM3 also compares the double signal verifying their coherency (same values
within a certain tolerance).
ECM3 must be calibrated with the load cell sensor, in case of one of these
components need to be replaced the calibration must be carried out as indicated
by the APPENDIX 2
.
The “0” of the load cell system is settled without the basket, so that with basket
and operator on, the weight read by the relevant input is the sum of them, for
instance with an operator of 80 Kg the load input will show about 130 Kg.
In case of an overcharge (more than about 280 Kg) or in case of anomalies
such as a discordance between the two lines machine will avoid the aerial part
movements showing an error message.
Содержание LightLift 15.70 3S
Страница 1: ...1 TECHNICAL COURSE BOOKLET LightLift 15 70 3S PERFORMANCE TTLL1570021702 ...
Страница 12: ...12 ...
Страница 13: ...13 2 4 LL15 70 WORKING AREA 230 KG UNRESTRICTED CAPACITY ...
Страница 45: ...45 7 4 1 GASOLINE HONDA iGX390 EMERGENCY START ...
Страница 46: ...46 7 4 2 DIESEL HATZ 1B40 EMERGENCY START ...
Страница 49: ...49 8 2 HYDRAULIC DIAGRAM 8 2 1 HYDRAULIC DIAGRAM INDEX ...
Страница 50: ...50 8 2 2 PUMPS AND UNDERCARRIAGE PART HYDRAULIC DIAGRAM TO THE AERIAL PART VALVEBLOCK ...
Страница 51: ...51 8 2 3 AERIAL PART HYDRAULIC DIAGRAM FROM THE DEVIATOR VALVE ...
Страница 108: ...108 CELLS PACK WITHOUT COVER ...